New Court Order in Stratasys v. Bambu Lab Lawsuit
There has been a new update to the ongoing Stratasys v. Bambu Lab patent infringement lawsuit.
Both parties have agreed to consolidate the lead and member casesinto a single case under Case No. 2:25-cv-00465-JRG.
Industrial 3D printing OEM Stratasys filed the request late last month. According to an official court document, Shenzhen-based Bambu Lab did not oppose the motion. Stratasys argued that this non-opposition amounted to the defendants waiving their right to challenge the request under U.S. patent law 35 U.S.C. § 299.
On June 2, the U.S. District Court for the Eastern District of Texas, Marshall Division, ordered Bambu Lab to confirm in writing whether it agreed to the proposed case consolidation. The court took this step out of an “abundance of caution” to ensure both parties consented to the procedure before moving forward.
Bambu Lab submitted its response on June 12, agreeing to the consolidation. The company, along with co-defendants Shenzhen Tuozhu Technology Co., Ltd., Shanghai Lunkuo Technology Co., Ltd., and Tuozhu Technology Limited, waived its rights under 35 U.S.C. § 299. The court will now decide whether to merge the cases.
This followed U.S. District Judge Rodney Gilstrap’s decision last month to deny Bambu Lab’s motion to dismiss the lawsuits.
The Chinese desktop 3D printer manufacturer filed the motion in February 2025, arguing the cases were invalid because its US-based subsidiary, Bambu Lab USA, was not named in the original litigation. However, it agreed that the lawsuit could continue in the Austin division of the Western District of Texas, where a parallel case was filed last year.
Judge Gilstrap denied the motion, ruling that the cases properly target the named defendants. He concluded that Bambu Lab USA isn’t essential to the dispute, and that any misnaming should be addressed in summary judgment, not dismissal.
A Stratasys Fortus 450mcand a Bambu Lab X1C. Image by 3D Printing industry.
Another twist in the Stratasys v. Bambu Lab lawsuit
Stratasys filed the two lawsuits against Bambu Lab in the Eastern District of Texas, Marshall Division, in August 2024. The company claims that Bambu Lab’s X1C, X1E, P1S, P1P, A1, and A1 mini 3D printers violate ten of its patents. These patents cover common 3D printing features, including purge towers, heated build plates, tool head force detection, and networking capabilities.
Stratasys has requested a jury trial. It is seeking a ruling that Bambu Lab infringed its patents, along with financial damages and an injunction to stop Bambu from selling the allegedly infringing 3D printers.
Last October, Stratasys dropped charges against two of the originally named defendants in the dispute. Court documents showed that Beijing Tiertime Technology Co., Ltd. and Beijing Yinhua Laser Rapid Prototyping and Mould Technology Co., Ltd were removed. Both defendants represent the company Tiertime, China’s first 3D printer manufacturer. The District Court accepted the dismissal, with all claims dropped without prejudice.
It’s unclear why Stratasys named Beijing-based Tiertime as a defendant in the first place, given the lack of an obvious connection to Bambu Lab.
Tiertime and Stratasys have a history of legal disputes over patent issues. In 2013, Stratasys sued Afinia, Tiertime’s U.S. distributor and partner, for patent infringement. Afinia responded by suing uCRobotics, the Chinese distributor of MakerBot 3D printers, also alleging patent violations. Stratasys acquired MakerBot in June 2013. The company later merged with Ultimaker in 2022.
In February 2025, Bambu Lab filed a motion to dismiss the original lawsuits. The company argued that Stratasys’ claims, focused on the sale, importation, and distribution of 3D printers in the United States, do not apply to the Shenzhen-based parent company. Bambu Lab contended that the allegations concern its American subsidiary, Bambu Lab USA, which was not named in the complaint filed in the Eastern District of Texas.
Bambu Lab filed a motion to dismiss, claiming the case is invalid under Federal Rule of Civil Procedure 19. It argued that any party considered a “primary participant” in the allegations must be included as a defendant.
