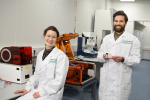
New study explores Xolography for bioprinting of hydrogels in tissue engineering
3dprintingindustry.com
Researchers from Eindhoven University of Technology (TU/e) have introduced a novel way to fabricate hydrogels using Xolography technology from Berlin-based 3D printer manufacturer xolo.Led by Lena Stoecker and Miguel Dias Castilho, their study showcases how this technique allows for precise control over the structure and mechanical properties of hydrogels, a material widely used in tissue engineering.Tissue engineering depends on extracellular environments that support and guide cellular activity through biochemical, mechanical, and structural cues. However, existing fabrication technologies failed to meet the high expectations, providing the necessary spatial precision. Published in Advanced Materials, this study presents Xolography as a method that can print centimeter-scale hydrogel structures within minutes, while offering fine control over their shape and stiffness at a microscopic level.My dream for Xolography would be to develop into a technology that is actually able to create tissue and organ models to study disease and develop cures, explains Stoecker.Lena Stoecker and Miguel Dias Castilho pose in front of the tissue 3D printer in the lab. Photo via Bart van Overbeeke.Grayscale light projection enables tunable hydrogel propertiesTo advance hydrogel design, the researchers developed a water-soluble photoinitiator system and tested a range of naturally derived, synthetic, and thermoresponsive hydrogels.Their method successfully created structures with positive features as small as 20 m and negative features around 100 m. Having shifted from binary to grayscale light projection, they achieved precise spatial modulation of stiffness, with compressive moduli ranging from 0.2 to 16 kilopascals (kPa), without altering the base material composition.Xolographys ability to control mechanical properties stems from its capacity to adjust the degree of crosslinking (DoC) during printing. The technology used in this study was provided by the Berlin-based manufacturer, whose Xube 3D printer was instrumental in enabling the dual-color volumetric printing process.By varying light intensity in a grayscale projection system, the researchers demonstrated localized stiffness control at a microscale resolution. This level of customization opens up possibilities for tailoring biomaterial scaffolds to specific tissue types, with potential applications in regenerative medicine.The study also delved into the use of thermoresponsive hydrogels, which exhibit shape-shifting behavior in response to temperature changes. Leveraging Xolographys grayscale projection, the researchers fabricated hydrogels capable of reversible shape transformations, demonstrating a new approach to dynamic biomaterials. This technique presents new possibilities for applications in tissue engineering and soft robotics, where controlled shape changes could prove invaluable.One of the promising aspects of this research was the successful integration of cell-laden printing. The team incorporated viable cell aggregates into hydrogel constructs, demonstrating that Xolography is compatible with bioprinting.These 3D printed cells maintained metabolic activity and exhibited distinct behaviors depending on their position within the hydrogel. However, the study also acknowledged that further optimization of hydrogel formulations is necessary to enhance cell viability and post-printing biological functions.Moreover, the implications extend across tissue engineering, regenerative medicine, and in vitro modeling. Looking ahead, the research team aims to refine hydrogel formulations, improve biocompatibility, and explore the scalability of this technique for larger biological constructs.Our research is a necessary first step for the future of tissue engineering. Right now, it can print physiologically more relevant 3D environments for cell culture, and in the long term, it could help make 3D printed organs a reality, says Dias Castilho.The new Xube. Image via Xolo.Volumetric 3D printing for medical applicationsBeyond the Eindhoven research, previous developments in volumetric bioprinting further demonstrate its potential for functional tissue fabrication.For instance, Utrecht University researchers fabricated functional liver tissue using an ultrafast volumetric bioprinting technique. Having employed visible light tomography, the method made cells transparent with the help of iodixanol, allowing high-resolution printing of miniature liver organoids while preserving their biological functions.In under 20 seconds, they 3D printed functional liver units capable of detoxifying harmful compounds, mimicking the livers natural processes. The team also designed porous architectures to facilitate nutrient flow, replicating the role of blood vessels.In 2023, researchers at UMC Utrecht advanced volumetric bioprinting by achieving three key developments: creating biologically functional regions within 3D printed cells, improving cell survival using granular gels, and combining volumetric bioprinting with melt electrowriting to reinforce 3D printed blood vessels.As per the team, these efforts were aimed at increasing the clinical applicability of bioprinting by enabling precise control over cellular interactions and tissue formation. Their work could support the development of bioengineered scaffolds that guide cell growth and contribute to the fabrication of complex organ structures for medical use.What3D printing trendsshould you watch out for in 2025?How is thefuture of 3D printingshaping up?To stay up to date with the latest 3D printing news, dont forget to subscribe to the 3D Printing Industry newsletter or follow us on Twitter, or like our page on Facebook.While youre here, why not subscribe to our Youtube channel? Featuring discussion, debriefs, video shorts, and webinar replays.Featured image shows Lena Stoecker and Miguel Dias Castilho pose in front of the tissue 3D printer in the lab. Photo via Bart van Overbeeke.Ada ShaikhnagWith a background in journalism, Ada has a keen interest in frontier technology and its application in the wider world. Ada reports on aspects of 3D printing ranging from aerospace and automotive to medical and dental.
0 Commenti
·0 condivisioni
·65 Views