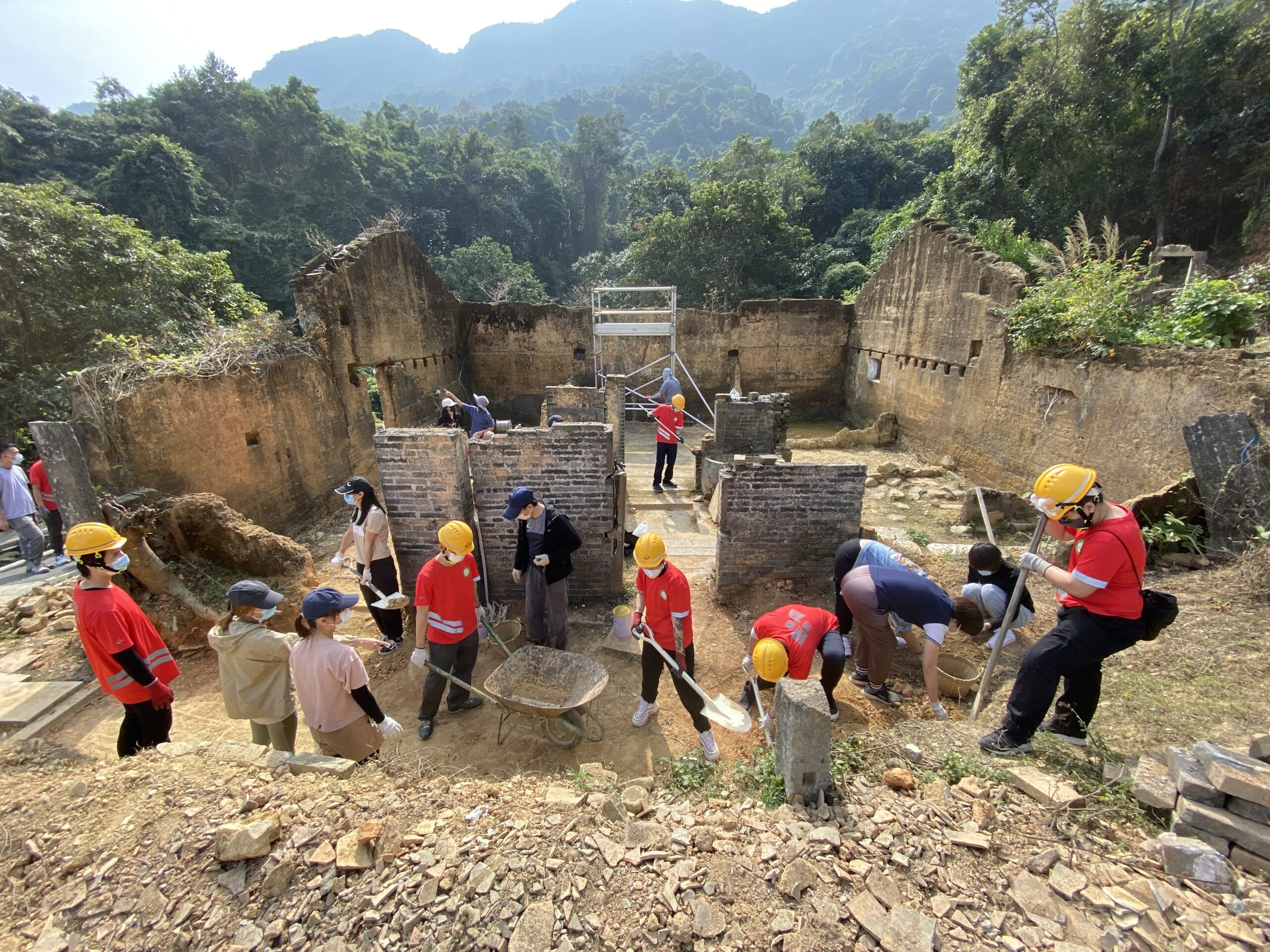
Architecture, Unplugged: Why Forward-Thinking Architects Are Reclaiming the Art of Building by Hand
architizer.com
Architects: Want to have your project featured? Showcase your work by uploading projects to Architizerand sign up for ourinspirational newsletters.In Tokyo, construction is measured in weeks, not years. Its a place where efficiency is often valued above artistry. Its a place where Keisuke Okas Arimaston Building really shouldnt exist.A structure built entirely by hand over two decades, with no formal plans, no digital modeling and certainly no construction teams working to a deadline, the Arimaston Building is the product of one mans patience, skill and refusal to conform to a system that treats architecture as an industrial process rather than the art of creation.The walls are notoriously irregular and the concrete surfaces are textured with imprints from makeshift molds. Things like food trays, scrap metal and whatever was available at the time were used. It is a building that quite literally tells the story of its own making. Unlike the typical Tokyo towers, all sharp angles and glass, the Arimaston Building is a record of human decision-making at every stage.Yet, instead of being seen as an argument for the enduring intelligence of craft, Okas project is treated as an eccentricity, an exception rather than a viable approach to building. It is part of a wider issue that has grown within architecture: the systematic replacement of craft, material knowledge and human adaptability with automation, prefabrication and algorithmic efficiency. Architecture has gradually become a profession that has distanced itself from the act of making and, in doing so, has lost something fundamental knowledge.Project Plum Grove by School of Architecture, The Chinese University of Hong Kong, Hong KongHandcraft is not a novelty. It is a way of building that has been refined over millennia, guided by material intelligence, regional conditions and cultural heritage. To treat it as obsolete is to ignore the very basis of architectural and human evolution. Unfortunately, many architects assume that just because something can be mechanized, it should be.At Sacsayhuamn in Peru, Inca stonemasons created a fortress of stone blocks, each weighing several tons and precisely fitted without mortar. These structures, built over 500 years ago, have withstood centuries of earthquakes that would have flattened modern buildings. Each stone was shaped one at a time to fit perfectly with the previous one to create a structure without weak points, enabling it to absorb seismic forces with ease.I,Ruud Zwart,Djenne great mud mosque,CC BY-SA 3.0The Great Mosque of Djenn in Mali, first built in the 13th century, isnt the same building as it was when it was first erected. Like a living system, each year, the local community gathers to apply fresh layers of mud plaster, renewing the structure that has eroded due to flooding or weather conditions. The result is an architecture that is the opposite of disposable, a building designed to last indefinitely, provided its users remain engaged with its care.Compare those examples to the standard lifespan of contemporary buildings. Many are engineered for obsolescence. The industrialization of architecture was sold as a step forward, but much of the real gain was not for architects or buildings. It was for developers and manufacturers. The faster a building can be constructed, the sooner it can be sold or leased. The less skilled labor is required, the cheaper the project is overall. The more standardized the materials, the easier they are to replace rather than repair.This shift