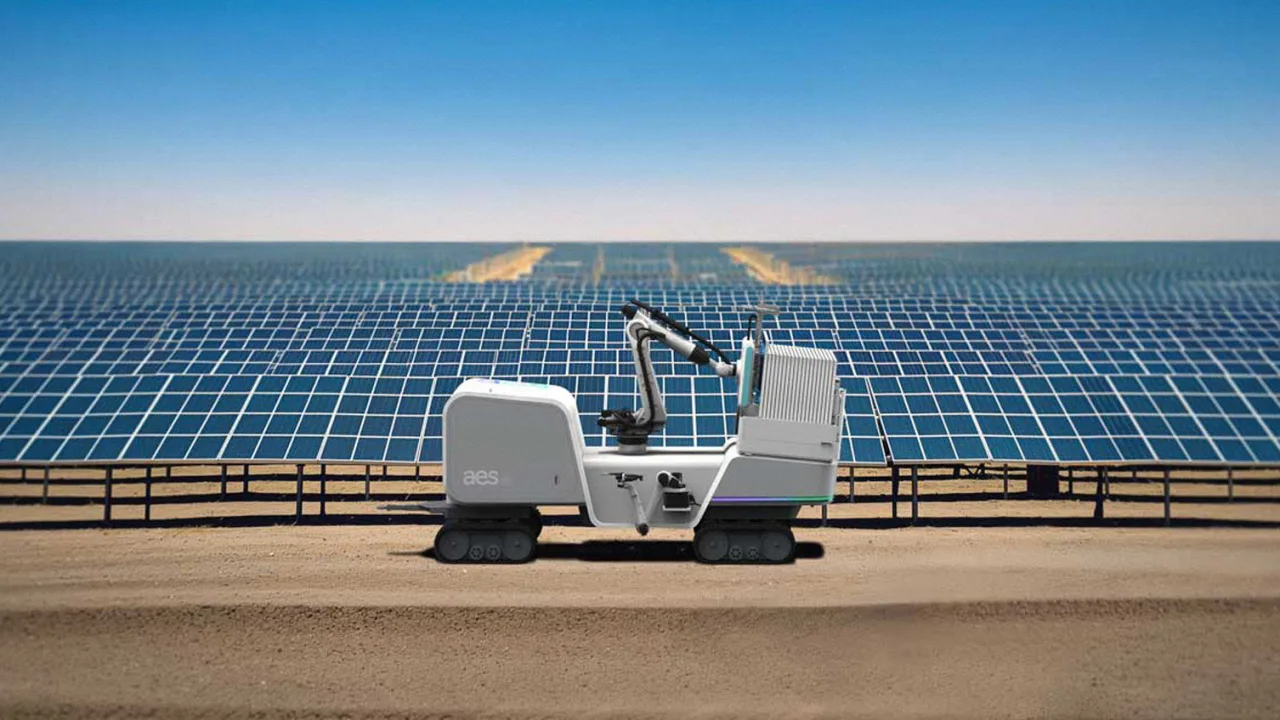
WWW.FASTCOMPANY.COM
The world needs more solar farms. This rolling robot is here to help
The worlds hunger for energy is growing at an unprecedented rate thanks to growing manufacturing and AI data centers. And our current electric generation capabilities just cant cope with the demand. The situation is so dire that the International Energy Agency predicts a tripling of solar panel installations in ten years, a surge that will require a near doubling of the workforce. The U.S. solar industry is currently installing approximately 15,000 modules per hour which is laughable when industry experts are saying it needs to reach a staggering 50,000 modules per hour by 2035 to keep up with electricity demand.The reality is that humans cant build wind and solar farms fast enoughwhich is why utility and energy generation company AES has invented Maximo, an AI-powered robot designed to double the speed of solar farm deployment. Building a solar farm requires moving and installing modules weighing more than 60 pounds and measuring an unwieldy 6.5 x 3.25 feet each. Its a tedious and potentially dangerous task. Maximo (nicknamed Max) is a medium-to-large, light gray robot that runs on two sets of tracks that is designed to make that operation a breeze. [Image: AES]Its boxy chassis with curved corners has a central platform that holds the multi-jointed robotic arm that lifts and places the solar panels. Small sensor modules dot the robot, mapping its surroundings so it knows where it is at all times as it reaches into the cradle on its back that holds the panels. Its a machine that looks like the future, thanks to the design work of industrial and brand design studio Fuseproject.Introduced last summer, AES says Maximo has become the first proven solar installation robot on the market. And while the company claims that Maximo isnt intended to replace human workers, it doesnt really need to. The solar industry faces an extreme shortage of skilled labor, so it cant tackle the sheer scale of the task at hand without using machines like this smart buggy with robotic eyes and arms.The genesis of Maximo began two years ago, as Yves Bhar, founder and principal designer of Fuseproject, told me during an interview. We had a really interesting initial discussion about increasing the capacity of solar power and making it more efficient, Bhar says. His experience with robotics and electric vehicles made the project particularly appealing to him. The combination of vehicle and robotics really at the service of accelerating the installation and the capacity of solar energy was something that I was very, very interested in.[Image: AES]Design principlesThe design process focused on several key principles. Scalability was paramount, as was seamless integration into existing workflows. Crucially, Maximo needed to be friendly in the field, a trustworthy friend to the human workers it would collaborate with. Its not meant to replace workers, Bhar says. Its really meant to complement. Its a tool to accelerate the transition to renewable energy, reducing the physical demands of having to lift panels [and accelerating the installation].Fuseproject wanted to give Maximo a distinct identity aligned with AESs brand, while following very specific function requirements to maximize efficiency in the movements and manufacturing cost-effectiveness. The design needed to be scalable, too, as the vision was to have an army of bots covering deserts and plains with oceans of dark silicon panels.One of the most important criteria was to visually integrate all the different parts, Bhar explains, as Maximo is basically a tank platform that needs to carry a lot of eclectic components. It has two mechanical arms for installation, a cradle that holds all the panels that need to get installed, the power unit, and the AI module. Bhar tells me that these disparate elements needed to be tied under a single form. His team came up with a metallic sine wave-shaped ribbon that expresses what the product does, while also providing essential protection from the elements.This continuous form turned out to be the most visually significant element of the robot. Deise Yumi Asami, AESs founder, says that Fuseproject did a phenomenal job on really getting into the fundamentals of what we wanted to convey with Maximo. The sine wave-like design incorporated into Maximos shape is a subtle nod to the alternating current of electricity. Its really tied to our core existence of energy, she explains.Other design elements, such as the aqua color, references the AES logo. The specific shade was carefully chosen, Asami explains, as was the light gray color of the main body: White on the construction site can be very challenging, so Fuseproject helped them tune the color to a very light color of gray that would, you know, be enough to meet our kind of like this kind of clean futuristic visuals of Max.