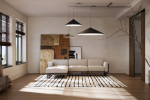
Will IC3Ds acquisition of Model No. solve its scaling challenges?
3dprintingindustry.com
Direct-to-consumer (DTC) 3D printing furniture startup Model No. has been acquired by Ohio-based 3D printing company IC3D.The sale comes as Model No. faced challenges in scaling its operations, particularly the high costs of maintaining and upgrading its specialized 3D printing equipment. As part of the acquisition, CEO Phillip Raub will depart from the company, and none of Model No.s employees will be transitioning to IC3D.The Ohio-based company has acquired the brands equipment and intellectual property but will be moving forward without its original team. Although the financial details remain undisclosed, IC3Ds Founder Michael Cao said the goal is to stabilize the business and make it profitable.We were originally looking [to sell to a] large-scale commercial furniture company, Raub told Business of Home. But [IC3D] had the best vision and the resources to preserve Model No.The 3-Piece Platform sofa and ottoman in Smoke fabric by Model No. Image via Model No.Challenges faced by Model No.Established in 2018, Model No. was founded by Vani Khosla, Jeffrey McGrew, and Jillian Northrup with a vision of using large-scale 3D printers to turn agricultural waste into furniture. The companys approach received attention for its focus on sustainability and local production.Rather than manufacturing in a centralized location and relying on long-distance shipping, Model No. planned to establish smaller production facilities in major cities. The idea was to produce furniture close to where it would be used, reducing shipping costs and the need for large inventories.With that concept, Model No. secured venture funding and built a facility in the Bay Area, primarily serving corporate clients, real estate developers, and institutions. While the model had advantages, scaling the business proved difficult.Unlike traditional furniture manufacturing, where costs are tied to labor and materials, Model No.s biggest expense was its equipment. The machines were expensive to purchase, maintain, and modify. As investors weighed the amount of capital required for future growth, the financial outlook made it difficult to justify continued investment.On the contrary, IC3D does not rely on venture capital, which Cao believes gives it more flexibility to make the model work. He sees opportunities in niche markets such as large-scale commercial outdoor planters, where customization is common and international shipping costs are high. These products are expensive to store and transport, making local on-demand production a more practical alternative.Raub remains optimistic about the future of 3D printed furniture, though he acknowledges that the design industry has been slow to adopt it. He believes larger furniture brands are hesitant to move away from traditional production methods due to risk concerns. However, with growing interest in domestic manufacturing and sustainability, he expects 3D printing to gain more traction over time.This Adirondack and Solis Side Table were designed specifically for the needs of a client looking for outdoor furniture. Image via Model No.3D printing in furnitureAway from Model No., other companies have explored 3D printing in furniture production, applying the technology in different ways to improve efficiency and design flexibility.In 2021, 3D printer manufacturer Flashforge demonstrated how 3D printing can improve furniture design and production efficiency. Working with an undisclosed furniture manufacturer, the company helped integrate 3D printing into the prototyping process, cutting development time from up to ten days to just two or three.Costs dropped as a result, and keeping prototyping in-house provided better control over intellectual property. Flashforges Creator 4 3D printer played a key role in optimizing material use and reducing inefficiencies in production, particularly for plastic components used in outdoor furniture. Over 30 days of continuous printing, the manufacturer saw improvements in accuracy and design flexibility.Elsewhere, US-based experimental design studio Slicelab created the Delicate Density Table, a concrete furniture piece formed using a 3D printed mold. Weighing 86kg and measuring 1525 x 455 x 380mm, the table was designed to explore the structural limits of concrete while maintaining intricate aesthetics.To achieve this, the team used digital simulation and structural optimization to create a detailed yet structurally sound form. The mold was divided into 23 3D printed PLA components, allowing for efficient assembly and controlled surface texture. By filling the mold upside down, air bubbles were confined to the underside, leaving the top smooth. The final table was polished to a mirror-like finish using diamond pad wet sanding.What3D printing trendsshould you watch out for in 2025?How is thefuture of 3D printingshaping up?To stay up to date with the latest 3D printing news, dont forget to subscribe to the 3D Printing Industry newsletter or follow us on Twitter, or like our page on Facebook.While youre here, why not subscribe to our Youtube channel? Featuring discussion, debriefs, video shorts, and webinar replays.Featured image shows the 3-Piece Platform sofa and ottoman in Smoke fabric by Model No. Image via Model No.Ada ShaikhnagWith a background in journalism, Ada has a keen interest in frontier technology and its application in the wider world. Ada reports on aspects of 3D printing ranging from aerospace and automotive to medical and dental.
0 Comentários
·0 Compartilhamentos
·59 Visualizações