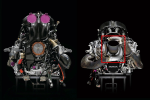
3D Printing at Honda adds New Value for Automotive Giant
3dprintingindustry.com
Japanese automotive manufacturer Honda is exploring 3D printing for automobile, motorcycle, motorsports, power, aerospace, and wheelchair racing products. The company recently reported it is investigating how laser powder bed fusion (LPBF) technology can add new value to manufacturing processes.Based in Minato, Tokyo, the global car maker says that 3D printing unlocks fast and efficient production of complex shapes at lower costs than conventional methods. It also pointed to the potential of 3D printing smart factories that could significantly shorten the process from development to mass production.Notably, Honda already uses in-house LPBF 3D printing to fabricate car engine components. These include pistons and turbine housings used in Oracle Red Bull Racings F1 cars. The company also leverages metal additive manufacturing to produce lightweight, topology optimized aluminum handles for racing wheelchairs.Hondas 3D printed turbine housing. Photo via Honda.Metal 3D printing at Honda Honda is working to increasingly integrate metal additive manufacturing into its development and production processes. It already 3D prints metal parts in house using LPBF technology, including systems from Nikon SLM Solutions.The firm claims to have accumulated AM expertise by optimizing parameters, recording material deposition to assess melting state, and monitoring temperature and laser power. Process simulation technology is also used to predict and mitigate potential deformations and improve the dimensional accuracy of its parts. Honda noted that metal 3D printing allows it to fabricate complex shapes that are impossible to achieve with conventional casting and forging techniques.In 2019, the company partnered with Oracle Red Bull Racing to supply engines for their F1 cars. Metal additive manufacturing helped them quickly adapt to specification changes and create complex, thin-walled parts. This, in turn, reduced lead times and lowered costs.The racing giant, which powers reigning F1 champion Max Verstappen, previously leveraged engine pistons produced using aluminum forging. Honda switched to LPBF 3D printing, using iron powder for added strength against combustion pressure. Though iron is heavier than aluminum, novel 3D printed geometries made the final parts lighter than conventional counterparts.Similarly, the F1 teams turbine housing parts were previously made in inconel, a heat-resistant nickel alloy, using precision casting. These large components feature thin wall sections, leading to deformation issues during conventional manufacturing. 3D printing the housings reportedly removed these issues, allowing Honda to meet strict requirements while reducing costs and cutting production times.Hondas 3D printed turbine housing in the F1 racing car engine. Image via Honda.Metal additive manufacturing technology is also used to fabricate aluminum handlebars for Hondas racing wheelchairs, also known as handcycles. By leveraging 3D printing, the leading motorcycle brand aimed to reduce weight and increase safety during collisions.Optimal handlebar geometries vary depending on the shapes of each athletes hands. Previously, these parts were made of welded aluminum pipes, offering minimal scope for customization. To overcome this, Honda used topology optimization to design a more ergonomic component while minimizing weight and optimizing strength. According to the Japanese firm, the handlebars mesh grip, key to weight reduction, can only be manufactured with metal LPBF 3D printing.Hondas racing wheelchair with 3D printed handlebars. Photo via Honda.Additive manufacturing for automotive applicationsThe role of 3D printing in automotive manufacturing is growing, as car makers target material, cost, and time savings for prototyping, tooling, and end-use parts.In December 2024, core manufacturer Laempe Mssner Sinto delivered six sand 3D printers to automotive giant BMWs foundry in Landshut, Germany. The automated, high-volume binder jet 3D printing production line can fabricate sand cores and molds of critical car components. BMW is already using the technology to produce its latest range of six-cylinder vehicles. This additive manufacturing solution reportedly eliminates manual steps, offering fully automated production and core removal.Elsewhere, Japanese SUV manufacturer Subaru Corporation utilized HP Inc.s Multi Jet Fusion technology to 3D print parts for its Legacy Outback Boostgear Package concept car. Announced at Tokyo Auto Salon 2024, the collaboration with HP Japan and DMM.make 3D Print is exploring new additive manufacturing possibilities in automotive design and production.HPs Jet Fusion 4200 and 5420W 3D printers have allowed Subaru to remove the need for molds. This reportedly unlocks rapid production of parts with unique geometries. HPs 3D High Reusability PA 12, a nylon material known for heat and weather resistance, was also leveraged. It reportedly combines the necessary structural strength with an 80% material recycling rate.More recently, Ford Motor Company, a global automotive manufacturer established in 1903, announced it is using 3D printing to prepare for its first F1 race in two decades. Set to compete during the 2026 season, Ford has already produced over 1,000 3D printed car parts at its additive manufacturing labs, including cold plates for batteries and cooling plates for other systems. These will feed into the race cars combustion engine and hybrid technology.Who won the 2024 3D Printing Industry Awards?Subscribe to the 3D Printing Industry newsletter to keep up with the latest 3D printing news.You can also follow us on LinkedIn, and subscribe to the 3D Printing Industry Youtube channel to access more exclusive content.Featured image shows Hondas 3D printed turbine housing in the F1 racing car engine. Image via Honda.
0 Comments
·0 Shares
·23 Views