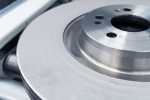
Addressing New EU Vehicle Emission Requirements with EMAGs LMD Technology
3dprintingindustry.com
German machine tools manufacturer EMAG is addressing European automotive sustainability regulations with its ELC 450 LMD laser metal deposition (LMD) technology.In November 2026, the European Union (EU) will introduce the Euro 7 emissions standard, setting stricter regulations for all road vehicles across the continent. Notably, it will impose tighter controls on particle emissions from brake disc abrasions, requiring a 27% reduction by the end of next year.Currently, most cars emit up to 40 milligrams of particulate matter per kilometer, but under Euro 7, all new vehicles must meet a significantly lower limit of just 7 milligrams. Consequently, automotive manufacturers and suppliers require new methods for creating more eco-friendly brake disks.EMAG aims to meet this need with the ELC 450 LMD, a laser metal deposition system that applies a metal coating to brake discs. This hard coating enhances corrosion and wear resistance, extends the discs lifespan, and reduces their environmental impact. Brake disks coated using LMD technology also require less maintenance, saving time and money for end users.EMAGs ELC 450 LMD coating a brake disk. Photo via EMAG.New EU regulations crack down on vehicle emissionsBrake discs are often overlooked in discussions about vehicle pollutants, which typically focus on engine-produced CO. However, concerns about brake-related particles are increasing as the EU intensifies efforts to reduce non-exhaust emissions.According to Italian 3D printer OEM Prima Additive, 21% of combustion vehicle-based particulate emissions come from the brake discs. This is generated when the brake is applied. Friction between a cars brake disk and brake pad causes materials causes 10m-scale materials to be released into the atmosphere. In addition to the 27% reduction in brake disc emissions, the Euro 7 standard will require a 13% reduction in overall automotive polluting particulate output.According to EMAG, alternative proposals to improve brake disk sustainability are flawed. For instance, the company argued that placing extraction systems near the brakes is a problematic approach. EMAG claims that these systems only remove part of the harmful emissions, while requiring automotive OEMs to completely re-design their bodywork.NAO (Non-Asbestos Organic) brake pads are also considered inadequate because they perform well only when new. According to EMAG, these asbestos-free components lose effectiveness and fail to meet the EUs new emissions standards after prolonged use.The Salach, Baden-Wrttemberg-based laser technology developer views brake disc coating as the optimal solution. In addition to lower emission rates, coated brakes offer longer service life, meaning they are replaced less often. In turn, this reduces the environmental impact of production, transportation, and disposal.3D printing sustainable brake disc coatingsWhile hard coatings of brake disks are nothing new, their adoption has previously been limited by high production costs. Conventional thermal spraying and electroplating methods do not create a metallurgical bond to the base material, meaning complex post-processing is required to bond the coating.EMAG claims its additive manufacturing-based LMD approach represents a quantum leap for coating brake disks. The company calls its approach economical and suitable for large-scale production. It also highlights reliability and variability, as different material combinations can be used to coat brake disks.Its modular, flexible, and configurable technology is designed to meet high-volume automotive manufacturing demands. For instance, process modules can be combined and expanded to meet customer requirements.Whats more, the ELC 450 LMD is available in a range of configurations tailored to production scale. The basic model features a single process module, while the ELC 450 DUO LMD features two modules, and the ELC 450 TRIO LMD boasts three. According to EMAG, this modular approach allows the company to meet wide-ranging customer requirements by accommodating different shift structures and productivity levels.Introduced in 2021, ELC 450 LMD is said to offer notable advantages over other disk coating approaches. In a blog post, Dr. Andreas Mootz, managing director of EMAGs LaserTec subsidiary, claimed that conventional high velocity oxygen fuel spraying (HVOF) methods are wasteful. This process fires the metal coating onto the brake disks at high speeds, resulting in high material losses. On the other hand, EMAGs LMD approach, which welds the metal material directly onto the brake disk, is virtually waste-free.The ELC 450 DUO LMD with two process modules. Photo via EMAG.Additive manufacturing enhances automotive sustainabilityAs the EUs new automotive regulation deadlines approach, EMAG is not the only company coating brake discs with additive manufacturing. Last year, Prima Additive collaborated with automation and robotics firm Comau to develop a high-speed coating system for Dutch automaker Stellantis.The partners developed new Rapid Coating Process cells that combine advanced laser systems, robotic arms, powder management, and directed energy deposition (DED) 3D printing. According to Prima, these systems can quickly cover a metal brake disk with a thin layer of resilient material. This increases its resistance to wear, reducing brake disk degradation-related pollution emissions by 80%.Paolo Calefati, Prima Additives CEO, called the companys laser-based approach, the most profitable and sustainable cases of laser additive manufacturing/laser cladding technology applied in mass production for automotive.Other areas of automotive production have also adopted 3D printing to unlock more eco-friendly production. Last year, GM Ventures, the venture capital arm of the US automotive firm General Motors, invested $10 million into Forge Nano, a materials company specializing in atomic layer deposition (ALD). Through a strategic partnership, the two firms are developing advanced battery materials to improve the performance and lower the cost of electric vehicle (EV) batteries.Elsewhere, British automotive manufacturer McLaren launched a new hypercar with 3D printed titanium suspension components. McLarens new hybrid car, called the W1, features 3D printed front suspension uprights and wishbones which unlock substantial weight savings. The launch followed McLarens decision to sign a multi-year collaboration with Divergent Technologies to utilize its Divergent Adaptive Production System (DAPS) 3D printing technology. This partnership aims to enhance manufacturing efficiency and create a more sustainable automotive supply chain.Who won the 2024 3D Printing Industry Awards?Subscribe to the 3D Printing Industry newsletter to keep up with the latest 3D printing news.You can also follow us on LinkedIn, and subscribe to the 3D Printing Industry Youtube channel to access more exclusive content.Featured image shows a brake disk coated using EMAGs LMD technology. Photo via EMAG.
0 Comments
·0 Shares
·49 Views