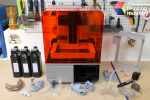
REVIEW: High-speed Resin 3D Printing with the Formlabs Form 4
3dprintingindustry.com
In this article, the 3D Printing Industry engineering team reviews Formlabs Form 4 resin 3D printer.This is the fourth generation of the Massachussetts-based companys Form series, accelerating resin-based additive manufacturing with Blazing Fast 100 mm per hour 3D printing. High speeds are enabled by the companys Low Force Display (LFD) engine, a masked stereolithography (MSLA) approach that combines LCD and SLA technologies.The 3D printers sizeable build volume and compatibility with any 405 nm photopolymer resin support a wide range of applications for professional-grade 3D printing. Read on to discover why the Form 4 is an impressive option for prosumer and industrial users seeking high-speed, high-quality, versatile, and affordable 3D printing. Prices for the Form 4 start at just $4,499, with more information available on the Formlabs website.Formlabs Form 4 3D printer. Photos by 3D Printing Industry.Why choose Formlabs Form 4?Central to the Form 4 is its novel LFD 3D print engine, representing a significant shift from the laser and galvanometer technology found in most competing products. This approach minimizes the force applied during 3D printing to enhance part quality and dimensional accuracy.The engine utilizes an innovative backlit LED unit to project the models cross-sectional area onto the resin tank, curing the resin. It leverages 60 LEDs and collimating lenses to produce a uniform area projection of ultra-high power light at an intensity of 16mw/cm2.According to Formlabs, this technology enables quick and precise 3D printing, ensuring a level of accuracy that rivals injection molded parts. Indeed, the Form 4 is ideal for customers wanting to accelerate 3D printing operations. Average 3D print speeds of 40 mm/hour can be achieved with a 100 m layer height, while maximum speeds reach 100 mm/hour.The 3D printer also boasts a 50 m pixel size with pre-tuned anti-aliasing and a maximum lifetime of 1.9 million layers. Its 0.15% XY dimensional tolerances seek to ensure that part assemblies fit and function as expected.Reliability is another key selling point of the Form 4. This is underpinned by validated 3D printer settings, precise heating mechanisms, force-sensing, and debris-detection capabilities. As such, Formlabs claims its fourth-generation product offers an unmatched 3D print success rate exceeding 98.7%, ideal for professionals targeting high-volume production.The Formlabs Form 4. Photos by 3D Printing Industry. User-friendly hardware with a premium feel Fitting a sizeable 200 mm x 125 mm x 210 mm build volume into a desktop-sized unit, the Form 4 offers the premium, high-quality feel we expect from Formlabs. Its sturdy metal chassis, distinct orange-tinted anti-UV door, and user-friendly touch-screen user interface (UI) create a premium, minimalist profile that would fit well into most workspaces.Form 4 unboxing and assembly is a breeze. No tools are required, and we had our 3D printer up and running in just 15 minutes. 60-point calibration and quality control inspection are conducted before each 3D printer leaves the factory, guaranteeing high-quality 3D printing straight out of the box.Formlabs Form 4 unboxing and kit contents. Photos by 3D Printing Industry.Formlabs fourth-generation 3D printer features a new, specialized resin tank. This incorporates a large dual-film system that works in conjunction with the LFD technology to ensure consistent, high-quality 3D printing and easy layer peeling. Formlabs Form 4 resin tanks can process over 75,000 layers, translating to 1 to 2 years for most users.The 200 mm x 125 mm print bed is also optimized for ease of use. It can be removed with one hand, while its solid, non-perforated design simplifies cleaning. However, parts often adhere strongly to the surface, risking damage. A built-in camera captures the entire build plate, allowing users to conduct remote build monitoring and capture 3D printing time-lapses.Form 4 resin tank and build plate. Photos by 3D Printing Industry.Formlabs end-to-end 3D printing ecosystemOur engineering team also tested Formlabs Form Wash (2nd Generation) and Form Cure post-processing units, which combine with the Form 4 to create an end-to-end 3D printing ecosystem.Once a 3D printing job is completed, the part must be washed to remove any toxic uncured resin. Liquid solvents, like Isopropyl alcohol, are usually used to achieve this. We were impressed by the Form Wash, which significantly reduces the need for direct contact with washing solvents. This provides a safer and cleaner alternative to manual wash stations, where users risk inhaling harmful IPA fumes and spilling solvents.After cleaning, 3D printed parts should be cured in UV light to further harden the resin. This helps to stabilize material properties, enhance surface quality, and improve part tolerances and accuracy. The Form Washs 405 nm light, 100 W heater, turntable, and reflective interior enable thorough polymerization at temperatures up to 80. Additionally, its plug-and-play functionality and user-friendly interface ensure a seamless curing process for users of all experience levels.Formlabs Form Wash (2nd Generation) and Form Cure post-processing units. Photos by 3D Printing Industry.PreForm 3D printing softwareFormlabs Form 4 is controlled by the companys proprietary, free-to-use PreForm 3D printing software. Compatible across all Formlabs 3D printers, PreForm stands out thanks to its intuitive interface and control over essential 3D