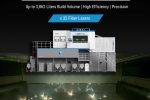
Farsoon Unveils FS1521M-U and Beam Shaping Technology at TCT Asia 2025
3dprintingindustry.com
At TCT Asia 2025, China-based manufacturer Farsoon showcased two significant advancements in industrial metal additive manufacturing: the FS1521M-U and the Beam Shaping Technology. The FS1521M-U now supports up to 32 500W fiber lasers, combined with a 3,862L build volume, aimed at enabling faster, high-quality mass production, reducing material waste and improving economic manufacturing. Meanwhile, the new laser beam shaping technology optimizes laser spot profiles, enabling higher speeds, improved detail, and better part quality.Expanding Large-Scale Metal 3D Printing with the FS1521M SeriesIn 2023, Farsoon introduced the FS1521M series, which features 16 lasers and offers a standard build cylinder of 1530mm 1530mm 850mm (FS1521M) or a high-cylinder build volume of 1530mm 1530mm 1650mm (FS1521M-U). This series was designed for industrial-scale production of large-format metal parts. Since its release, the FS1521M series has been adopted by industrial customers globally, recognized for its design and performance.The updated FS1521M-U offers a build volume of 3,862 liters and supports up to 32 500W fiber lasers, enabling high-speed, high-precision printing while maintaining part quality. The upgraded FS1521M series also features 4 overflow and 4 recycling powder hoppers, supporting up to 4 powder recycling units. Each unit has a processing rate of 90L/h, with a combined maximum processing rate of 360L/h, ensuring more efficient and seamless production. Additionally, the platform offers versatile build volume configurations, either circular or square, to optimize powder usage and reduce costs.Farsoons FS1521M-U. Image via: FarsoonAdvancing Metal Additive Manufacturing with Beam Shaping TechnologyFarsoon is also introduced its Beam Shaping Technology, designed to improve precision, efficiency, versatility and overall performance in metal powder bed fusion systems. This innovation has been integrated into the FS350M-4, a mid-sized production platform featuring quad 1000W lasers and a 433 358 400mm build volume.Beam Shaping Technology enables dynamic laser spot configurations, such as ring-shaped or point-ring patterns, which can be tailored to specific applications. By optimizing laser power distribution and scanning strategies, this technology enhances print quality and efficiency for a range of materials, including stainless steel, aluminum alloys, and titanium alloys, achieving part densities exceeding 99.95%.In addition to improving print quality, Beam Shaping Technology increases printing speeds by widening melt pools by 50100% and boosting build rates by over 2.5 times.It is designed to minimize melt pool spatter, enhance thermal stability, and enable intricate details such as thin-wall structures. The technologys compatibility with high-thermal conductivity materials, including copper alloys, expands its applications across industries such as consumer goods, mold manufacturing, 3C electronics, aerospace, and precision casting.Beam Shaping Technology has been demonstrated across multiple Farsoon metal systems, including the FS721M-H-8-CAMS, FS350M-4, FS273M, and FS191M. Looking ahead, Farsoon plans to extend Beam Shaping Technology to larger platforms, including the FS621M, FS811M, and meter-scale systems, further advancing metal additive manufacturing capabilities.Farsoons Beam Shaping Technology. Image via: FarsoonFarsoons Previous Innovations in Metal Additive ManufacturingIn December, Farsoon introduced the Flight HT601P-4, a large-format polymer powder bed fusion (PBF) system featuring four 300-watt fiber lasers. The new system offers a substantial build volume of 600 600 600 mm (216 liters), enabling the efficient production of large components or high-volume batches.Fiber lasers in the Flight HT601P-4 achieve scanning speeds of up to 20 meters per second, significantly boosting productivity and operational efficiency. Its interchangeable build cartridge design supports continuous production workflows, minimizing downtime and maximizing throughput. Additionally, the compact footprint allows for optimized factory layouts, enhancing production yield within limited floor spaces.In November, Farsoon introduced the FS191M, a next-generation metal powder bed fusion (PBF) machine designed to enhance productivity and cost-efficiency across a range of industrial uses. Building upon the foundation of its FS121M system launched in 2016, the new system aims to offer a scalable solution for both pilot projects and low-volume manufacturing.Who won the 2024 3D Printing Industry Awards?Subscribe to the 3D Printing Industry newsletter to keep up with the latest 3D printing news.You can also follow us on LinkedIn, and subscribe to the 3D Printing Industry Youtube channel to access more exclusive content.Featured image showsFarsoons FS1521M-U. Image via: FarsoonPaloma DuranPaloma Duran holds a BA in International Relations and an MA in Journalism. Specializing in writing, podcasting, and content and event creation, she works across politics, energy, mining, and technology. With a passion for global trends, Paloma is particularly interested in the impact of technology like 3D printing on shaping our future.
0 Комментарии
·0 Поделились
·45 Просмотры