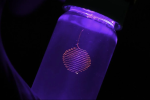
A new 3D printing method to produce ultra-fine fibers at scale
3dprintingindustry.com
Researchers from University of Illinois Urbana-Champaign have developed a novel method to fabricate ultra-fine fibers with diameters as small as 1.5 m, offering a scalable way to replicate biological fibrous structures.Published in Nature Communications, this study also saw contributions from University of Cambridge, Chapman University, and Hongik University researchers. Known as 3D printing by rapid solvent exchange (3DPX), the technique allows for the creation of fibers extending tens of centimeters in length, with potential applications in robotics, medicine, and advanced materials.Unlike conventional fabrication methods, which struggle with flexibility and high aspect ratios, this approach leverages solvent exchange to enable rapid solidification of extruded polymer filaments. This process reaches speeds of 5 mm/s, significantly outpacing traditional meniscus-guided printing. By allowing fibers to solidify almost instantly, capillary-induced breakage is prevented, ensuring the stability of fine structures.In nature, there are many examples of filamentous structures that achieve a diameter of only a few microns, said, Mohammad Tanver Hossain, an engineer at the University of Illinois Urbana-Champaign in a press release. We knew it had to be possible.A spiral structure produced using embedded 3D printing. Image via M. Tanver Hossain.3D printing ultra-fine fibersExperiments showed that 1.5 m fibers could be produced using a 5 m nozzle, with aspect ratios exceeding 3,400. The researchers fine-tuned the support gel rheology and polymer composition to ensure stability, proving that even at this scale, the process remains reliable.The technique also works across a broad range of materials, including thermoplastic elastomers, polystyrene, and polyvinyl chloride (PVC). They even tested carbon nanotube-polymer nanocomposites, which could be useful for applications in electronics and sensor technology.Beyond individual fibers, the team successfully printed hair-like arrays anchored onto elastomeric substrates, with diameters under 2 m and lengths surpassing 1,500 m. These could prove valuable in tactile sensors, microneedles for drug delivery, and microfluidic devices, taking inspiration from natures own solutions for sensing and adhesion.Scalability was another key focus. A multi-nozzle printing system demonstrated the ability to fabricate multiple structures at once, with a nine-nozzle manifold producing identical prints in parallel. This capability enhances industrial applications, where efficiency and precision are equally important.The team also experimented with coils, spirals, and curved filaments, showing that the printing speed and the gels yield stress have a direct impact on how well a filament holds its shape. At higher yield stress values, the gel provided better mechanical support, preventing filaments from shifting during extrusion. Slower printing speeds allowed for more controlled deposition, ensuring that fibers adhered closely to the intended trajectory.Compared to existing methods, 3DPX sets a new record for feature size in direct ink writing. Previous embedded 3D printing techniques, such as those using curable silicone elastomers, struggled to get below 8 m, while this approach cuts that down to 1.5 m. Unlike electrohydrodynamic (EHD) printing and aerosol jet printing, which tend to be slow and require external supports, 3DPX works faster and allows for freeform, unsupported printing.As with any research, this study also faced its distinct challenges. Handling ultra-high-aspect-ratio fibers after printing remains tricky, and further refinements in material formulations and support gel properties could help improve stability.According to Hossain, this method holds strong potential, as ultra-fine and long fibers could be combined with functional materials to enable replication of nature-inspired fibrous structures.Broader advances in micro-3D printingAway from University of Illinois, other researchers have also tackled challenges in micro-3D printing, exploring different methods to enhance precision and efficiency.Last year, Israeli 3D printer manufacturer Nano Dimension 3D printed a micro-scale medical device to record neuronal activity in mice for a biomedical research project. Partnering with Qubecs CERVO Research Center, Universit Laval, and Bordeaux University, and Institut des Maladies Neurodgnratives (IMN) researchers, the company used its Fabrica Micro 3D printer to achieve the micron-level precision needed for the 2.7 mm-wide brace.Printed using bio-compatible Fabrica Medical M-810 material, the device features 110m-sized holes for electrodes and was fabricated in just one week, significantly reducing the production time from several months. The brace ensured stable electrode placement despite animal movements, allowing researchers to overcome previous limitations in studying dorsal horn neurons in awake mice.Elsewhere, Stanford University researchers developed a high-speed roll-to-roll CLIP (r2rCLIP) 3D printing process capable of producing up to one million microscale particles per day. By integrating continuous liquid interface production (CLIP) with a modular film system, the team replaced the static build plate with a PET film assembly line, automating printing, washing, curing, and removal.This fully automated system enables high-resolution, high-throughput micro-3D printing, with applications in drug delivery, microrobotics, and advanced materials. The research, led by Joseph DeSimones lab, was published in Nature, showcasing its potential for scalable 3D printing of complex microscopic structures.What3D printing trendsshould you watch out for in 2025?How is thefuture of 3D printingshaping up?To stay up to date with the latest 3D printing news, dont forget to subscribe to the 3D Printing Industry newsletter or follow us on Twitter, or like our page on Facebook.While youre here, why not subscribe to our Youtube channel? Featuring discussion, debriefs, video shorts, and webinar replays.Featured image shows a spiral structure produced using embedded 3D printing. Image via M. Tanver Hossain.Ada ShaikhnagWith a background in journalism, Ada has a keen interest in frontier technology and its application in the wider world. Ada reports on aspects of 3D printing ranging from aerospace and automotive to medical and dental.
0 Comentários
·0 Compartilhamentos
·53 Visualizações