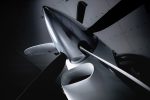
GE Aerospaces 3D Printed Catalyst Engine Receives New FAA Certification
3dprintingindustry.com
GE Aerospace has received US Federal Aviation Administration (FAA) certification for its 3D printing-enabled Catalyst turboprop engine.The Ohio-based aerospace manufacturer previously announced that approximately 30% of the Catalysts parts are 3D printed. Notably, 855 conventionally manufactured components have been reduced to just 12 3D printed titanium parts.GEs modern centerline, clean-sheet turboprop also offers a 16:1 overall pressure ratio. This reportedly unlocks 18% superior fuel consumption and up to 10% higher cruise power than competing engines. Part of GE Aerospaces next-generation Engine suite, the Catalyst is being fabricated at the companys Avio Aero facilities in Italy, the Czech Republic, Poland, and Germany.According to GE Aerospace, the Catalyst is the first turboprop to be certified under the FAAs latest standards, which include over 20 new requirements. The FAR (Federal Aviation Regulation) Part 33 certification saw 23 Catalyst engines undergo over 8,000 hours of operation, with more than 190 component tests.The certification of the Catalyst engine is a significant milestone for our company and a proud moment for all our team members who have dedicated their efforts to the design, development, and testing of this brand-new European turboprop engine, commented Riccardo Procacci, President and CEO of Propulsion and Additive Technologies at GE Aerospace. We are now fully committed to supporting the production ramp-up of the engine towards the entry into service in support of our customers.GE Aerospaces Catalyst Turboprop engine. Photo via GE Aerospace.Catalyst turboprop engine receives FAA CertificationGE Aerospace has called Catalyst the first, new centerline, clean-sheet advanced turboprop of the 21st century. Paul Corkery, Catalyst General Manager at Avio Aero, commented that the company is pleased with the performance of the engine throughout its ground and flight test campaigns.The propeller-based engine features two stages of variable stator vanes and cooled high-pressure turbine blades. Additive manufacturing has also helped reduce its weight by approximately 100 lb (45.4 kg) and simplified maintenance by decreasing the number of components.Catalyst also stands out thanks to its full authority digital engine control or FADEC technology. This allows pilots to fly with a single lever, instead of the three needed for most turboprop engines. In turn, the flying experience is simplified to feel more like that of a jet.Looking ahead, the fully certified Catalyst will power Wichita plane manufacturer Textron Aviations new Beechcraft Denali turboprop aircraft. Textron selected GE Aerospaces 3D printed propulsion system back in 2015 when it was known as the Advanced Turboprop (ATP) engine. Three years later, the turboprop completed a successful test fire at a GE Aviation test cell near Prague, Czech Republic.Catalyst will also be used on Airbus, Dassault Aviation, and Leonardos jointly developed Eurodrone unmanned aerial vehicle (UAV). A twin-engine reconnaissance aircraft, Eurodrone has already attracted orders from NATOs France, Germany, Italy, and Spain. The Airbus-led project selected Catalyst as their engine of choice in 2022. At the time Jean-Brice Dumont, Head of Military Aircraft at Airbus, identified Catalyst as the best solution due to its superior performance, lower developmental risk, better in-service economics and growth potential.Beechcraft Denali airplane. Photo via GE Aerospace.3D printed aerospace enginesCatalyst is not the only 3D printed aerospace engine in the aviation market. Last year, GE Aerospace announced plans to scale the production of its 3D printed LEAP and GE9X engines. Through a $650 million investment into its global manufacturing plants and supply chain, the US aerospace firm hopes to grow its production capacity and meet demand from commercial and defense clients.Each LEAP engine includes 19 3D printed fuel nozzles that reportedly increase fuel efficiency by 15%, compared to CFM56 engines. GEs landmark 3D printed fuel nozzle tips are 25% lighter and five times more durable than their conventionally manufactured counterparts. They also feature a complex geometry that pre-mixes jet fuel before it is fed into the combustion chamber, further boosting engine efficiency. Additionally, the companys GE9X engines, designed for Boeing 777X jets, include over 300 3D printed parts.The role of 3D printing is also growing in the production of rocket engines. At Formnext 2024, metal 3D printer manufacturer Eplus3D unveiled what it called the worlds largest single-piece metal 3D printed rocket thruster. Developed with engineering services provider LEAP71, the rocket delivers 200 kN of thrust and stands over 1.3 meters tall.Elsewhere, German aerospace start-up POLARIS Spaceplanes completed successful flight tests of its 3D printed aerospike engine. Designed to power the companys MIRA II spaceplane demonstrator, the AS-1 linear engine completed a three-second burn, achieving 4 m/s acceleration and 900 newtons of thrust. This represented the first in-flight test of a linear aerospike, marking a notable milestone in the Bremen-based companys efforts to begin commercial spaceflight operations in 2028.Who won the 2024 3D Printing Industry Awards?Subscribe to the 3D Printing Industry newsletter to keep up with the latest 3D printing news.You can also follow us on LinkedIn, and subscribe to the 3D Printing Industry Youtube channel to access more exclusive content.Featured image shows GE Aerospaces Catalyst Turboprop engine. Photo via GE Aerospace.
0 Kommentare
·0 Anteile
·37 Ansichten