printing tasks.The software allows users to easily slice models, generate supports, manipulate parts, and modify designs. It can also be used to simultaneously manage multiple Formlabs 3D printers, ideal for 3D print farms and high-volume production environments.PreForms One-Click Print feature is particularly valuable. This automates several key processes to reliably ensure successful 3D printing. These include model repair, orientation, automatic support generation, and build area layout adjustments to prevent overlap. The file can then be uploaded directly to the Form 4, making for an incredibly straightforward and hassle-free process.For industrial users handling high production volumes, manually adjusting each part on the print bed can lead to significant delays. To address these challenges, PreForms layout function automatically arranges all models to maximize build area usage. Once a model has been loaded and oriented, the software can automatically generate and analyze support structures to enhance final part quality.While we were impressed by PreForms straightforward usability and functionality, its simplicity could be limiting for more experienced users. Features like nesting, non-uniform scaling, in-slicer model editing, and custom cutting tools are all missing, preventing more advanced 3D printing possibilities.PreForm layout, One-Click Print feature, and support generation. Images by 3D Printing Industry.Intuitive UI streamlines 3D printingThe Form 4s seven-inch touchscreen UI also stood out to our testing team. This intuitive, easy-to-navigate interface provides preventative maintenance reminders, information on 3D print status, and printer readiness, removing questions from the production process.The Form 4 makes maintenance effortless by displaying critical diagnostic tools on-screen. If an issue arises, a QR code directs users to relevant support articles for quick troubleshooting, an invaluable tool for resin 3D printing newcomers. Looking ahead, Formlabs plans to enhance accessibility further with firmware updates, including new language options.Calibration steps on the Form 4s 7-inch, touchscreen user interface. Photos by 3D Printing Industry.Benchmarking the Form 4How does the Form 4 compare to other resin 3D printers on the market? To find out, we conducted several benchmarking prints, which will also test the claims made by Formlabs.The first, a mandibular dental model commonly 3D printed during dental training, was initiated using PreForms One-click Print function. This was impressive, featuring exceptional surface quality with no visible layer lines. The auto-support generation system worked perfectly, requiring minimal manual tweaking of the 3D model before printing. Post-processing was also straightforward. All residue was cleaned off in under ten minutes, with effective curing completed in half an hour.3D printed mandibular dental model. Photos by 3D Printing Industry. The Form 4 stands out with its notable build volume of 200 mm x 125 mm x 210 mm. However, some slicers restrict users from fully utilizing the printers advertised capacity. Does this impact the Form 4? For the Z-axis, our tower test found no restrictions and our part achieved a height of 210 mm.Form 4 3D printed tower test. Photos by 3D Printing Industry.During this test, we were particularly impressed by PreForms Print Validation feature, which helps users identify potential issues before the printing process begins. For example, during the tower test, the validation system detected risks associated with printing tall parts and recommended adding vent holes to reduce the cupping effect. This feature is invaluable for users who prioritize reliability and want to avoid the frustration of failed prints.Print validation warnings. Image by 3D Printing Industry.Next, we conducted a perimeter test to assess the maximum 200 mm x 125 mm limits along the X and Y axes. When importing the STL file into PreForm, we encountered a warning stating that the model exceeded the build volume, despite it measuring the exact advertised dimensions.This occurred because the software compensates for material shrinkage during printing. To handle shrinkage, the printer applies a standard scale correction for each material. In this case, the correction was 1.0049 mm. Fortunately, this shrinkage only caused a minor reduction of less than one millimeter in the overall size, which would have a negligible impact on most applications.3D printed perimeter test. Photos by 3D Printing Industry. Parts with complex geometries often feature overhanging sections. This can pose challenges for resin 3D printers. To assess how the Form 4 deals with these challenges, we 3D printed two models with six overhangs increasing in 5 from 40 to 65.Both parts were successful, with all angles completed to a good standard. However, we did observe a faint rippling defect. This was likely caused by the peeling force during the early stages of 3D printing. Interestingly, the rippling effect disappeared approximately one-quarter of the way into the print, leaving a completely smooth overhang at angles up to 65. This minor anomaly did not impact the integrity of the print, with the test confirming the Form 4s ability to handle overhang geometries.3D printer overhang tests. Photos by 3D Printing Industry. Many users turn to resin 3D printers due to their advantages in producing parts with small dimensions and tight tolerances. To assess the Form 4s capabilities for these applications, we 3D printed a functional M8 nut and bolt with a coarse pitch size of 1.25 mm.These small parts were