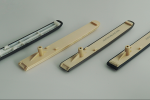
LOT Polish Airlines introduces new single-piece 3D printed arm caps for its Boeing 737 Fleet
3dprintingindustry.com
LOT Polish Airlines has begun installing 3D printed arm caps on its Boeing 737 aircraft.Produced by Riga-based aviation manufacturing firm AM Craft, the new single-piece design replaces conventionally manufactured components with a more durable alternative. This decision comes as part of ongoing efforts to maintain cabin quality while addressing challenges in sourcing replacement parts.As Polands flag carrier, LOT operates over 80 aircraft across Europe, Asia, and North America, but keeping them in great condition has become more difficult due to supply chain disruptions and discontinued components.Adding to the point, Maja Margul, Continuing Airworthiness Junior Specialist at LOT, highlighted that frequent cabin use causes wear, requiring timely part replacements. Some degrade faster than expected, while others become unavailable, leading to procurement delays. To resolve these issues, the Riga-based firm developed a redesigned arm cap manufactured as a single piece to address these issues.LOT Polish Airlines has a long history of leadership in commercial aviation, said Didzis Dejus, CEO of AM Craft. We are proud that we were able to leverage our expertise in design and certification of 3D printed aircraft components to solve their supply chain problem with these arm caps, and we look forward to helping them address additional challenges. For commercial aviation, 3D printing has clearly become a highly impactful technology while no one was looking.Bottom view of arm caps showing (left to right) the part being replaced, the unpainted 3D printed equivalent, and two colors of the final printed part. Image via AM Craft.Enhancing durability and efficiency with 3D printed arm capsAmong the affected components were the economy-class arm caps on LOTs Boeing 737s. The original rubber-and-plastic design often loosened, detached, or cracked at the seat attachment point, complicating maintenance. With replacement parts from the original supplier difficult to obtain, LOT turned to 3D printing for both improved durability and reliable availability.To produce the redesigned arm caps, AM Craft used Stratasys Fused Deposition Modeling (FDM) technology, employing ULTEM 9085 filament, a high-performance thermoplastic known for its strength, flame resistance, and suitability for aerospace applications. The final finish was applied using Mankiewiczs ALEXIT coating system, ensuring a consistent appearance and durability that aligns with LOTs cabin interior requirements.A total of 1,200 arm caps were manufactured by AM Craft for installation across LOT Polish Airlines Boeing 737 fleet. Beyond production, AM Craft also handled the certification process, delivering the components with an EASA Form 1 Airworthiness Certificate, confirming compliance with European aviation safety regulations.By eliminating the multi-part construction, the redesigned arm cap removed the risk of separation between the rubber and plastic layers while also reinforcing the connection point to the seat. The new structure enhances reliability and reduces the likelihood of damage under frequent use.A key advantage of using 3D printing for this component was the ability to manufacture low-to-mid volume parts without the high tooling costs of injection molding or other traditional methods. This flexibility allowed AM Craft to quickly produce the required parts while maintaining high-quality standards.Margul stated that while LOT initially planned to replace only damaged arm caps with identical replacements from the original seat manufacturer, the AM Craft part was such an improvement that we replaced all the arm caps with the 3D printed version.Top view of arm caps showing (left to right) the part being replaced, the unpainted 3D printed equivalent, and two colors of the final printed part. Image via AM Craft.Unique 3D printed aircraft interior partsThis wasnt the first time that the aviation manufacturing firm helped design interior components for an airline. Last year, AM Craft supplied over 300 3D printed blanking panels to Finnair for its Airbus A320 fleet, replacing outdated flip-down video monitors. The upgrade is part of Finnairs effort to modernize Passenger Service Units (PSUs) across 17 aircraft, aiming to reduce weight, minimize inventory, and simplify installation, with each panel taking just 10 minutes to fit.Using 3D printer OEM Stratasys FDM 3D printing and ULTEM 9085 filament, AM Craft tailored the design for easy mounting and finished the parts in its certified paint shop. Installation began in late 2023 and was set to be completed by the end of 2024. Both companies considered the project a success and are open to future 3D printing collaborations.Back in 2021, Senior Aerospace BWT, a UK-based manufacturer of air distribution systems, brought 3D printing in-house to produce aircraft interior components. After two years of testing and qualifying ULTEM 9085, an aerospace-grade thermoplastic, the company installed two Stratasys Fortus 450mc 3D printers at its Cheshire facility.Moving away from external suppliers, the manufacturer began producing parts for low-pressure air ducting and air handling systems used in regional, military, and private jets. Switching from aluminum to FDM 3D printing helped cut weight, cost, and lead times by up to 75%, making it a more efficient option for small, complex components.What3D printing trendsshould you watch out for in 2025?How is thefuture of 3D printingshaping up?To stay up to date with the latest 3D printing news, dont forget to subscribe to the 3D Printing Industry newsletter or follow us on Twitter, or like our page on Facebook.While youre here, why not subscribe to our Youtube channel? Featuring discussion, debriefs, video shorts, and webinar replays.Featured image shows a bottom view of arm caps showing (left to right) the part being replaced, the unpainted 3D printed equivalent, and two colors of the final printed part. Image via AM Craft.Ada ShaikhnagWith a background in journalism, Ada has a keen interest in frontier technology and its application in the wider world. Ada reports on aspects of 3D printing ranging from aerospace and automotive to medical and dental.
0 Commenti
·0 condivisioni
·66 Views