The court denied the motion on May 29, 2025. In the ruling, Judge Gilstrap explained that Stratasys’ allegations focus on the actions of the named defendants, not Bambu Lab USA. As a result, the official court document called Bambu Lab’s argument “unavailing.” Additionally, the Judge stated that, since Bambu Lab USA and Bambu Lab are both owned by Shenzhen Tuozhu, “the interest of these two entities align,” meaning the original cases are valid.
In the official court document, Judge Gilstrap emphasized that Stratasys can win or lose the lawsuits based solely on the actions of the current defendants, regardless of Bambu Lab USA’s involvement. He added that any potential risk to Bambu Lab USA’s business is too vague or hypothetical to justify making it a required party.
Finally, the court noted that even if Stratasys named the wrong defendant, this does not justify dismissal under Rule 12. Instead, the judge stated it would be more appropriate for the defendants to raise that argument in a motion for summary judgment.
The Bambu Lab X1C 3D printer. Image via Bambu Lab.
3D printing patent battles
The 3D printing industry has seen its fair share of patent infringement disputes over recent months. In May 2025, 3D printer hotend developer Slice Engineering reached an agreement with Creality over a patent non-infringement lawsuit.
The Chinese 3D printer OEM filed the lawsuit in July 2024 in the U.S. District Court for the Northern District of Florida, Gainesville Division. The company claimed that Slice Engineering had falsely accused it of infringing two hotend patents, U.S. Patent Nos. 10,875,244 and 11,660,810. These cover mechanical and thermal features of Slice’s Mosquito 3D printer hotend. Creality requested a jury trial and sought a ruling confirming it had not infringed either patent.
Court documents show that Slice Engineering filed a countersuit in December 2024. The Gainesville-based company maintained that Creaility “has infringed and continues to infringe” on both patents. In the filing, the company also denied allegations that it had harassed Creality’s partners, distributors, and customers, and claimed that Creality had refused to negotiate a resolution.
The Creality v. Slice Engineering lawsuit has since been dropped following a mutual resolution. Court documents show that both parties have permanently dismissed all claims and counterclaims, agreeing to cover their own legal fees and costs.
In other news, large-format resin 3D printer manufacturer Intrepid Automation sued 3D Systems over alleged patent infringement. The lawsuit, filed in February 2025, accused 3D Systems of using patented technology in its PSLA 270 industrial resin 3D printer. The filing called the PSLA 270 a “blatant knock off” of Intrepid’s DLP multi-projection “Range” 3D printer.
San Diego-based Intrepid Automation called this alleged infringement the “latest chapter of 3DS’s brazen, anticompetitive scheme to drive a smaller competitor with more advanced technology out of the marketplace.” The lawsuit also accused 3D Systems of corporate espionage, claiming one of its employees stole confidential trade secrets that were later used to develop the PSLA 270 printer.
3D Systems denied the allegations and filed a motion to dismiss the case. The company called the lawsuit “a desperate attempt” by Intrepid to distract from its own alleged theft of 3D Systems’ trade secrets.
Who won the 2024 3D Printing Industry Awards?
Subscribe to the 3D Printing Industry newsletter to keep up with the latest 3D printing news.You can also follow us on LinkedIn, and subscribe to the 3D Printing Industry Youtube channel to access more exclusive content.Featured image shows a Stratasys Fortus 450mcand a Bambu Lab X1C. Image by 3D Printing industry.
#new #court #order #stratasys #bambu
New Court Order in Stratasys v. Bambu Lab Lawsuit
There has been a new update to the ongoing Stratasys v. Bambu Lab patent infringement lawsuit.
Both parties have agreed to consolidate the lead and member casesinto a single case under Case No. 2:25-cv-00465-JRG.
