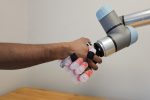
Breakthrough hybrid prosthetic hand now features human touch via sensors
3dprintingindustry.com
Researchers from Johns Hopkins University (JHU), Florida Atlantic University (FAU) and the University of Illinois Chicago (UIC), have developed a prosthetic hand designed to mimic the human touch.Led by JHU biomedical engineering professor Nitish Thakor, and biomedical engineer Sriramana Sankar, this development could improve prosthetic solutions for individuals with hand loss and refine how robotic arms interact with physical environments. The work was supported by funding from the U.S. Department of Defense (DoD) through the Orthotics and Prosthetics Outcomes Research Program and the National Science Foundation (NSF).The goal from the beginning has been to create a prosthetic hand that we model based on the human hands physical and sensing capabilitiesa more natural prosthetic that functions and feels like a lost limb, said Sankar. We want to give people with upper-limb loss the ability to safely and freely interact with their environment, to feel and hold their loved ones without concern of hurting them.Hybrid robotic hand with neuromorphic tactile sensing inspired by the human hand. Image via JHU.A hybrid prosthetic hand with human-like sensingUnlike traditional robotic hands that tend to be either too rigid or too soft, this system balances both elements. This results in a grip that is firm enough to securely hold a water bottle yet delicate enough to pick up a fragile plastic cup without damaging it.To achieve this, the prosthetic hand uniquely combines the flexibility of soft robotics with the strength of traditional rigid robotics, allowing it to grasp and handle various everyday items more naturally. Additionally, the hands fingertips feature three tactile sensor layers, each inspired by the human skins sensory receptors.These include piezoresistive layers sensitive to light touch and deformation, as well as a piezoelectric layer designed to detect subtle vibrations, mirroring the sophisticated sensory experience of human fingers.The hybrid robotic finger incorporates three independently actuated soft joints made from chemical manufacturing firm Smooth-Ons Dragon Skin 10 silicone, supported by 3D printed polylactic acid (PLA) rigid skeletal structures.Finite element analysis and practical tests showed the hybrid finger could achieve significant flexibility, 130 curvature and a flexion angle of 208, at an actuation pressure of just 7 psi. This is notably more efficient compared to purely soft robotic fingers, which typically require much higher pressures.If youre holding a cup of coffee, how do you know youre about to drop it? Your palm and fingertips send signals to your brain that the cup is slipping, Thakor said. Our system is neurally inspiredit models the hands touch receptors to produce nervelike messages so the prosthetics brain, or its computer, understands if something is hot or cold, soft or hard, or slipping from the grip.During lab tests, the hybrid finger demonstrated over three times the grasping force of fully soft robotic alternatives. The embedded multilayered tactile sensors proved highly effective in distinguishing between 26 diverse textures, achieving a notable average accuracy of 98.38%, compared to roughly 83% accuracy from standard soft and rigid prosthetic fingers.To process tactile signals efficiently, the team used neuromorphic encoding, a method inspired by natural nerve communication. This approach significantly enhanced the hands capability to discriminate textures.Practical demonstrations further highlighted the hands utility, with successful electromyography (EMG) controlled experiments involving the grasping of various objects from the Southampton Hand Assessment Procedure (SHAP), ranging from delicate to heavier items.Remarkably, the hybrid robotic hand achieved a 99.69% accuracy rate when identifying and differentiating 15 common everyday objects during grasping tasks. Items tested included objects of varying shapes, textures, and levels of softness, showcasing the prosthetic hands adaptability and precision.Having termed the research a breakthrough, the researchers still see room for improvement, like adding rigid joints to boost gripping strength and extending sensory coverage beyond the fingertips. They also suggested exploring nerve stimulation to provide users with a more natural, lifelike sense of touch.Hybrid finger with multilayered neuromorphic tactile sensing. Image via JHU.Improving grasp and artificial touch in prostheticsIn a similar vein, other teams have also been exploring prosthetic solutions aimed at enhancing practical usability.For instance, prosthetic 3D printing firm Open Bionics delivered its advanced Hero Arm prostheses to a medical facility in Germany, aiding Ukrainian soldiers injured by landmine explosions. Equipped with forearm-activated sensors, the Hero Arm allowed precise control over its movable thumb and fingers, providing significantly better grasping capability than traditional prosthetics.One of the recipients, Vitalii Ivashchuk, described feeling pleasantly surprised by how functional and natural the prosthesis felt, noting it exceeded his expectations. Coordinated by Ukraines Superhumans Foundation with support from Mastercard, this initiative aimed to expand prosthetic and rehabilitation services in Ukraine.Scientists at the University of Bristol developed an artificial fingertip, called TacTip, enabling prosthetic limbs to feel objects. Created using 3D printed structures mimicking human skins papillae, this device sensed object shapes and transmitted artificial nerve signals resembling natural tactile responses.During testing, TacTip accurately responded to pressure similar to human skin but showed slightly lower sensitivity in detecting object orientations due to its thicker artificial skin. Despite this, researchers observed significant similarities between artificial and natural sensory responses. The team suggested that with further refinement, TacTip could significantly improve robotic dexterity, enabling robots to automate sensitive tasks like fruit picking or offering enhanced tactile sensations in prosthetic hands.What3D printing trendsshould you watch out for in 2025?How is thefuture of 3D printingshaping up?To stay up to date with the latest 3D printing news, dont forget to subscribe to the 3D Printing Industry newsletter or follow us on Twitter, or like our page on Facebook.While youre here, why not subscribe to our Youtube channel? Featuring discussion, debriefs, video shorts, and webinar replays.Featured image shows the hybrid prosthetic hand demonstrating a gentle yet firm handshake. Image via JHU.Ada ShaikhnagWith a background in journalism, Ada has a keen interest in frontier technology and its application in the wider world. Ada reports on aspects of 3D printing ranging from aerospace and automotive to medical and dental.
0 Comments
·0 Shares
·52 Views