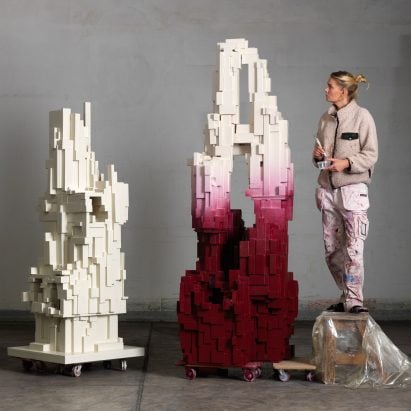
Swedish designers doing things that have "never been done before"
www.dezeen.com
A wave of radical designers in Sweden are experimenting with digital technology and alternative materials to invent new ways of making furniture. Amy Frearson reports.Today's creatives are not just making use of emerging technologies and resources; they are using them to completely overhaul the conventional design process.The growing availability of biomaterials and waste products is leading more designers to adopt a fabric-first approach, allowing the materials to fuel the design direction.Orange rinds, car airbags and oyster shellsMeanwhile, the advancement of technologies such as artificial intelligence (AI), virtual reality and 3D printing has been equally transformative, paving the way for shapes that previously weren't conceivable.In Sweden, designers at the forefront of this trend include Stockholm-based Interesting Times Gang. This innovation-led studio has created products from materials ranging from peeled orange rinds to used car airbags.Interesting Times Gang 3D printed a table from crushed shells. Photo by Caroline Jgborn RungAt the Stockholm Furniture Fair this week, Interesting Times Gang is showcasing the results of recent experiments with oyster shells. A bioplastic made from crushed shells was 3D printed to create the free-flowing curves of its Gigas Table and Infuana Lamp.The studio is also presenting a collaboration with furniture label Ingridsdotter, a version of the Jonas Bohlin-designed LIV table featuring a surface made from recycled fishing nets that has a finish resembling frothy ocean waves."A regular studio might have a preconceived idea about how something should look," said the studio's head of design, Alexander Westerlund."We work the other way round we start by seeing what can be done with that material, then we try to create something that fits that material's properties."Interesting Times Gang's best-known work is the Kelp Collection. Photo by Matilda Kurtson BellmanInteresting Times Gang is best known for the Kelp Collection, a series of 3D-printed chairs. One version is made from fishing nets mixed with wood fibre, while another is a biocomposite made from seaweed.The project came about after the design studio approached Nordic SeaFarm, Sweden's largest seaweed producer."Kelp regenerates really quickly, so we knew it could be a good material to use if something interesting could be done with it," said Westerlund.Read: Read Dezeen Dispatch online now!The project proved so successful that Nordic SeaFarm, which was previously focused on the food sector, is now exploring the wider potential for kelp in furniture production. IKEA's parent company was among the investors in a recent funding round worth 25 million Swedish kronor."Some of the stuff we're doing has never been done before, so it can be stressful to make it work; sometimes you need to have two or three ideas in your back pocket in case the materials don't perform as you want them to," explained Westerlund.But it's worth the effort, he said, when projects are influencing the likes of IKEA. "It can be hard as a small studio to make change but we're managing to inspire larger companies."Kajsa Willner has developed a technique called craft punk. Photo by David MllerOther designers exploring a fabric-first approach include Malm-based Kajsa Willner, who has developed a technique she calls "craft punk".This stemmed from a 2023 collaboration with Fogia, exploring how the Swedish furniture brand's manufacturing waste could be reintroduced into the production cycle.It led Willner to develop a process for creating objects from small pieces of scrap wood. She coats these creations in paint, followed by a water-based lacquer, resulting in a colourful high-gloss finish.The wooden pieces are covered in water-based lacquer. Photo by David MllerThe designer has been experimenting with the technique ever since, producing vases, chairs, tables and art installations. Her latest creation is a pair of large-scale sculptures for The Office Group in London, made using offcuts from flooring brand Dinesen."Some people think upcycling is basic, when it's the only thing we should be doing," she said.A similar theme of reuse and repair underpins the exhibition Willner is presenting at Stockholm Modern during Stockholm Design Week, a series of polished steel objects featuring torn strips and ripped holes."A few years ago, we couldn't have done that"She believes the global push for sustainability, particularly waste reduction, creates an opportunity to promote more small-scale manufacturing and handcrafted products.The designer hopes that Sweden, which has become synonymous with mass production thanks to IKEA, can become a hotspot for a more material-focused approach to design."I'm interested in pushing the boundaries of how you can work with design," Willner said. "If we want to reduce our waste, maybe the future of furniture is in medium-scale and small-scale production. With these research-based projects, it's all about connecting the dots."Reality was unveiled at last year's Stockholm Design Week.Photo by Martin BrusewitzStockholm-based designer Gustav Winsth has taken a different route to the design process, using digital technologies to uncover new forms of furniture and objects.He and collaborator Alexander Lervik created a stir at last year's Stockholm Furniture Fair when they presented Reality, a chair designed in virtual reality.Read: Six emerging designers to look out for at Stockholm Furniture Fair 2025With the use of VR goggles, the duo worked in digital platform Gravity Sketch to share ideas and sketch out the design shape. The process resulted in a curvaceous aluminium form that could only be brought to life by skilled metalworkers."A few years ago, we couldn't have done that chair," Winsth said. "The software is developing all the time. I could see the potential."The Tension Trolley is now in production. Photo by Erik LefvanderWinsth has already shown that this process can be used on a production scale. He designed the Tension Trolley, a product for furniture brand Lammhults, in the same way.The designer is now exploring how he can apply the approach to interior design, with two projects just open in Stockholm. One is a revamp of restaurant Hosoi, launching during Stockholm Design Week. The other is the newly unveiled showroom of glassmaker Bobo."It means we can go from a really rough sketch to knowing exactly what it feels like to be in the room," Winsth said. "You can walk around and get a good sense of how it will be."The designer believes his background in mechanical engineering gave him a different perspective on product development than other designers. He thinks that experimenting with processes is key to pushing boundaries in a meaningful way.Gustav Winsth unveiled the Bobo show at this year's design week. Photo by Gustav Winsth"Materials and processes interest me more than design itself," he stated."I seldom look at design classics when I'm drawing, but I can be mesmerized by a video of a tube-bending machine. I like seeing different techniques and materials, then trying to find uses for them."Winsth is excited by what might be possible if more designers and manufacturers embrace the arrival of digital technologies like VR."There is so much potential when it comes to prototyping in furniture the idea that you can go into the same room as a product developer in another country, discuss something you both see in front of you and make changes in real-time," he said."I hope that more producers realise that potential."This article was originally written for the Dezeen Dispatch magazine at Stockholm Design Week 2025.Stockholm Design Week 2025 is taking place at various locations around the city from 3 to 9 February. To see what's on, visitDezeen Events Guide.The post Swedish designers doing things that have "never been done before" appeared first on Dezeen.
0 Comments
·0 Shares
·43 Views