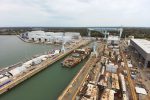
New US Navy Aircraft Carrier Features 3D Printed Valve Manifold
3dprintingindustry.com
US shipbuilding firm Huntington Ingalls Industries (HII) has successfully installed a 3D printed valve manifold assembly into a new US Navy aircraft carrier. The United States largest military shipbuilder has installed over 55 3D printed parts to-date at its Newport News Shipbuilding (NNS) division. It plans to deploy at least another 200 by the end of 2025.HIIs 3D printed assembly was integrated into the US Navys third Gerald R. Ford-class aircraft carrier, the USS Enterprise (CVN 80). Measuring approximately five feet long and weighing 1,000 pounds, the large-scale component was fabricated with the help of metal DED additive manufacturing specialist DM3D. It was installed at the NNS facility in Virginia and is reportedly the first 3D printed part of its kind to be used in US aircraft carrier construction.Looking ahead, the Fortune 500 company plans to install similar 3D printed manifold assemblies on the USS Doris Miller, a Gerald R. Ford-class carrier set to be launched in 2029. According to HII, additive manufacturing reduces scheduling risks and increases production efficiency compared to conventional casting methods.What started as a proof of concept quickly turned into a tangible result that is making a meaningful difference to improve efficiencies in shipbuilding, commented NNS vice president of engineering and design Dave Bolcar. The benefits of this innovation will extend well beyond Enterprise (CVN 80), as we incorporate our expertise in additive manufacturing into the fundamentals of shipbuilding.HIIs 3D printed valve manifold assembly installed on the USS Enterprise. Photo via HII.3D printing enhances aircraft carrier constructionAdditive manufacturing is nothing new at HII. The shipbuilding giant, which employs 44,000 people, is a certified and approved supplier of 3D printed components for the US Navys Naval Sea Systems Command (NAVSEA).Back in 2018, the US warship builder signed a deal with leading 3D printer manufacturer 3D Systems to qualify metal additive manufacturing for ship construction. Through the contract, HII adopted 3D Systems ProX DMP 320 metal 3D printing technology to shift elements of its production to additive manufacturing. At the time, the shipbuilding firm planned to use its new large-scale 3D printer to fabricate marine-based alloy replacement parts for castings as well as valves, housings and brackets for future nuclear-powered warships.The following year, HII produced a 3D printed piping assembly for the US Navy aircraft carrier USS Harry S. Truman (CVN 75). Said to be the first transformational part installed on a nuclear-powered aircraft carrier, the component underwent a year-long onboard evaluation to assess the value of 3D printed warship components.In 2021, HII again collaborated with 3D Systems to develop corrosion-proof metal powders for maritime 3D printing. The Rock Hill-based OEM formulated novel Copper-Nickel (CuNi) and Nickel-Copper (NiCu) alloys specifically designed to yield robust, temperature-resistant parts. By 3D printing the materials instead of using conventional casting, HIIs Newport-based shipbuilding division believes seaworthy valves, housings, and brackets can be produced with 74% lower lead times.HIIs latest 3D printed component, produced alongside DM3D, is a specialized valve manifold assembly that allows a single source of fluid to be transported to multiple points on the ship. It has been installed in the new nuclear-powered warships pump room. The USS Enterprise (CVN 80) is set to be launched with the assembly later this year.The USS Enterprise (CVN 80) under construction. Photo via HII.US Navy adopts additive manufacturingThe US Navy is increasingly adopting additive manufacturing to help overcome global supply chain challenges.Earlier this year, Australian large-format Wire Arc Additive Manufacturing (WAAM) company AML3D delivered 3D printed prototype tailpiece components to support the US Navys Virginia Class nuclear submarine program. Provided through the trilateral AUKUS partnership, the 3D printed Copper-Nickel components are undergoing testing before being installed on a Virginia-Class submarine for naval trials later this year.Valued at approximately A$156,000, the parts were fabricated in under five weeks, much quicker than the 17-month lead time required by conventional manufacturing methods. AML3Ds latest delivery builds on a two-year collaboration with the US Department of Defense (DoD) to support the US Navys submarine industrial base. The North Plympton-based companys Scale Up strategy sees it acquire US defense contracts to become a point-of-need additive manufacturing solution with its ARCEMY WAAM technology.In other news, Bechtel Plant Machinery Inc. (BPMI) selected metal 3D printing technology from US firm Velo3D to support the US Naval Nuclear Propulsion Program. This includes Velo3Ds Sapphire XC large format 3D printer calibrated for stainless steel 415.Operated by materials company ATI at its manufacturing facility in Fort Lauderdale, Florida, the large-format metal 3D printer is being used to improve production of critical nuclear submarine components. Additive manufacturing will be used to fabricate parts previously made using casting, reducing lead times and optimizing the supply chain.Who won the 2024 3D Printing Industry Awards?Subscribe to the 3D Printing Industry newsletter to keep up with the latest 3D printing news.You can also follow us on LinkedIn, and subscribe to the 3D Printing Industry Youtube channel to access more exclusive content.Featured image shows the USS Enterprise (CVN 80) under construction. Photo via HII.
0 Commentarios
·0 Acciones
·54 Views