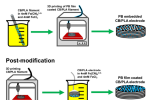
Brightons latest research on glucose biosensor using Prussian Blue filament
3dprintingindustry.com
Researchers from the University of Brighton have developed a 3D printed glucose biosensor that can monitor glucose consumption in HepG2 cells.Led by Chloe Miller, alongside Bhavik Anil Patel, Professor of Clinical and Bioanalytical Chemistry, this study employed a method in which Prussian Blue was embedded directly into carbon black/polylactic acid (CB/PLA) filaments before 3D printing. Leveraging FlashForge Creator Pro 3D printer, the method offers a potential workaround to common issues with chemically modified electrodes, especially when it comes to stability and reproducibility.Electrochemical sensors depend heavily on the surface of electrodes, where reactions take place. Thats why surface modifications, such as improving conductivity or enhancing selectivity are often essential.Typically, this involves depositing materials like nanoparticles or enzymes after the electrodes are printed. But those post-printing steps are often complex, time-consuming, and prone to long-term degradation. Published in ACS Publications, the Brighton team instead set out to integrate the active material at an earlier stage.Schematic diagrams showing the processes taken to pre- and post-modify CB/PLA electrodes with PB. Image via University of Brighton.Direct electrodeposition improves material control and printabilityAs per the team, Fused Filament Fabrication (FFF) has become a go-to 3D printing technique for sensor fabrication because its affordable, customizable, and easy to work with. Still, theres a catch: the conductive materials available off the shelf are limited, which leaves many researchers resorting to in-house modifications.Some previous attempts, for example, involved embedding compounds like Ni(OH) and graphene into PLA filaments. Others tried to create Prussian Blue on filaments using leftover iron. But these approaches often fall short when it comes to consistency or accessibility.To avoid that, the team directly electrodeposited Prussian Blue onto commercial CB/PLA filaments. Prussian Blue, known for its electrocatalytic behavior in detecting hydrogen peroxide (HO), was deposited using cyclic voltammetry.The researchers tested different numbers of deposition cycles to find the optimal point. Up to 200 cycles, the surface coating improved without causing any problems. But once they hit 250 cycles or more, the filament became too thickly coated to pass through the 3D printers extruder.Surface analysis with scanning electron microscopy (SEM) and energy dispersive X-ray (EDX) spectroscopy confirmed successful deposition and iron distribution on the filament. At 200 cycles, the coating developed cracks that exposed the PLA base, improving material mixing during extrusion.Electrodes printed from these filaments contained well-distributed Prussian Blue, although only about 5.2% of the embedded material remained electrochemically accessible.Evaluating performance across electrode types and designsTo see how well these embedded electrodes performed, the researchers compared embedded electrodes with post-printing Prussian Blue films, finding both showed surface-controlled behavior but differed notably in sensitivity and stability.The film electrodes initially had a lower detection limit for HO (1.4 M) compared to embedded ones (22.4 M). Long-term stability tests revealed that film electrodes lost 80% of their current response after 30 days, while embedded electrodes retained over 60%, indicating superior durability.Geometry also turned out to matter. The team printed electrodes with flat, dome, and square grid surfaces to evaluate how design affects performance. Interestingly, while flat surfaces gave the highest response in standard tests, the square grid performed best in real-time HO detection, likely due to better exposure of embedded Prussian Blue at the edges.With that in mind, they used the square grid design to build a glucose biosensor. After modifying the surface with glucose oxidase, bovine serum albumin, and glutaraldehyde, they inserted the sensor into a 3D printed well plate.They then tested its ability to track glucose levels in a cell culture setup. When the sensor was placed in media with HepG2 cells for 24 hours, it successfully measured a drop in glucose concentration compared to a control sample, proving it could monitor cellular metabolism in vitro.According to the researchers, this study demonstrates a novel approach to glucose biosensor fabrication by embedding Prussian Blue directly into 3D printing filaments. By successfully monitoring glucose consumption in cell cultures, the study showcases the potential of this approach for reliable, real-time biochemical sensing in biomedical applications.Light microscopy images of flat, dome, and square grid CB/PLA electrodes. Image via University of Brighton.Novel developments in 3D printed biosensorsAway from Brighton, previous research also explored novel approaches to advance 3D printed biosensor development.In December 2018, Washington State University (WSU) researchers used 3D printing to create a needle-free glucose monitoring device for people with diabetes. Produced via direct ink writing (DIW), the thumbnail-sized biosensor was made from layered carbon and enzyme inks, where the carbon ink served as the electrode and the enzyme layer absorbed glucose.Adhering to the skin and measuring glucose in sweat, the device was designed as a less invasive alternative to finger pricking. It showed improved sensitivity, material efficiency, and long-term stability over screen-printed versions, highlighting DIWs potential for affordable, personalized biosensors.Elsewhere, researchers from Sungkyunkwan University used a commercially available inkjet printhead to develop personalized wearable biosensors for health monitoring. Using 3D printed sugar scaffolds filled with flexible silicone elastomer, the team created lightweight, conductive sensors that conformed to patient body shapes.These devices captured both active strain and passive signals like EMG, EDA, and EEG with high sensitivity during sleep and treadmill tests, leading the team to pursue broader personalized diagnostic applications.What3D printing trendsshould you watch out for in 2025?How is thefuture of 3D printingshaping up?To stay up to date with the latest 3D printing news, dont forget to subscribe to the 3D Printing Industry newsletter or follow us on Twitter, or like our page on Facebook.While youre here, why not subscribe to our Youtube channel? Featuring discussion, debriefs, video shorts, and webinar replays.Featured image shows schematic diagrams showing the processes taken to pre- and post-modify CB/PLA electrodes with PB. Image via University of Brighton.Ada ShaikhnagWith a background in journalism, Ada has a keen interest in frontier technology and its application in the wider world. Ada reports on aspects of 3D printing ranging from aerospace and automotive to medical and dental.
0 Commentaires
·0 Parts
·88 Vue