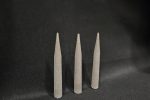
Next-Generation Tungsten Manufacturing: HAMR Industries and Freemelt AB Present 3D Printed Penetrator Rounds
3dprintingindustry.com
At MILAM 2025, HAMR Industries, a provider of advanced scientific research and engineering solutions, and Swedish 3D printer manufacturer Freemelt AB showcased their latest advancements in tungsten additive manufacturing. Among the exhibits were metal 3D printed penetrator rounds, produced using the Freemelt One Electron Beam Powder Bed Fusion (EB-PBF) system at Neighborhood 91, the worlds first end-to-end additive manufacturing (AM) production campus.These precision-engineered rounds are designed for high-velocity impact applications, with the goal of advancing propulsion systems, thermal protection components, and customized kinetics. They are specifically engineered to meet the high-performance demands of military, aerospace, and energy applications. According to Michael Schmitt, CEO and Senior Research Scientist at HAMR Industries, the same tungsten printing process can also be applied to industries such as rocket nozzles for space exploration, spacecraft thermal protection systems, and fusion power components, where tungstens exceptional density and thermal resistance are essential for extreme conditions.The reason for creating these advanced rounds is to push the limits of existing tungsten manufacturing methods. Compared to traditional techniques, EB-PBF technology enables the production of highly complex geometries that are optimized for enhanced performance, material efficiency, and customization.3D printed penetrator rounds, produced using the Freemelt One Electron Beam Powder Bed Fusion (EB-PBF) system. Photo via HAMR Industries.Tungstens Role in 3D PrintingTungsten, one of Freemelts core materials alongside titanium and copper, is known for its extremely high melting point of 3,422C, making it ideal for high-temperature applications. It has also become increasingly appealing due to its exceptional ability to maintain strength and stiffness even at elevated temperatures. However, Tungstens brittleness at lower temperatures (below 300600C), along with its high melting point and poor machinability, presents challenges in traditional manufacturing methods.These difficulties have driven increased interest in additive manufacturing (AM) for tungsten. While laser beam powder bed fusion (LB-PBF) has seen limited success due to its lower process temperatures (around 200C), electron beam powder bed fusion (EB-PBF) provides a more effective alternative. By operating in a vacuum and sustaining temperatures above 1,000C, EB-PBFs inertia-free beam deflection achieves speeds of several kilometers per second. This enables efficient melting of highly crack-prone materials while maintaining their chemical purity.Research and Innovations in Tungsten 3D PrintingRecognizing its potential, Freemelt has been advancing its industrial EB-PBF system, eMelt, to optimize tungsten 3D printing. The company is exploring various techniques, including spot melting, enabled by its proprietary Pixelmelt software. Spot melting allows for greater utilization of beam power, which could improve production efficiency.A key feature of Freemelts electron beam source is its diode-type system with a laser-heated cathode, which maintains consistent beam spot quality across the 06 kW power range. Other systems may experience variation in spot quality when operating above 2 kW. Freemelts beam source configuration also enables the EB-PBF process to maintain high power throughout preheating, thermal management, and meltinga capability unmatched in the field.Freemelts ProHeat electron beam powder bed fusion preheating technology in progress. Photo via Freemelt.Freemelts Past InnovationsIn 2023, Freemelt launched the eMELT-iD, a model designed to simplify product and application development while preparing components for large-scale production. Featuring integration with the eMELT-iM, the eMELT-iD enables a smooth transition from development to serial production. Built on the core technology of the eMELT-iM, it offers a unique approach to the development and scaling of industrial machines. This innovation seeks to reduce both time and costs for customers looking to develop new applications for mass production using 3D printing technologies.In 2024, Freemelt also secured patents for a post-processing method to remove excess powder from 3D printed parts. This method, designed for finishing powder bed fusion prints, involves filling parts with saline water, freezing them to break links between powder grains in internal channels, and easing the removal of excess powder.Who won the 2024 3D Printing Industry Awards?Subscribe to the 3D Printing Industry newsletter to keep up with the latest 3D printing news.You can also follow us on LinkedIn, and subscribe to the 3D Printing Industry Youtube channel to access more exclusive content.Featured image shows3D printed penetrator rounds, produced using the Freemelt One Electron Beam Powder Bed Fusion (EB-PBF) system. Photo via HAMR Industries.Paloma DuranPaloma Duran holds a BA in International Relations and an MA in Journalism. Specializing in writing, podcasting, and content and event creation, she works across politics, energy, mining, and technology. With a passion for global trends, Paloma is particularly interested in the impact of technology like 3D printing on shaping our future.
0 Comentários
·0 Compartilhamentos
·79 Visualizações