successfully produced with impressive detail in 1 hour. They were 3D printed on a raft to prevent an elephant foot effect, a common defect where the initial layers are flattened or widened. Once removed and post-processed, the nut and bolt fit together seamlessly, confirming the Form 4 can 3D print small and precise parts to desired tolerances.3D printed M8 X 1.25 mm nut and bolt. Photos by 3D Printing Industry. However, our next attempt to produce a nut and bolt with a 1 mm thread pitch was unsuccessful. As the threads became finer, the Form 4 failed to maintain the required resolution. As such, we can confirm that the 3D printer has limitations when fabricating ultra-fine-pitch threads, limiting its value for certain high-resolution applications.3D printed M6 X 1 mm nut and bolt print. Photos by 3D Printing Industry.To test the Form 4s ability to handle fine details, we 3D printed a small J3D Tech Definition test cube. This coin-sized model includes three surfaces with complex shapes and intricate details.The test showed that the printer can produce high-quality, ultra-detailed parts. While there were minor issues with extremely thin walls, the overall results were impressive. Therefore, the Form 4 is well-suited for making small, detailed parts with complex designs.3D printed J3D Tech Definition test cube. Photos by 3D Printing Industry.Repeatability is essential when producing batches of identical parts. To determine the Form 4s value for this application, we 3D printed a test model 12 times, each of which was measured and compared to the intended dimensions. Most proficient 3D printers will achieve an average deviation of less than 0.05 mm and a standard deviation under 0.25 mm.3D printed repeatability parts. Photos by 3D Printing Industry.All twelve test pieces were 3D printed and processed with no significant defects. The measurements ultimately highlighted the strong repeatability of the Form 4. The average deviation came to 0.0477 mm, just below the 0.05mm benchmark. While this highlighted commendable precision, these parts were negatively impacted by Z-axis deviations caused by uncured, trapped resin or support touchpoints being cured inside the hole section. The X and Y axes exhibited identical results, reflecting great consistency across all models.The standard deviation was a remarkable 0.0155 mm compared to the 0.25 mm target. This confirms Formlabs claims regarding the Form 4s reliability and precision, helping it stand out as a consistently high-quality professional-grade resin 3D printer.Repeatability differences between the measurement and reference. Image by 3D Printing Industry.Testing Form 4 3D printing applicationsEngineers and manufacturers often leverage resin 3D printers to fabricate functional, end-use parts. Formlabs offers a range of resins optimized for these parts, featuring mechanical properties for a range of applications.The companys Grey V5 resin is well known for its versatility and robust mechanical properties. To assess the ability of the Form 4 to produce functional parts with this material, we fabricated motorcycle fuel pump hose clips. This component attaches to the fuel hose to the pump, preventing any accidental dislodgement. The original equipment manufacturer of this particular component no longer produces these clips, meaning resin 3D printing offers an excellent alternative to producing aftermarket parts.We 3D printed a batch of 24 fuel pump clips, with a total print time of 7 hours. The Form 4 performed exceptionally well here, with all components produced with intricate features perfectly preserved. The surface text was rendered perfectly, rivaling the quality of its injection-molded counterparts.3D printed fuel pump clips. Photos by 3D Printing Industry. Another popular application of desktop resin 3D printers is the production of figurines and miniature models with fine details. To assess whether the Form 4 is a good choice for enthusiasts and designers targeting the arts and crafts market, we produced a Viking figurine with a 25 m layer thickness.The 3D printer again performed exceptionally well here, delivering an impressive surface finish with consistent layer buildup and no anomalies. Post-processing was straightforward, with the model washed, dried, and cured with minimal manual input. Some issues were encountered with support removal. Even after reducing the touchpoints to a size of 0.35 mm, we were unable to achieve clean breaks, with many supports generated in delicate areas of the model. Despite this, we were thoroughly impressed with the Form 4s performance.3D printed Viking model. Photos by 3D Printing Industry. Next, we used the translucent Clear V5 material to 3D print a breathing mouthpiece that connects two snorkeling components. We sought to produce an end-use part that was strong, damage-resistant, and highly precise. Clear V5 achieved this with flying colors.The part had an impressive transparent effect, free from the cloudiness often seen in other translucent resins. It also showed no yellowing, which is a common issue with similar clear materials. The high clarity and smooth surface finish eliminated the need for extra post-processing, like polishing or smoothing, and support removal left minimal marks.3D printed breathing tube mouthpiece. Photos by 3D Printing Industry. The use of additive manufacturing is growing within the medical sector, as on-site 3D printers significantly reduce lead times and support patient-specific customization. To assess the Form 4s value for the production of medical devices, we 3D printed a primary oxygen splitter assembly. Clear