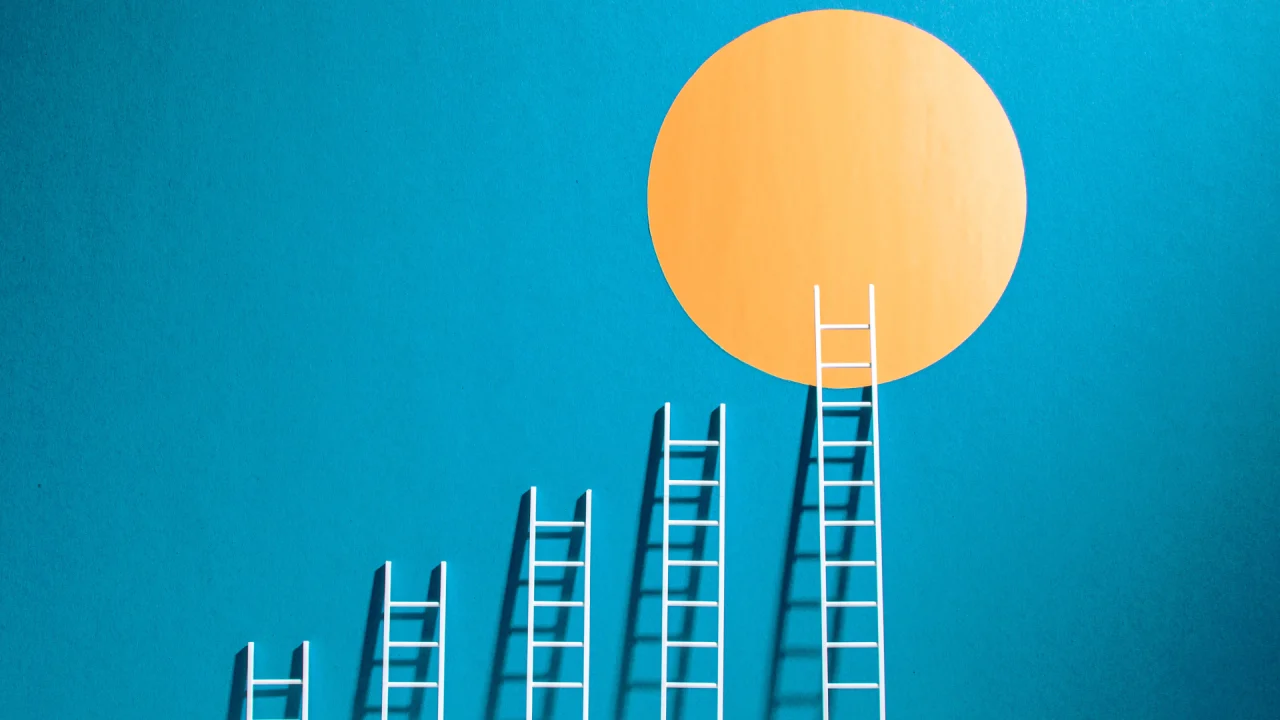
How to motivate staff when automating your business
www.fastcompany.com
Clearly, automation will affect labor in 2025. But we maintain that when implemented well, automation elevates our employees and empowers our American workers to make U.S. businesses more competitive on the global stage.This is our why. Now Chang Robotics president, Kate McAfoose, will address the how. These are remarks she shared at a recent Delaware Valley Goods Movement Task Force quarterly meeting panel.New automation brings new challengesYes, new challenges emerge with increased automation and digitalization. As an engineering firm, our company is coming from an engineering culture into companies ranging from manufacturing to warehousing, transportation, e-commerce, healthcare, and government spaces. Many are Fortune 500; some are smaller, but the challenges they face are the same:They want to maintain staffing from within their regions, but they must be sure theyre meeting quality requirements and regulatory benchmarks.They want to build a resilient supply chain within the U.S.So how do they transition manual workers to jobs informed by digital technologies?Smart technologies and asking the right questionsAs part of our robotic solutions, we integrate smart sensors, internet of technology (IoT) platforms, data collection, and analysis. We also provide C-suites with a dashboard to track key metrics, and identify areas where performance may be lacking. The dashboard answers questions such as Are we maintaining uptime? Are we meeting production requirements? Are the quality measurements in line?Perhaps the client needs to improve operational efficiency to maintain profitability. In healthcare, nursing staff may be burned out due to a shortage, leading to physical exhaustion or extended shifts. Or a government facility might be readyor requiredto transition to autonomous shuttles.In all cases, the process involves finding the repetitive tasks that are not necessarily high skilled, then finding ways to automate those functions. Now the challenge is to upskill the staff and operators to new trades as were implementing the systems.Training the trainers is keyOur company has a philosophy called train the trainer. As we implement new technology, we walk side by side with the operators for roughly 3-6 months. We make sure they understand and can operate the system; then we help them champion the system. In addition to the new level of employment, they earn the metaphorical badge of honor for having learned a new trade.We focus on empowering employees who can go home and say, My job is cool. I get to work with robots. Its not a situation of humans being replaced by robots, but in positioning them with collaborative robots that can drive efficiency and quality but cannot function without human interaction. If we implement the change in this way, everyone wins.A new world, with room for manyHow many people go through high school thinking, I want to specialize in goods movement or I want to work in automated transport? This is not a career path people have considered as a cool future role. But as these functions become better understood, the respect for their power will grow.There will still be a range of skilled and lower-skilled positions in the automated workforce. More positions will naturally focus on the maintenance and planning of the automated facilities. People will be required to perform maintenance and testing functions and to plan and maintain the spare parts inventory. These roles are vital to the operations success and will naturally gain a much bigger seat at the organizational table.Automation also applies to quality control. For example, if youre automating plasticware production, the utensils must come off the line cleanly, with no excess edges. The moment one piece fails to meet quality standards, it can cause a backup in the entire line, leading to a shutdown and requiring manual labor to resolve the issue. If youre operating with a smaller staff, youll need to pull workers from other areas, further slowing down production. Everyone involved will continually learn and adapt.Jobs remain, but skillsets are shiftingIts critical to avoid the assumption that automation leads to job reduction. Its a drive for as much production and quality enhancement as possible, but it will require a specialized team to achieve. Ideally, its the same team you already have, but differently trained.Traditionally, manual warehouse labor roles have very high turnover. After 6 months, many workers feel the job is repetitive and unappealing, or they leave to avoid night shifts or seek higher pay elsewhere. When this happens, the training investment is lost, and the next employee must be trained. However, when automation is implemented effectively, the need for manual labor decreases. Ideally, this reduction can occur through natural attritionwhen an employee moves on rather than advancing, the company may not need to hire a replacement.Automation can streamline roles that involve heavy lifting, high workplace injury risk, and increased burnout or boredom. People will leave less often. Effective automation can reward companies and workers in new ways.Technology for a bright futureWhat does this mean for our childrens future? Kate has a child in kindergarten right now. I have no idea what she will do. Maybe shell pursue data science or data analysis, but the truth is, the roles of the future most likely dont even exist yet. But they will be necessary. And so will she.We will continually need to strive for the right decisions and balance, with a focus on innovation and action. This is how the next generation of companiesand employeescan continue to win.Matthew Chang is founder and Kate McAfoose is president of Chang Robotics.
0 Reacties
·0 aandelen
·73 Views