Industrial 3D printing OEM Stratasys filed the request late last month. According to an official court document, Shenzhen-based Bambu Lab did not oppose the motion. Stratasys argued that this non-opposition amounted to the defendants waiving their right to challenge the request under U.S. patent law 35 U.S.C. § 299.
On June 2, the U.S. District Court for the Eastern District of Texas, Marshall Division, ordered Bambu Lab to confirm in writing whether it agreed to the proposed case consolidation. The court took this step out of an “abundance of caution” to ensure both parties consented to the procedure before moving forward.
Bambu Lab submitted its response on June 12, agreeing to the consolidation. The company, along with co-defendants Shenzhen Tuozhu Technology Co., Ltd., Shanghai Lunkuo Technology Co., Ltd., and Tuozhu Technology Limited, waived its rights under 35 U.S.C. § 299. The court will now decide whether to merge the cases.
This followed U.S. District Judge Rodney Gilstrap’s decision last month to deny Bambu Lab’s motion to dismiss the lawsuits.
The Chinese desktop 3D printer manufacturer filed the motion in February 2025, arguing the cases were invalid because its US-based subsidiary, Bambu Lab USA, was not named in the original litigation. However, it agreed that the lawsuit could continue in the Austin division of the Western District of Texas, where a parallel case was filed last year.
Judge Gilstrap denied the motion, ruling that the cases properly target the named defendants. He concluded that Bambu Lab USA isn’t essential to the dispute, and that any misnaming should be addressed in summary judgment, not dismissal.
A Stratasys Fortus 450mcand a Bambu Lab X1C. Image by 3D Printing industry.
Another twist in the Stratasys v. Bambu Lab lawsuit
Stratasys filed the two lawsuits against Bambu Lab in the Eastern District of Texas, Marshall Division, in August 2024. The company claims that Bambu Lab’s X1C, X1E, P1S, P1P, A1, and A1 mini 3D printers violate ten of its patents. These patents cover common 3D printing features, including purge towers, heated build plates, tool head force detection, and networking capabilities.
Stratasys has requested a jury trial. It is seeking a ruling that Bambu Lab infringed its patents, along with financial damages and an injunction to stop Bambu from selling the allegedly infringing 3D printers.
Last October, Stratasys dropped charges against two of the originally named defendants in the dispute. Court documents showed that Beijing Tiertime Technology Co., Ltd. and Beijing Yinhua Laser Rapid Prototyping and Mould Technology Co., Ltd were removed. Both defendants represent the company Tiertime, China’s first 3D printer manufacturer. The District Court accepted the dismissal, with all claims dropped without prejudice.
It’s unclear why Stratasys named Beijing-based Tiertime as a defendant in the first place, given the lack of an obvious connection to Bambu Lab.
Tiertime and Stratasys have a history of legal disputes over patent issues. In 2013, Stratasys sued Afinia, Tiertime’s U.S. distributor and partner, for patent infringement. Afinia responded by suing uCRobotics, the Chinese distributor of MakerBot 3D printers, also alleging patent violations. Stratasys acquired MakerBot in June 2013. The company later merged with Ultimaker in 2022.
In February 2025, Bambu Lab filed a motion to dismiss the original lawsuits. The company argued that Stratasys’ claims, focused on the sale, importation, and distribution of 3D printers in the United States, do not apply to the Shenzhen-based parent company. Bambu Lab contended that the allegations concern its American subsidiary, Bambu Lab USA, which was not named in the complaint filed in the Eastern District of Texas.
Bambu Lab filed a motion to dismiss, claiming the case is invalid under Federal Rule of Civil Procedure 19. It argued that any party considered a “primary participant” in the allegations must be included as a defendant.
The court denied the motion on May 29, 2025. In the ruling, Judge Gilstrap explained that Stratasys’ allegations focus on the actions of the named defendants, not Bambu Lab USA. As a result, the official court document called Bambu Lab’s argument “unavailing.” Additionally, the Judge stated that, since Bambu Lab USA and Bambu Lab are both owned by Shenzhen Tuozhu, “the interest of these two entities align,” meaning the original cases are valid.
