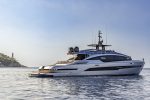
Pershing GTX116 Yacht Employs Caracols Robotic 3D Printing for Superstructure Components
3dprintingindustry.com
Pershing, an Italian brand under luxury yacht manufacturer Ferretti Group, has integrated large-format additive manufacturing (LFAM) into its latest sport utility yacht, the GTX116. Developed in collaboration with Caracol, the project showcases how 3D printing is reshaping the yacht industry by replacing traditional fiberglass molding with robotic extrusion systems.Pershing, an Italian brand under luxury yacht manufacturer Ferretti Group, has integrated large-format additive manufacturing (LFAM) into its latest sport utility yacht, the GTX116. Developed in collaboration with Caracol, the project showcases how 3D printing is reshaping yacht production by replacing traditional fiberglass molding with robotic extrusion systems.The yachts side air intake grilles and visor above the windshield were fabricated using Caracols Heron AM platform. This marks a significant milestone in the adoption of additive manufacturing for high-end marine applications, where performance, customization, and aesthetic value are paramount.3D printed intake grilles.Photo via Caracol.The additive manufacturing process and its benefits for Pershing GTX116 air grillesManufactured at Caracols facility using their Heron 300 system, the air grilles span 4.2 meters in length and were printed using ASA (Acrylonitrile Styrene Acrylate) reinforced with 20% glass fiber (GF), a material selected for its strength and resistance to marine environments. The printing process, completed in 72 hours, resulted in a 40 kg component measuring 420t0 x 400 x 400 mm, that was later finished with a gel coat for durability and visual appeal.This shift from traditional fiberglass lamination to robotic additive manufacturing offers numerous advantages. Yacht grilles and other custom superstructures typically require mold production, intensive manual labor, and long lead times. Caracols LFAM approach eliminates the need for tooling, enabling direct-from-CAD production, reducing steps, and enhancing design freedom.According to Ferretti Group, the new approach led to a 50% reduction in lead time, 60% reduction in material waste, and a 15% lighter component. These improvements align with the industrys growing focus on sustainability, cost-effectiveness, and performance.Founded in Milan in 2017, Caracol has developed an integrated LFAM platform that combines a proprietary extrusion head, robotic motion systems, and its in-house Eidos Manufacturing software. The company operates Europes largest LFAM center and has recently expanded to the U.S. and Dubai, with applications in aerospace, marine, energy, and architecture. Its most recent addition, the Vipra AM platform, brings LFAM to metal applications, targeting high-performance components in industries such as construction, aerospace, and shipbuilding.Intake grilles with the Heron 300 System. Photo via Caracol.3D Printing for marine applicationsA notable example is the companys recent collaboration with V2 Group, producing a 6-meter-long 3D printed catamaran. This catamaran was developed with a focus not only on producing a single vessel but also on examining how the manufacturing process could be refined for broader application. The results demonstrated the potential of large-format additive manufacturing to reduce material waste and allow for complex, customizable designs. Both companies plan to continue advancing this method of production, working toward a model that could be commercially viable in the marine industry.Other companies are also advancing similar initiatives- Dutch start-up Tanaruz Boats uses recycled polypropylene reinforced with 30% glass fiber to produce customizable leisure boats ranging from 4.5 to 10 meters. The company aims to scale production while maintaining a circular manufacturing modelIn the U.S., the University of Maine (UMaine) made headlines in 2022 after 3D printing two large vessels for the U.S. Marine Corps. Produced at UMaines Advanced Structures and Composites Center, the boats were designed as logistical support vessels capable of carrying supplies and personnel. The larger vessel can transport two 20-foot shipping containers, while the smaller one can accommodate an entire rifle squad with three days worth of provisions. This project highlights how additive manufacturing can be used to accelerate production, reduce costs, and deliver mission-specific performance at scale.Featured image shows the Pershing GTX116 yacht. Photo via Caracol.Who won the 2024 3D Printing Industry Awards?Subscribe to the 3D Printing Industry newsletter to keep up with the latest 3D printing news.You can also follow us on LinkedIn and subscribe to the 3D Printing Industry Youtube channel to access more exclusive content.
0 Comentários
·0 Compartilhamentos
·51 Visualizações