V5 resin was again used to enable easy inspection of the splitters internal channels. Additionally, the material is not reactive to oxygen, a critical factor for this oxygen-heavy part.Despite 3D printing all parts, the Form 4 encountered a critical issue that rendered the final product unusable. The 3D printer could not achieve the required precision for the threaded connections. Attempts to join these sections resulted in the threads grinding against each other, preventing proper assembly. To correct this, the parts would need to be re-designed with a coarser thread pitch.3D printed oxygen splitter assembly. Photos by 3D Printing Industry.Resin 3D printers are also witnessing increased adoption within the eyewear sector, offering benefits for sustainability, personalization, and localized production. Is the Form 4 well suited to serve this growing market? We were pleased with the quality of our 3D printed sunglasses frames, which were produced with the finest layer height of 25m.However, support removal again caused issues, leaving small dents and marks on the frame. Moreover, after a few uses the threaded connector sections failed, largely due to the brittle nature of Formlabs Clear V5 resin. Therefore, a more flexible 3D printable resin would likely achieve better results for the functional frame.3D printed sunglasses frame. Photos by 3D Printing Industry.Elastic 50a, a silicone-like material, offers much better flexibility and durability. To assess the Form 4s ability to 3D print more stretchable components we 3D printed a soft robotic gripper prototype. Pumping air or water into its channels causes the gripper to contract, allowing it to grip small objects.The quality of this prototype was excellent, with perfect channels and good functionality. Post-processing was greatly successful, although the surface remained slightly sticky after washing and curing. Users should note that Elastic 50A is fragile and prone to tearing when removed from the build platform, an issue we experienced twice during our testing. To avoid this, we recommend using Formlabs new Flex Platform, an upgraded version designed to facilitate easier part removal.3D printed robotic gripper. Photos by 3D printing Industry.The Form 4: high-speed, professional-grade 3D printingThe Formlabs Form 4 is a reliable, high-performance resin 3D printer that combines impressive accuracy and versatility with affordability and ease of use. The efficiency and reliability provided by Formlabs LFD technology make the Form 4 ideal for professional and industrial-scale users seeking an adept production system at a low price point.Notably, the Blazing Fast 100 mm/hour maximum and 40 mm/hour average production speeds significantly accelerate the resin 3D printing process. This, in turn, reduces lead times, expands output, and saves money, increasing productivity by 3x for certain applications. Its accelerated production capabilities make the Form 4 well suited to engineers targeting quick prototyping, high-volume manufacturers, and print farms facing high demand.LFDs minimal peeling forces ensured a high success rate throughout our testing, which indicated impressive accuracy and precision for a range of sizes and geometries. We were particularly impressed with 3D printers repeatability, which stood out with an exceptional 0.0155 mm standard deviation.Formlabs Form Wash and Form Cure units also stood out as great options in the post-processing market. Their hands-free operation enhances the user experience, minimizing exposure to IPA solvent and other harmful chemicals. In our testing, we rarely encountered un-cured resin, with the Form Cure featuring tunable settings optimized for Formlabs materials.PreForm software further elevated our testing experience. Its easy-to-use interface allows users of all experience levels to reliably achieve impressive results. In particular, One-click printing significantly streamlines the production process, ensuring settings are optimized for high-quality 3D printing.Some limitations were recognized during our extensive testing. The Form 4 faces challenges with extremely fine threads, preventing functionality for screwable sections. The finer the pitch, the more likely the parts are to be affected by shrinkage, which could pose issues for certain applications. Issues were also encountered when removing support structures, which frequently damaged otherwise perfectly finished surfaces.Despite this, we were impressed with the Form 4s ability to achieve high-quality, professional-grade 3D printing at high speeds. Its affordable price makes it an incredibly competitive addition to the industrial resin 3D printer market, offering value for users requiring reliable, high-quality results in a straightforward package.Technical specification of Formlabs Form 43D Printing TechnologyLow Force Display (LFD)Build Volume200 mm x 125 mm x 210 mmLayer Thickness (Z Resolution)25 300 micronsXY Resolution50 micronsAverage 3D Printing Speed40 mm/hourMaximum 3D Printing Speed100 mm/hResin Tank Lifetime75,000+ layers with any Formlabs material3D Printer Dimensions398 x 367 x 554 mm3D Printer Weight18.3kgSoftware CompatibilityWindows 7 and up; Mac OS X 10.12 and upFile Types AcceptedSTL, OBJ, 3MFSubscribe to the 3D Printing Industry newsletter to keep up with the latest 3D printing news.You can also follow us on LinkedIn like our Facebook page, and subscribe to the 3D Printing Industry Youtube channel to access more exclusive content.Featured image shows the Formlabs Form 4 3D printer. Photo by 3D Printing Industry.
0 التعليقات
·0 المشاركات
·53 مشاهدة