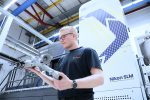
3DPRINTINGINDUSTRY.COM
Bosch new 6M metal AM facility to boost its automotive production
German multinational engineering and technology company Bosch has launched a new metal additive manufacturing facility at its Nuremberg plant, investing nearly 6 million.At the heart of the facility is a Nikon SLM Solutions NXG XII 600 metal 3D printer, which the company says will play a key role in producing complex metal parts more efficiently. With this addition, the automotive giant sees itself as the first Tier-1 automotive supplier in Europe to operate a facility in this performance class.The new setup is part of Boschs ongoing effort to strengthen its manufacturing capabilities in Germany. At full capacity, the new facility can manufacture up to 10,000 kilograms of metal parts annually, with production speeds reaching 1,000 cm/h.According to Technical Plant Manager Jrg Luntz, the main goal is to reduce time-to-market by moving faster than traditional manufacturing methods allow. Even today, only a few companies can produce technology on an industrial scale the way Bosch does. Were now going one step further, taking volume production in metal 3D printing to the automotive level.3D printed steering gear box. Photo via Bosch.Flexible production and faster turnaround timesOne of the benefits of the new system is its flexibility. The printer can produce unfinished parts directly from digital files, eliminating the need for tooling. It also minimizes raw material waste, which Weichsel pointed out contributes to more sustainable production practices. In addition, the setup allows Bosch to adapt quickly to changes in batch size while keeping the entire process in-house.The machine is capable of producing a wide range of parts, from components used in hydrogen applications and electric vehicle motor housings to e-axle parts and engine blocks for racing. Using twelve lasers, the printer fuses metal powder layer by layer according to computer-aided design files.Compared to earlier systems, it operates up to five times faster and can handle geometries that would be challenging, or even impossible, with traditional milling. For example, the ability to print curved or internal channels offers clear advantages for complex component design.Bosch remains committed to Germany as an industrial location and is investing large sums of money here. By introducing new technologies in our plants, we are securing considerable sales potential, said Klaus Mder, member of the Bosch Mobility sector board responsible for operations.A case in point is engine block manufacturing. Traditionally, this process can stretch over three years, with mold-making alone requiring up to 18 months. With 3D printing, Bosch can bypass that step entirely. The design data goes straight to the machine, and a finished engine block can be produced in just a few days, a shift that significantly shortens the development timeline.At the plant level, expectations are high. Alexander Weichsel, Commercial Plant Manager in Nuremberg, noted that the facility is designed to make metal part production both faster and more productive, factors he believes will enhance Boschs competitiveness.Beyond automotive, the company also sees opportunities in areas such as energy and aviation.New Nikon SLM Solutions NXG XII 600 3D printer at Nuremberg plant. Photo via Bosch.Metal AM advantage in automotive sectorMetal 3D printing is increasingly being used in automotive production to streamline workflows, reduce costs, and enable complex part designs not possible with traditional methods.Earlier this month it was announced that Japanese automotive manufacturer Honda is exploring how laser powder bed fusion (LPBF) 3D printing could enhance manufacturing across its automotive, motorsports, aerospace, and wheelchair racing divisions. The company highlighted benefits such as faster production, lower costs, and shorter lead times.According to the company, metal 3D printing is already part of its workflow, with LPBF systems from Nikon SLM Solutions used to create complex components like pistons and turbine housings for Oracle Red Bull Racings F1 cars, as well as lightweight, custom-fit aluminum handlebars for racing wheelchairs. Simulation tools and real-time monitoring further improved part accuracy and overall manufacturing precision.Back in 2023, Europes largest carmaker Volkswagen Group acquired a second MetalFAB 3D printer from Netherlands-based Additive Industries to expand its metal additive manufacturing capabilities. The company cited the systems automation, modularity, and efficiency-enhancing tools as key factors in the decision.Its first MetalFAB unit had already contributed to significant cost and lead time reductions. Back in 2018, Volkswagen opened a dedicated 3D printing center, and more recently, partnered with HP and Siemens to further scale production. At its Wolfsburg plant, the company aimed to manufacture up to 100,000 3D printed automotive components annually by 2025.What3D printing trendsshould you watch out for in 2025?How is thefuture of 3D printingshaping up?To stay up to date with the latest 3D printing news, dont forget to subscribe to the 3D Printing Industry newsletter or follow us on Twitter, or like our page on Facebook.While youre here, why not subscribe to our Youtube channel? Featuring discussion, debriefs, video shorts, and webinar replays.Featured image shows 3D printed steering gear box. Photo via Bosch.Ada ShaikhnagWith a background in journalism, Ada has a keen interest in frontier technology and its application in the wider world. Ada reports on aspects of 3D printing ranging from aerospace and automotive to medical and dental.
0 Comments
0 Shares