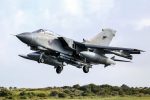
RAF Jets Recycled into 3D Printable Material in New Project
3dprintingindustry.com
British engine manufacturer Rolls-Royce has partnered with the UK Ministry of Defence (MOD) to recycle fighter jet components into 3D printed engine parts.The collaboration, which features expertise from Additive Manufacturing Solutions Ltd., is converting old Royal Air Force (RAF) Tornado fighter jet parts into metal powder feedstock. This has been used to 3D print components for the Orpheus jet engine concept, which supports the Future Combat Air System (FCAS) program.Part of Rolls-Royces defense division, Orpheus seeks to accelerate engine design and production using advanced manufacturing techniques, such as 3D printing. According to Neil Mantle, the companys Director of Manufacturing, additive manufacturing previously reduced development times by 50%, with engines going from concept to testing in 18 months.Rolls-Royce believes its latest 3D printing initiative, called Tornado 2 Tempest, has the potential to support the Tempest fighter jet. Developed through Britain, Italy, and Japans Global Combat Air Programme (GCAP), the sixth-generation aircraft has already leveraged additive manufacturing. Last year, BAE Systems, the British aerospace firm leading the project, used metal 3D printing to produce primary structural components for the Tempests demonstrator. This follows BAEs 2020 statement that it planned to 3D print 30% of the Tempests parts.The Tornado 2 Tempest project exemplifies the forward-thinking sustainability principles embedded in the FCAS Sustainability Strategy and MOD Defence Support Strategy, commented Andrew Eady, Rolls-Royces VP of FCAS Sustainability.At Rolls-Royce, we continue to be leaders in circular economy practices and innovative digital enablers to support our steps to be a lower carbon and digitally enabled business, Eady added. He called Tornado 2 Tempest a bold, exciting and innovative project and a demonstration of how excellent collaboration between the MOD, industry and SME can deliver sustainable and technologically advanced solutions.RAF Tornado Fighter Jet. Photo via the RAF.3D printing recycled fighter jet partsThe Tornado fighter jet retired from RAF operations in 2019. When decommissioning, replacing, and scrapping old equipment, the MOD risks losing strategic metals. Many of its surplus assets and broken components feature valuable materials like high-quality steel, aluminum, and titanium.The Tornado 2 Tempest project aimed to explore whether surplus Tornado components could be converted into metal powder for 3D printing, creating a circular supply chain. As part of this effort, titanium Tornado partssuch as jet engine compressor blades from a low-pressure air compressorwere collected, cleaned, and atomized into metal feedstock.Rolls-Royce and AMS then used this powder to 3D print a nose cone and compressor blades, which were installed on the Orpheus test engine. After installation, the engine was tested under operational conditions to validate the safety, performance, and feasibility of 3D printed components for future military aircraft engines. The team also developed a Digital Product Passport to track material provenance and lifecycle data. According to Rolls-Royce, this could help make more informed material allocation decisions and safeguard against counterfeit materials.AMS stated it is honored to contribute its expertise in additive manufacturing to this collaborative effort, reinforcing its commitment to advancing sustainable and efficient solutions within the aerospace and defense sectors. Rob Higham, the companys Founder, added, This project turned our proposed solutions into a reality, and we have been very humbled and grateful to the MOD and Rolls-Royce, for allowing us to showcase our capability to deliver game-changing circular economy processes and parts in Defence.Rolls-Royce, AMS, and the MOD led the initiative alongside Defence Equipment and Supports (DE&S) Defence Recycling & Disposals Team (DRDT). The project was funded by the UK Strategic Commands Defence Support Organisation in support of its Circular Economics for Defence Concept Note. Over 80 people participated, including DRDTs commercial graduates and Rolls-Royce graduate apprentices.Rolls-Royces Orpheus engine. Photo via Rolls-Royce.Additive manufacturing to secure defense supply chainsShipping insecurities and geopolitical challenges are increasingly threatening global supply chains. This has led many countries, including the UK, to ramp up their sovereign military manufacturing capabilities with 3D printing. Earlier this year, armored vehicle manufacturer Rheinmetall BAE Systems Land (RBSL) announced it had attracted over 56 million in investment to accelerate defense manufacturing at its Hadley Castle Works Factory in Telford. The company, a joint venture between the UKs BAE Systems and Dsseldorf-based Rheinmetall, is leveraging additive manufacturing to produce the next-generation Challenger 3 main battle tank and Boxer armored personnel carrier on British soil.Maria Eagle, Minister for Defence Procurement, recently visited the Telford site as part of the UK Governments new Defense Industrial Strategy. This initiative seeks to ensure the countrys defense sector is innovative, resilient, and competitive. During the visit, Eagle stated that Telford is at the heart of UK defence, with the new Government strategy designed to drive economic growth, boost British jobs, and strengthen national security.A 950 million Challenger 3 contract has already created 300 jobs across RBSLs facilities in Telford, Dorset, Bristol, and Newcastle. This was followed by a 5 billion investment to equip UK forces with 148 Challenger 3 tanks and 623 Boxer vehicles by 2030.Elsewhere, the UK, Australian, and US governments agreed to accelerate hypersonic technology under a new AUKUS Hypersonic Flight Test and Experimentation (HyFliTE) Project. Initially signed in 2021, the trilateral partnership is pursuing a new level of collaboration to unlock faster development, testing, and evaluation of hypersonic vehicles to bolster their sovereign aerospace and defense capabilities. This could include long-range strike missiles launched from land, sea, or air.According to the MOD, the new project seeks to bolster battle-winning capabilities, enhance domestic security, and defend against international threats. Existing research will be incorporated into the new initiative, reportedly allowing the partners to develop at a pace that no one nation could do alone. While the role of additive manufacturing has not been disclosed, the US is investing heavily in 3D printed missiles. For instance, the Department of Defense awarded rocket engine manufacturer Ursa Major with $12.5 million to develop 3D printed solid rocket motors in the US. It has also previously funded aerospace firm Aerojet Rocketdynes efforts to 3D print a prototype hypersonic propulsion system.Who won the 2024 3D Printing Industry Awards?Subscribe to the 3D Printing Industry newsletter to keep up with the latest 3D printing news.You can also follow us on LinkedIn, and subscribe to the 3D Printing Industry Youtube channel to access more exclusive content.Featured image shows an RAF Tornado Fighter Jet. Photo via the RAF.
0 Comments
·0 Shares
·58 Views