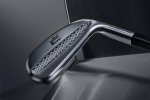
New 3D Printed Golf Irons Introduced by Cobra Golf
3dprintingindustry.com
Californian sports equipment brand Cobra Golf has launched its new range of 3D printed King Tour Irons. Fabricated using Direct Metal Laser Sintering (DMLS) additive manufacturing, the new golf clubs feature a 3D printed lattice structure that reportedly reduces weight by 33%.Made from 316 stainless steel, the blades have been designed to combine a high degree of forgiveness with the sleek look and soft feel of a professional players iron. As with Cobra Golfs previous 3D printed LIMIT3D clubs, its new Irons seek to unlock high-level performance for all players, from Tour pros to mid- and high-handicap golfers.Mike Yagley, Vice President of Innovation & AI at Cobra Golf, called LIMIT3D the first commercially available 3D printed clubs, adding they sold out so quickly we had to make more. According to Yagley, the new Tour irons offer the same premium construction, performance, and feel, but will now be available as a standard COBRA model.Available for pre-sale now, the 3D printed golf wedges will be released at retail from March 21, 2025. Prices for the standard 4-PW set (right-hand and left-hand) start at 2,199. Each club features KBS $-Taper 110 steel shafts and Lamkin Crossline grips as the default setup. According to Cobra, limited quantities are available while stocks last. A 3-iron, Gap Wedge, and custom shafts and grips can also be ordered via the companys online store.Cobra Golfs new 3DP Tour Iron. Image via Cobra Golf.Cobra Golf introduces new 3D printed ironsThe new range of King Tour Irons builds on Cobra Golfs existing additive manufacturing experience. Ryan Roach, the companys Director of Innovation, previously told 3D Printing Industry We have a long history with additive. He explained that the Puma subsidiary first adopted additive manufacturing to accelerate its development process.Cobra soon shifted to end-use production to fabricate specialist clubs for its partner players. This includes 6-time PGA Tour winner Rickie Fowler, who leveraged a unique 3D printed putter featuring enhanced roll consistency and put distance. According to Roach, these limited runs validated the value of 3D printing, paving the way for increased use in the commercial market.In 2020, Cobra introduced the 3D printed KING Supersport-35 putter. This club, produced in collaboration with HP and Parmatech, features a fully-3D printed metal body with a weight-optimized internal lattice structure. HP Metal Jet 3D printers were used to manufacture the putters due to their high production speeds and design adaptability. Cobra prototyped 35 designs in just eight months. The following year, the company launched a full line of KING 3D printed multi-material putters.Last year, Cobras LIMIT3D launch represented a big deal in golf, according to Roach, with some players considering it the biggest innovation in irons for 10 years. 3D printing the clubs reportedly allowed Cobra to unlock designs that arent possible with casting and forging to make the club look and feel better, Roach added.Close-up of Cobra Golfs 3D printed Tour Iron. Image via Cobra GolfThe latest product line seeks to continue this innovation. Though similar in size to Cobras conventionally forged King Tour irons, the new 3D printed clubs are longer and more forgiving. This level of performance is reportedly unlocked by their complex internal lattice, which can only be produced via additive manufacturing. The structure, also found in the LIMIT3D clubs, was designed using nTops engineering software.The New York City-based design specialists platform was much more efficient than Cobras previous software. It allowed the company to more quickly iterate and determine the best lattice for our product, explained Roach. According to Cobra, this complex internal lattice reduces weight, allowing designers to reposition up to 100g of tungsten lower in the clubheads heel and toe area. This, in turn, lowers the center of gravity and increases the moment of inertia (MOI), translating to improved forgiveness and consistency.The 3D printed Tour Irons internal lattice structure. Image via Cobra Golf.3D printed sporting goodsCobra Golfs continued adoption of additive manufacturing reflects the growing market for 3D printed sporting goods. This trend is clear within the golfing sector, where Cobra is not the only brand leveraging metal 3D printing.Last year, the Japanese lifestyle golf brand Designer launched a range of titanium 3D printed golf club heads. Fabricated using FS200M metal LPBF 3D printers from Farsoon Technologies, the clubs offer added strength while being lightweight. According to Farsoon, the novel head design and self-supported internal structures offer top-of-the-line performance for players seeking greater distance, accuracy, and stability. The company claims that its 3D printers also reduced cost per part by 70% from design to production compared to conventional manufacturing processes.Away from golf, US sports equipment manufacturer Wilson Sporting Goods Co. made headlines last year with the commercial launch of its 3D printed airless basketball. Co-developed with 3D design specialists General Lattice, 3D printer manufacturer EOS, and post-processing company DyeMansion, the basketball is fully functional and meets NBA ball regulations. It features a 3D printed lattice structure, eliminating air-retention challenges within traditional ball manufacturing.Who won the 2024 3D Printing Industry Awards?Subscribe to the 3D Printing Industry newsletter to keep up with the latest 3D printing news.You can also follow us on LinkedIn, and subscribe to the 3D Printing Industry Youtube channel to access more exclusive content.Featured image shows Cobra Golfs new 3D printed Tour Iron. Image via Cobra Golf.
0 التعليقات
·0 المشاركات
·74 مشاهدة