In the official court document, Judge Gilstrap emphasized that Stratasys can win or lose the lawsuits based solely on the actions of the current defendants, regardless of Bambu Lab USA’s involvement. He added that any potential risk to Bambu Lab USA’s business is too vague or hypothetical to justify making it a required party.
Finally, the court noted that even if Stratasys named the wrong defendant, this does not justify dismissal under Rule 12. Instead, the judge stated it would be more appropriate for the defendants to raise that argument in a motion for summary judgment.
The Bambu Lab X1C 3D printer. Image via Bambu Lab.
3D printing patent battles
The 3D printing industry has seen its fair share of patent infringement disputes over recent months. In May 2025, 3D printer hotend developer Slice Engineering reached an agreement with Creality over a patent non-infringement lawsuit.
The Chinese 3D printer OEM filed the lawsuit in July 2024 in the U.S. District Court for the Northern District of Florida, Gainesville Division. The company claimed that Slice Engineering had falsely accused it of infringing two hotend patents, U.S. Patent Nos. 10,875,244 and 11,660,810. These cover mechanical and thermal features of Slice’s Mosquito 3D printer hotend. Creality requested a jury trial and sought a ruling confirming it had not infringed either patent.
Court documents show that Slice Engineering filed a countersuit in December 2024. The Gainesville-based company maintained that Creaility “has infringed and continues to infringe” on both patents. In the filing, the company also denied allegations that it had harassed Creality’s partners, distributors, and customers, and claimed that Creality had refused to negotiate a resolution.
The Creality v. Slice Engineering lawsuit has since been dropped following a mutual resolution. Court documents show that both parties have permanently dismissed all claims and counterclaims, agreeing to cover their own legal fees and costs.
In other news, large-format resin 3D printer manufacturer Intrepid Automation sued 3D Systems over alleged patent infringement. The lawsuit, filed in February 2025, accused 3D Systems of using patented technology in its PSLA 270 industrial resin 3D printer. The filing called the PSLA 270 a “blatant knock off” of Intrepid’s DLP multi-projection “Range” 3D printer.
San Diego-based Intrepid Automation called this alleged infringement the “latest chapter of 3DS’s brazen, anticompetitive scheme to drive a smaller competitor with more advanced technology out of the marketplace.” The lawsuit also accused 3D Systems of corporate espionage, claiming one of its employees stole confidential trade secrets that were later used to develop the PSLA 270 printer.
3D Systems denied the allegations and filed a motion to dismiss the case. The company called the lawsuit “a desperate attempt” by Intrepid to distract from its own alleged theft of 3D Systems’ trade secrets.
Who won the 2024 3D Printing Industry Awards?
Subscribe to the 3D Printing Industry newsletter to keep up with the latest 3D printing news.You can also follow us on LinkedIn, and subscribe to the 3D Printing Industry Youtube channel to access more exclusive content.Featured image shows a Stratasys Fortus 450mcand a Bambu Lab X1C. Image by 3D Printing industry.
