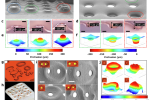
New study into 3D microelectrode technology could improve neural interfaces
3dprintingindustry.com
Researchers from Pusan National University and Seoul National University have introduced a new method that could reshape neural recording and stimulation.Led by Associate Professors Joonsoo Jeong and Kyungsik Eom, their findings highlight a technique known as microelectrothermoforming (ETF), which simplifies the process of creating intricate 3D microstructures on microelectrode arrays (MEAs) using thermoplastics and 3D printed molds.For years, researchers have faced hurdles when designing 3D neural interfaces. Conventional microelectromechanical system (MEMS) technologies require multiple fabrication steps to build 3D microstructures onto planar MEAs, making the process complex and limiting the variety of shapes that can be achieved. Methods like photolithography, vacuum deposition, and etching have traditionally been used, but they come with design restrictions.Published in npj Flexible Electronics, the ETF technique offers a way around these obstacles, allowing flat electrode arrays to be shaped into 3D microstructures in a single step using molds that are 3D printed but not part of the final electrode itself.The idea for this study came from a simple observation of plastic lids on take-out coffee cups. I realized that this plastic forming method could be applied at a microscopic level to create 3D structures for neural electrodes, says Dr. Jeong.Versatile 3D structures with diverse shapes and heights created by the one-step ETF process. Image via PNU.Improving neural stimulation and durabilityHaving applied the ETF technique, the research team successfully produced MEAs with 80-micrometer-high protrusions and recesses. This technique enables different shapes to be created within the same electrode array, paving the way for more customized microelectrode structures tailored to specific neural applications.Tests in retinal stimulation experiments showed that these 3D MEAs significantly outperformed conventional planar electrodes, requiring 1.7 times less stimulation current and improving spatial resolution by 2.2 times.One of the biggest advantages of ETF is its ability to shape 3D microstructures without additional processing steps. The technique relies on liquid crystal polymer (LCP) as the thermoplastic substrate due to its durability, chemical resistance, and biocompatibility.LCPs low water absorption also makes it well-suited for long-term implantation. While LCP was the material of choice in this study, the researchers note that ETF could be applied to other thermoplastics commonly used in biomedical engineering.The effectiveness of these 3D MEAs was further validated through computational simulations and ex vivo experiments with mouse models. The findings revealed that the 3D structures improved the localization of electric fields, reducing the current needed for effective stimulation.Calcium imaging of mouse retinas confirmed that protruding electrodes activated retinal ganglion cells more efficiently than planar electrodes, both in terms of lower required current and higher spatial precision.Beyond performance, durability was another key factor. Mechanical and electrochemical evaluations confirmed that the ETF-fabricated MEAs maintained their integrity under physiological pressure conditions.Electrical properties remained stable even after repeated deformation, and finite element analysis showed that the new design minimized mechanical strain on the embedded conductive layers, ensuring long-term reliability.The implications of this research extend beyond neural implants. Researchers are looking into its potential for wearable electronics, organoid studies, and lab-on-a-chip systems, where precise 3D microstructures could make a real impact. The focus now is on refining fabrication for broader medical applications.Ex vivo retinal experiments for evaluating the effectiveness of ETF MEA for subretinal stimulation. Image via PNU.3D printing advances in neural implants3D printing has been, infrequently, deployed in the neural implants field.Back in 2020, Massachusetts Institute of Technology (MIT) researchers developed soft, flexible brain electrodes using 3D printing and conducting polymer materials. Designed to conform to the brains natural contours, these implants offered a safer and more adaptable alternative to traditional metal electrodes, which often lead to inflammation and scarring.By refining poly (3,4-ethylenedioxythiophene) polystyrene sulfonate (PEDOT:PSS) into a printable hydrogel, the team ensured the material retained its electrical conductivity while maintaining a soft structure. Early tests on mice confirmed the electrodes ability to detect neural signals with high precision.Elsewhere, researchers at Carnegie Mellon University developed a novel class of high-density neural probes using nanoparticle 3D printing to enhance neural data recording. Supported by a $1.95 million NIH grant under the BRAIN Initiative, the project aimed to create a cost-effective manufacturing method for brain implants.Led by Rahul Panat and Eric Yttri, the team used aerosol jet printing (AJP) to fabricate customizable, ultra-high-density microelectrode arrays, surpassing conventional probes in resolution and implantability. By enabling precise brain-machine interfaces (BMIs) and neuroprosthetic applications, the technology significantly improved electrode accessibility while reducing tissue damage.What3D printing trendsshould you watch out for in 2025?How is thefuture of 3D printingshaping up?To stay up to date with the latest 3D printing news, dont forget to subscribe to the 3D Printing Industry newsletter or follow us on Twitter, or like our page on Facebook.While youre here, why not subscribe to our Youtube channel? Featuring discussion, debriefs, video shorts, and webinar replays.Featured image shows versatile 3D structures with diverse shapes and heights created by the one-step ETF process. Image via PNU.Ada ShaikhnagWith a background in journalism, Ada has a keen interest in frontier technology and its application in the wider world. Ada reports on aspects of 3D printing ranging from aerospace and automotive to medical and dental.
0 Commentaires
·0 Parts
·41 Vue