[Image: AES]How it worksMaximos functionality is as important as its form. The ribbon sine wave, for example, also houses an integrated LED safety system that signals when human workers can approach Max. That was another core requirement from AES: The robot needed to be field-friendly, especially when its volume and power is so unwieldy. Max was really developed to carry all the heavy lifting, but not only that, it had to really accelerate the pace in which we are installing solar panels, Asami tells me. Maximo moves on its own, recognizing the terrain around it. An operator simply engages a safe switch just in case something bad happens and then Maximo takes over the entire operation thanks to a combination of computer vision, artificial intelligence, and a behavioral tree the company developed with Amazon AWS. It knows where to go. And it will decide whats the best path from path A to path B, Asami says. This allows Maximo to operate in the dynamic, uncontrolled environment of a construction site, a key difference from typical factory robots that are fixed in a single point and perform repetitive tasks always in the same place. This outdoor operation presented the most significant technological challenge, Asami says, requiring the development of robust AI and computer vision systems capable of handling glare and other visual issues that happen under different weather conditions and the changing position across different terrains.Safety was the third core requirement, not only through the integrated LED light system integrated in the ribbonwhich turns red, signaling to workers to maintain a safe distance when Max is working, even if its not movingbut with ultrasonic sensors that detect if anyone enters the operating zone, triggering an immediate stop. We have an abundance of redundancy, Asami points out.[Image: AES]The cradle that holds the solar panels was a unique design challenge. It seems like its the only module not perfectly integrated in the design. When I told Asami and Bhar, they acknowledged that there was no way around this, as it needed to adapt to different panel sizes. It needs to be continually accessible too, Asami says. And mechanically speaking, it adjusts to the different sizes of the solar modules.[Image: AES]The adaptability of every aspect of its design is key to Maximos autonomous nature. When it arrives to the solar farm, a worker carefully loads a rack of solar panels into the waiting cradle using a forklift. With its cargo secured, Maximo embarks on its journey along the solar farm, relying on its sophisticated computer vision and brain to chart the most efficient course and identify where each panel should go.Once it gets to the first solar array support structure, Maximo uses its arm to pick up a panel from the cradle, smoothly rotating it and carefully placing the panel onto the pre-installed mounting structure, called the torque tube, before securing it firmly in place. The mechanical installation is complete and then, the process repeats. Panel after panel, Maximo moves along the torque tube building the farm. The human operator only acts as a supervisor, ensuring everything runs smoothly, ready to intervene if needed. Once the cradle is empty, a worker reloads, and the cycle begins again.[Image: AES]Shiny skies aheadMaximo has already installed nearly 10 megawatts of solar and is projected to install 100 MW in 2025. From these first experiences, plans are going to be put on warp 9. AES claims it plans to deploy Maximo to help build up to 5 gigawatts of its solar project pipeline over the next three years. While AES isnt disclosing specific production numbers, Asami says they are seriously ramping up production of the robot for their clients.Asamis ambition is to make Maximo a standard in solar farm construction. With the increasing labor shortages in the industry and the growing demand for solar installations, it seems that it is going to be a must have rather than a may need. The challenge, she noted, is not just about building more solar farms, but also about bringing them online quickly. The majority of the time that its spent on the site, it is spent on the installation of solar modules, she explains, making Maximos contribution to installation speed crucial. We do believe that Max will have a big impact, she says. And thats why we see a lot of emerging competitors as well because everyone understands the need in the industry for something like Maximo. Heres to seeing more of these friendly beasts with their glowing aqua and red ribbons signaling the beginning of a new shiny solar world despite the dark stormy clouds now looming over us.
0 Commentaires
0 Parts
130 Vue