#new #court #order #stratasys #bambu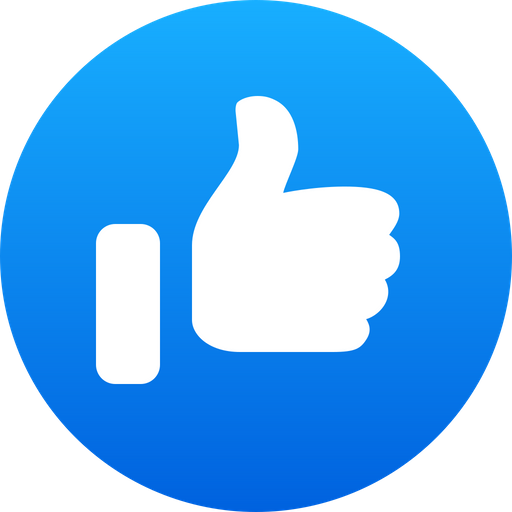
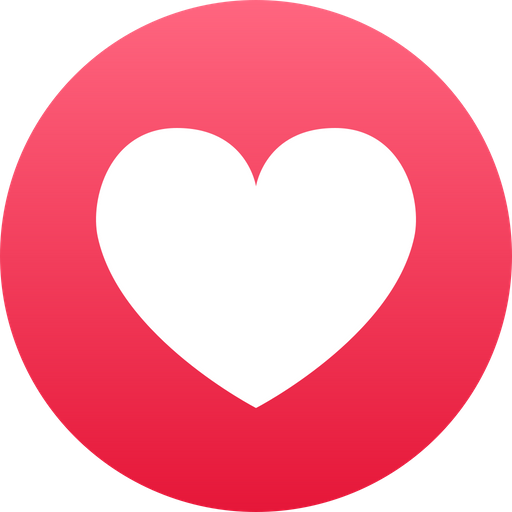
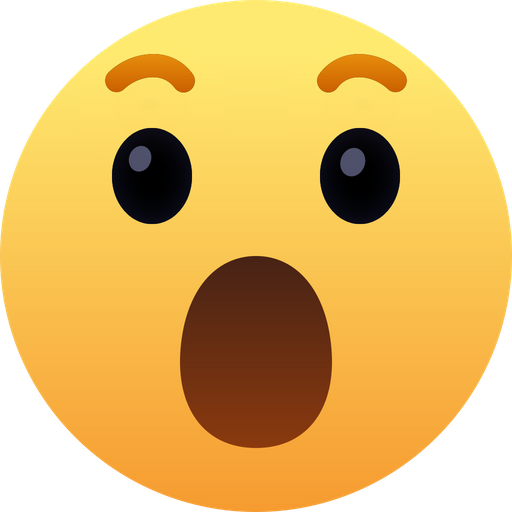
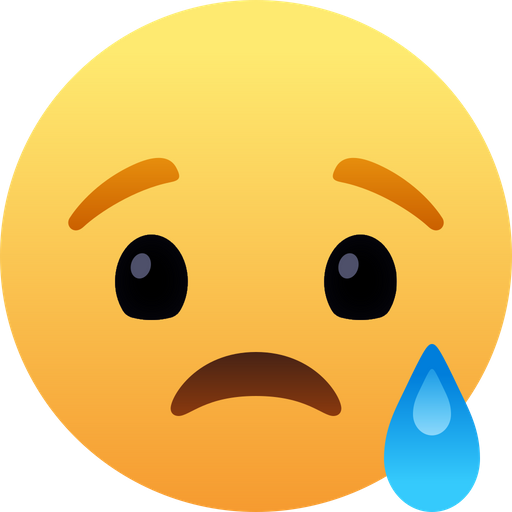
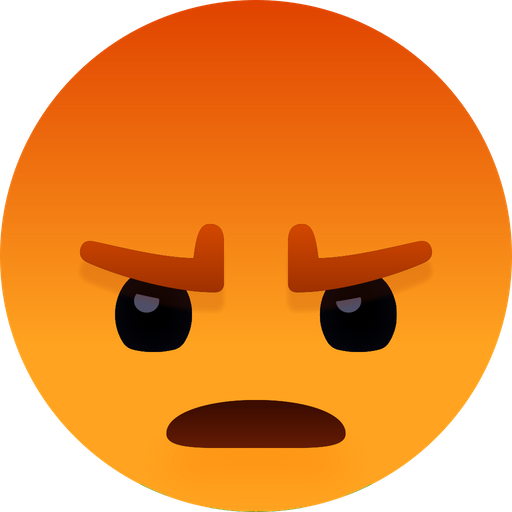
2 Comentários
·0 Anterior