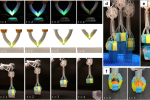
Can FDM under extrusion yield better results in bio-inspired robotics? Research suggests so
3dprintingindustry.com
Researchers from the University of Twente (UT) and University of Southern Denmark (SDU) have come up with a clever way to strengthen the connection between soft and rigid materials in hybrid robots, an ongoing challenge in robotics.Interestingly, their approach turns an everyday 3D printing issue, under extrusion, into an advantage. By deliberately allowing the printer to create a porous structure, theyve found a way to improve adhesion between materials.Whats more, this method works with standard fused deposition modeling (FDM) printers, making it far more accessible than existing solutions that require expensive multi-material printers. Published in Nature, contributions came from researchers Arman Goshtasbi from SDU, Luca Grignaffini and Ali Sadeghi from UT.A bioinspired hybrid gripper mimicking a human fingernail features a rigid nail plate bonded to a porous mesh, replicating the natural bond between a nail and nail bed. Image via UT.Mimicking nature to enhance roboticsSoft and rigid components in robots each have their strengths, but getting them to bond properly has always been a tricky business. Differences in how these materials handle stress often lead to weak adhesion, with traditional bonding methods, such as adhesives, becoming failure points under mechanical strain.Nature, however, offers a solution. Just as biological connective tissues seamlessly link muscles to bones, the researchers developed a fibrous, porous structure that strengthens the connection between soft and rigid materials.This approach mirrors how tendons, ligaments, and other natural interfaces distribute stress, preventing sudden mechanical failures. Through rigorous testing, they fine-tuned the level of porosity needed to achieve an optimal balance of strength and flexibility, marking a step forward in bio-inspired robotics.The numbers tell the story. In lap shear and peel tests, this method outperformed traditional adhesives by up to 200%. Experiments with Ecoflex 00-10 and DragonSkin 10 silicone rubbers showed significantly stronger bonds compared to commonly used adhesives, giving soft robots a better shot at durability.For pneumatic soft robotics, where airtight seals are critical, the method also showed promising results. Under simulated pressure conditions, bonds created using this technique withstood forces three times greater than those joined with adhesives, reinforcing its potential for inflatable and hybrid robotic systems.By offering a simple, low-cost way to create strong bonds between different materials, this method could change how hybrid robots are made. Applications could extend to any environment where mechanical reliability is crucial, opening up new possibilities for soft robotics.According to the researchers, future work may explore ways to further refine this technique by mimicking natures gradual transitions between soft and rigid materials. Testing with alternative 3D printing materials, like ABS and PETG, could also shed light on ways to make bonds even stronger.Lap shear and peel-off test results. Image via UT.Research into bio-inspired roboticsIn the past, 3D printing has contributed to the development of several unique bio-inspired robots. One notable contribution came from researchers at the University of California San Diego, who introduced a more affordable way to 3D print soft, insect-like robots. Their flexoskeleton printing method works with standard FDM printers, layering rigid filaments onto a heated thermoplastic base.This approach simplifies production, making soft robotics more accessible by removing the need for expensive multi-material 3D printing. Drawing inspiration from insect exoskeletons, the technique balances flexibility and structural support. In tests, the printed robots demonstrated improved strength and durability, with a prototype successfully walking on its own.Elsewhere in 2022, a student from University of Surrey developed a 3D printed robotic fish designed to collect microplastics from waterways. Created by Eleanor Mackintosh in 2022, the robot, called Gillbert, featured gill-like structures with fine mesh to trap plastic particles as small as two millimeters while allowing water to pass through.The design won the 2022 Natural Robotics Contest and was successfully tested in both lab settings and a UK lake. At the time, it was remote-controlled, with future plans including to improve its swimming speed and autonomy.What3D printing trendsshould you watch out for in 2025?How is thefuture of 3D printingshaping up?To stay up to date with the latest 3D printing news, dont forget to subscribe to the 3D Printing Industry newsletter or follow us on Twitter, or like our page on Facebook.While youre here, why not subscribe to our Youtube channel? Featuring discussion, debriefs, video shorts, and webinar replays.Featured image shows a bioinspired hybrid gripper mimicking a human fingernail features a rigid nail plate bonded to a porous mesh, replicating the natural bond between a nail and nail bed. Image via UT.
0 Comentários
·0 Compartilhamentos
·59 Visualizações