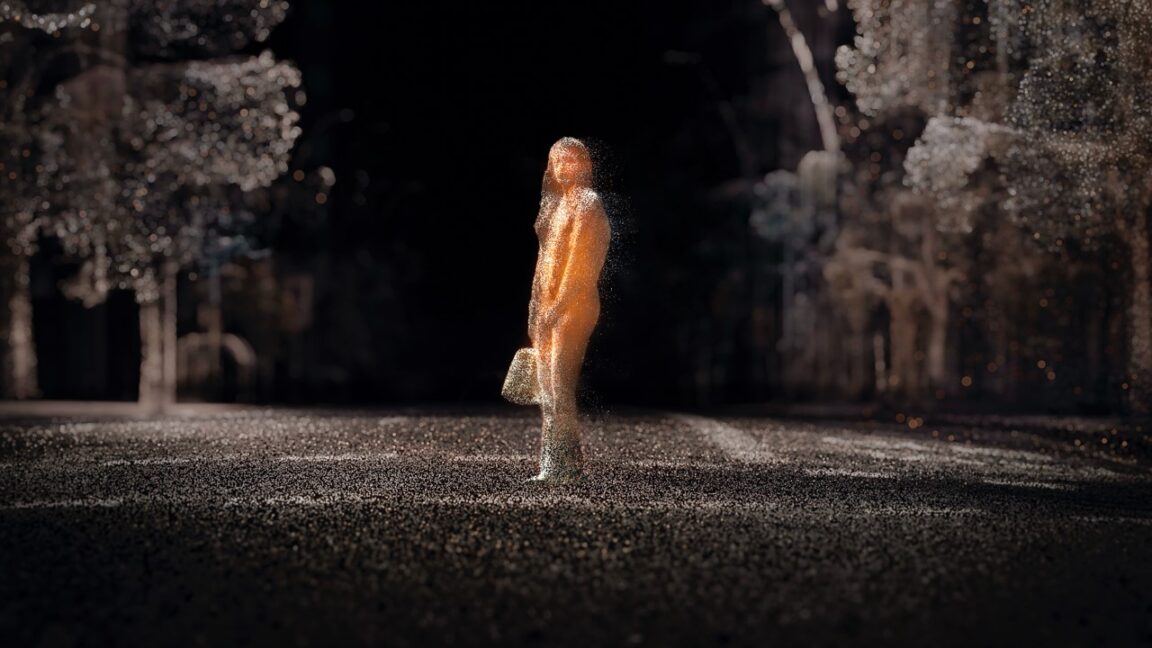
Volvo is using Gaussian splatting in virtual worlds to make safer cars
arstechnica.com
yes, gaussian splatting Volvo is using Gaussian splatting in virtual worlds to make safer cars Massive parallel testing means Volvo can work through lots of unusual scenarios. Jonathan M. Gitlin Mar 19, 2025 11:32 am | 6 Credit: Volvo Cars Credit: Volvo Cars Story textSizeSmallStandardLargeWidth *StandardWideLinksStandardOrange* Subscribers only Learn moreSafety is Volvo's big thing. From three-point seatbelts to side-impact protection to blind-spot monitoring and much more, the Swedish automaker focuses its innovation on making its cars safer rather than faster around the Nrburgring. (Although in the past, it has set records there too.) As part of its efforts, Volvo has collected data from tens of thousands of car crashes, which it's now leveraging in virtual worlds to put simulated cars and SUVs through the wringer with the help of something amusingly named "Gaussian splatting.""We've been visiting crash sites since the '70s. We've been recording event data from a fleet of cars for many, many years," said Alwin Bakkenes, head of global software engineering at Volvo Cars. "And all of those data points have actually helped us create safety innovations... from the three-point safety belt to whiplash protection systems and now also, as we're introducing in the ES90, a function called 'lidar AS,' which helps the car steer away from vulnerable road users in the dark," he said.Like some others in the industry, Volvo is an early adopter of the software-defined vehicle, or SDV. As a quick refresher, SDVs are clean-sheet designs in terms of their electronic architecture. Instead of dozens or even a hundred discrete black boxes, each with its own hardware and running its own software, each doing a discrete job (like controlling the air conditioner or managing traction control), four or five powerful central computers take over those roles, overseeing domains like infotainment, advanced driver assistance systems, handling and powertrain, and interior comfort."One thing is that we develop this in-house now, so instead of relying on suppliers with long deadlines and long process and sending requirements back and forth, we develop the software," said Erik Coelingh, VP of product at Zenseact, an ADAS developer owned by Volvo. Credit: Volvo Cars "If there's something, we solve it in a day," Coelingh said. "It's so much faster. So we iterate much faster. As Bakkenes said, we're all testing with the new software every single day. So the innovation speed is fundamentally different than before, and the way we try to use this is to really build safety and go toward lower accident rates in a pace that we've never seen before."Among the advantages of moving to SDVs is that it's much easier to simulate them since the entire software stack can be run virtually. That's why Volvo has built one of the largest data centers in Europe: to be able to run those sims.Like a lot of other companies out there, Volvo has turned to AI to speed up the development process. But how does such a safety-conscious company like Volvo know it can trust the output of those end-to-end algorithms?"Gaussian splitting is a technology where we can take one point, one traffic scenario, and explode it into thousands or tens of thousands of scenarios from this real-world data," Coelingh said. "And then we can manipulate one scenario into a thousand different scenarios, and then we can enclose the simulation and test our software against this."Autonomous vehicle developers have been simulating in environments like Unreal Engine for some time now. "That's very visual; that works for camera data. But here we're probing lidar data, camera data, radar data, and we reconstruct the scene with the neural net, and then do the manipulation and use closed-loop simulation," Coelingh said. "So this is a way of, really fast, be able to test your software against a huge, huge amount of different scenarios that are representative for the real world." An example of some Gaussian splatting scenarios. Credit: Volvo Cars The first neural radiance fields were able to interpolate 3D objects from an input of 2D images taken from different angles. "So instead of doing all the physics calculations on how the rays bounce and all this, instead, you train a neural network to learn the static scene," Coelingh said. "The next step was to build NeRFs in 4Din space time. So we are using this for, let's say, a camera sequence of 10 seconds, and then you can, in time, reconstruct this."Running the original data with the original conditions in simulation lets Volvo check that the simulation is faithful enough to recreate the original outcome. From there, it can start changing conditions, rerunning the test to see how (or if) the car's behavior changes. By doing the same for radar and lidar data as well as camera data, "we can reconstruct the scenarios that the car sees in reality... with all the strange things that happen in the real world," Coelingh said."We have our millions and millions of data points where we actually have events that we collect from our fleet," Bakkenes said. "When we find something the system finds difficult to deal witha scenariothen we can zoom into one of those scenarios with all the sensor data, and we can explode that into a thousand variants of that particular scenario."Virtual testing with Gaussian splatting has not replaced real cars driving on the test track, but it does let Volvo test new cars in a much wider range of conditions than would otherwise be possible.Jonathan M. GitlinAutomotive EditorJonathan M. GitlinAutomotive Editor Jonathan is the Automotive Editor at Ars Technica. He has a BSc and PhD in Pharmacology. In 2014 he decided to indulge his lifelong passion for the car by leaving the National Human Genome Research Institute and launching Ars Technica's automotive coverage. He lives in Washington, DC. 6 Comments
0 Commentarii
·0 Distribuiri
·31 Views