has had consequences for our built world. Prefabrication and digital workflows have distanced architects from the very materials they specify. Few will have worked with the stone, timber, or concrete they design with. Fewer still will have a working knowledge of the skills required to shape them.A stonemason working with limestone understands how to read the grain of the rock, how it will fracture, how it will weather over time. Carpenters trained in Sashimono learn to build timber structures without nails or adhesives, instead using precise interlocking joints that can be undone. These structural solutions, refined over centuries, make buildings more durable, movable and repairable.Limestone Gallery by He Wei Studio3andwich Design, Anlong, Qianxinan, ChinaThere is an argument that modern digital modeling tools now allow architects to analyze materials in ways that were previously impossible. AI can optimize timber cuts to minimize waste, robotic arms can carve stone with sub-millimeter precision, and parametric modeling can predict structural stress with near-perfect accuracy. But analysis is not intuition. A craftsman working directly with materials develops an embodied knowledge of their behavior: how they flex, resist, expand, and decay.It is not that machine-built architecture is bad its just that it has become the default, while anything requiring human craftsmanship is treated as a luxury. Its expensive, slow, and very often looked at as impossible.Yet sometimes, like the Arimaston Building, exceptions can prove that handbuilt can be just as effective and the alternative. Limestone Gallery in Xiadi Village, China, is suspended on a clifftop of 100 meters above a river. A precarious site that is difficult to reach and complicated to work with. It required a large portion of the construction work to be done manually by local laborers. Adjusting and adapting the process as the site was developed. The gallery now fits perfectly in its location.Sail Houseby David Hertz Architects, Studio of Environmental Architecture, Saint Vincent and the Grenadines | Photo by Kevin Scott PhotographyOr in Bequia, Saint Vincent and the Grenadines, where Sail House combines modern design strategy with traditional hand-building methods. Designed by David Hertz Architects, the nautical-inspired buildings took into consideration the difficulty of construction in the Caribbean with its limited resources. It was decided that the buildings should be prefabricated in Indonesia and then shipped to the site. On arrival, the buildings were assembled by hand in just two months. One of the main benefits of this type of construction is that these structures can be disassembled just as they were assembled, and individual sections can be repaired or replaced as they wear.If architecture is to retain its material intelligence, its authorship, and its connection to place, it should not fully surrender to mechanization. These projects show that hand-building is far from an obsolete tradition and when combined with modern techniques, it is a choice that remains entirely viable for architects. The problem has never been technology itself and handcraft should not entirely reject innovation. What it should reject is the idea that efficiency is the only measure of value. That speed matters more than longevity. That cheapness is an acceptable substitute for quality.Architects: Want to have your project featured? Showcase your work by uploading projects to Architizerand sign up for ourinspirational newsletters.The post Architecture, Unplugged: Why Forward-Thinking Architects Are Reclaiming the Art of Building by Hand appeared first on Journal.
0 Comments
·0 Shares
·25 Views