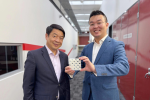
RMITs new ultra-stiff, energy-absorbing lattice for construction and safety applications
3dprintingindustry.com
Researchers at RMIT University have developed a bio-inspired lattice structure (BLS) with 13 times the stiffness and 10% greater energy absorption than existing auxetic materials.Inspired by the deep-sea sponge Venus flower basket, the structure retains auxetic properties over a 60% greater strain range, applications in construction, protective gear, and medical implants.Unlike conventional materials that thin when stretched and expand when compressed, auxetic materials behave in the opposite way. This characteristic has previously been applied in fields such as medical stents, where controlled expansion is essential. However, existing auxetic materials typically suffer from low stiffness and limited energy absorption, restricting their broader use.However, traditional auxetic designs, such as re-entrant honeycomb structures, have historically suffered from low stiffness and limited energy absorption, restricting their practical use. According to Dr. Jiaming Ma, lead author of the study published in Composite Structures, the research addresses this limitation by developing a double-lattice structure that optimizes load distribution and deformation resistance.Professor Mike Xie and Dr. Jiaming Ma hold a 3D printed model of the teams double lattice design. Photo via RMIT University.Enhanced stiffness and energy absorptionTo test the structural performance, the researchers fabricated prototypes using 3D printed thermoplastic polyurethane (TPU). The material was chosen for its flexibility, allowing the team to study the auxetic behavior of the structure under compressive loads.Quasi-static compression tests confirmed that the bio-inspired lattice withstood higher peak stress before structural failure, while maintaining its auxetic behavior over a wider strain range than conventional designs.Finite element analysis (FEA) simulations further demonstrated that the dual-lattice arrangement enhances both stiffness and energy absorption. The 13-fold increase in stiffness and 10% improvement in energy absorption indicate that the structural design itself, rather than the material it is made from, is responsible for these enhancements.This study also examined how variations in lattice geometry influence performance, revealing that increasing the thickness of non-diagonal beams improves stiffness, while expanding the spacing between diagonal beams improves energy absorption.Co-author Dr. Ngoc San Ha highlighted the potential applications of this structural design in seismic-resistant construction, where its high stiffness and energy absorption could reduce the need for steel and concrete while maintaining structural integrity.In addition to construction, the lattice structure could be used for lightweight armor, bulletproof vests, and impact-resistant medical implants, where energy absorption is critical.While the initial prototypes were fabricated using TPU, the next phase of research will focus on scaling up production using steel-based versions. The team is also exploring machine learning algorithms to further optimize the structure for different applications, including programmable materials with tunable mechanical properties.According to the team, the findings suggest that with further refinements auxetic lattice structures could provide more efficient and adaptable solutions for construction, safety, and medical industries.The double lattice structure (left) outperforms the standard re-entrant honeycomb design (right). Photo via RMIT University.RMIT-led materials researchThis research aligns with RMITs broader efforts in materials science and 3D printing, advancing stronger, lighter, and more efficient structures across industries.Last year, the Australian university developed a 3D printed titanium metamaterial that is 50% stronger than the strongest magnesium alloy of similar density used in aerospace applications. Made from Ti-6Al-4V titanium alloy, the hollow-strut lattice (HLS) structure uses a multi-topology design to evenly distribute load stress, reducing weak points and enhancing mechanical strength.The structure was fabricated using powder bed fusion (PBF) additive manufacturing, overcoming previous challenges in manufacturability and stress concentration. Compression tests confirmed the materials improved durability, making it suitable for medical implants, aircraft, and rocket components. With biocompatibility, corrosion resistance, and heat tolerance up to 350C, it holds promise for high-performance applications, with potential for even higher temperature adaptations.Elsewhere, RMIT researchers optimized 3D printed concrete structures by mimicking the helicoidal shell patterns of lobsters, improving durability and load distribution. By adjusting printing patterns using an extrusion-based concrete 3D printer, they achieved greater isotropy, reducing weak interfacial bonds common in traditional layer-stacked concrete.Further reinforcement with 6mm steel fibers (0.75%) enhanced structural integrity, minimized defects, and accelerated hardening, enabling taller and more complex structures. The team planned to expand its research into 3D printed housing, recycled materials, and sound-dampening walls, supported by an Australian Government Innovations Connections grant.What3D printing trendsshould you watch out for in 2025?How is thefuture of 3D printingshaping up?To stay up to date with the latest 3D printing news, dont forget to subscribe to the 3D Printing Industry newsletter or follow us on Twitter, or like our page on Facebook.While youre here, why not subscribe to our Youtube channel? Featuring discussion, debriefs, video shorts, and webinar replays.Featured image shows Professor Mike Xie and Dr. Jiaming Ma hold a 3D printed model of the teams double lattice design. Photo via RMIT University.Ada ShaikhnagWith a background in journalism, Ada has a keen interest in frontier technology and its application in the wider world. Ada reports on aspects of 3D printing ranging from aerospace and automotive to medical and dental.
0 Yorumlar
·0 hisse senetleri
·43 Views