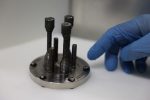
First metal 3D printed part from space returns for testing
3dprintingindustry.com
The first-ever metal 3D printed part produced in space has returned to Earth for testing as part of the European Space Agencys (ESA) Metal3D project focused on manufacturing in microgravity.Created aboard the International Space Station (ISS) using ESAs Metal 3D Printer, the sample has landed at the agencys European Space Research and Technology Centre (ESTEC) in the Netherlands, where it will undergo testing.Developed by Airbus and its partners, this 3D printer was installed in the ISSs Columbus module by ESA astronaut Andreas Mogensen last year. A few months later, in June, it successfully produced its first test print, a curving line shaped like an S.Over the summer, it printed a complete sample, followed by a second in December. Now, the first of these samples is set for analysis at ESTECs Materials and Electrical Components Laboratory, where researchers will compare it with Earth-printed counterparts to better understand how microgravity influences the printing process. The second sample will be studied at the Technical University of Denmark (DTU).The worlds first metal 3D printer for space is on its way to the ISS. Photo via Airbus.Advancing metal 3D printing for space missionsThe project itself has been years in the making. Airbus Defence & Space and AddUp began developing the Metal 3D Printer under an ESA contract in 2016, with the goal of evaluating 3D printing capabilities in sustained microgravity. The system was launched to the ISS aboard NASAs NG-20 mission on January 30, 2024, and operational printing started in mid-2024.While astronauts have been using polymer 3D printers on the ISS since 2014 to produce plastic parts, introducing metal 3D printing could significantly expand manufacturing capabilities for future missions. The ability to produce components on demand could reduce reliance on Earth-based resupply missions, which is particularly important for long-duration space travel to the Moon or Mars.That said, metal 3D printing in space isnt without its challenges. Unlike traditional systems that can take up significant floor space in industrial settings, the ISS 3D printer had to be scaled down to fit within a unit roughly the size of a washing machine.Safety was another major consideration, since metal alloys require extreme temperatures to melt, far higher than plastics, the printer was enclosed in a sealed metal box to prevent any hazards. While plastic 3D printing typically requires temperatures around 200C, metal alloys used in this process melt at over 1,200C, necessitating strict thermal control.The 3D printing process itself also differs from standard Earth-based methods. Rather than using powder-based 3D printing, which could pose containment issues in microgravity, the ISS 3D printer relies on a wire-based approach to minimize risks.With the first space-printed metal samples now back on Earth, researchers at ESA and DTU will examine them closely, running mechanical strength and bending tests alongside microstructural analysis.The goal is to compare these results with identical samples printed under normal gravity conditions to determine the effects of microgravity on the manufacturing process. According to the team, these findings could provide crucial insights for future space missions, where in-orbit manufacturing might one day become a practical necessity.Metal 3D printed part from space. Photo via ESA.3D printing in microgravityAs ESA and its partners study the effects of microgravity on metal 3D printing, other developments in space-based manufacturing are also gaining attention.Recently, researchers at the University of Glasgows James Watt School of Engineering developed a 3D printing system designed for use in microgravity, aiming to overcome challenges in manufacturing structures in space. Led by Dr. Gilles Bailet, the project has received funding from multiple sources and has been tested during ESAs parabolic flight campaign, where it demonstrated reliable material flow using a granular feedstock instead of traditional filaments.The technology could support applications such as space-based solar power, communications infrastructure, and pharmaceutical production. Researchers are also exploring ways to integrate electronics into printed components. Future plans include securing additional funding and conducting an in-space demonstration, with a focus on reducing dependence on Earth-based resupply and addressing concerns about space debris.Space system manufacturer Redwire successfully bioprinted a human knee meniscus in space using its upgraded BioFabrication Facility (BFF) on the IS). The bioprinted meniscus was cultured on the ISS for 14 days in Redwires Advanced Space Experiment Processor (ADSEP) before returning to Earth aboard SpaceXs Crew-6 Mission for further analysis.Conducted as part of the BFF-Meniscus-2 Investigation with the Uniformed Services University of the Health Sciences Center for Biotechnology (4D Bio3), this research aims to advance treatments for meniscal injuries, which are common among U.S. service members. Redwires upgraded BFF offers precise temperature control for bioink printing and features a cell-culturing system to strengthen tissues over time.What3D printing trendsshould you watch out for in 2025?How is thefuture of 3D printingshaping up?To stay up to date with the latest 3D printing news, dont forget to subscribe to the 3D Printing Industry newsletter or follow us on Twitter, or like our page on Facebook.While youre here, why not subscribe to our Youtube channel? Featuring discussion, debriefs, video shorts, and webinar replays.Featured image shows a metal 3D printed part from space. Photo via ESA.
0 Commentaires
·0 Parts
·82 Vue