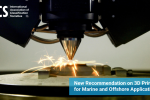
3DPRINTINGINDUSTRY.COM
New IACS guideline formalizes 3D printing standards for marine parts
The International Association of Classification Societies (IACS), a technical standards organization covering over 90% of the worlds cargo-carrying fleet, has published a new recommendation aimed at guiding the use of 3D printing in the maritime and offshore sectors. Recommendation 186 sets out a standardized framework for qualifying, approving, and certifying metallic parts produced using additive manufacturing (AM).IACS new recommendation responds to growing industry interest in deploying AM to replace or complement traditional manufacturing techniques such as casting, forging, and welding. In marine and offshore contextswhere operational uptime, safety, and sustainability are critical3D printing offers potential advantages such as reduced material waste, faster part production, and increased design flexibility. Rec.186 defines clear criteria for integrating AM into existing regulatory structures by aligning with standards such as ISO/ASTM 52900 and AWS D20.1, and incorporating IACS Unified Requirements for welding and materials, known as UR W.Rec.186 outlines specific technical guidance for three 3D printing methods: Powder Bed Fusion (PBF), Directed Energy Deposition (DED), and Binder Jetting (BJT). For each, the document defines process parameters and inspection protocols to ensure consistent part quality. It introduces a three-tier testing regimeAM Levels 1 through 3based on application criticality. Components used in safety-critical systems, such as propulsion or structural assemblies, fall under higher testing levels and are subject to more rigorous qualification procedures. Feedstocks, including metal powders, wires, and binders, must meet documented quality control measures, with added provisions for recycling protocols and material traceability.Laser-based additive manufacturing process in IACS qualification guidelines for 3D printed marine components. Photo via IACS.Design qualification is addressed through a series of requirements focused on topology optimization, simulation-based pre-build verification, and performance validation. Rec.186 also mandates post-processing standards and non-destructive testing (NDT) procedures suited to the unique material properties of AM parts. Techniques such as computed tomography (CT) scanning are recommended to detect internal flaws like porosity or incomplete fusion, which can compromise component integrity under mechanical stress or corrosion exposure. These inspection methods are calibrated to account for anisotropic behavior, which is common in layer-wise fabrication.Materials and welding expert of IACS Alexandre Astruc emphasized the importance of establishing trust in AM technologies. Additive manufacturing, or 3D printing, is increasingly becoming a valuable tool for the marine sector, offering a flexible, speedy and customizable solution for environments where the consequences for safety, sustainability or operational uptime can otherwise be significant, he said. While its potential for rapid production is notable, its true strength lies in its ability to provide innovative, on-demand solutions tailored to complex maritime challenges. In developing Rec 186, IACS is seeking to safeguard the benefits offered by additive manufacturing by ensuring it is underpinned by a standardized framework for verification and certification that gives confidence to all parties.Future applications of Rec.186 may include class-certified parts for onboard systems, repair components produced at sea, and localized manufacturing near shipyards. IACS has indicated that ongoing collaboration with shipbuilders, original equipment manufacturers (OEMs), and marine operators will be central to the continued evolution of the framework. Rec.186 marks a shift from experimentation to formal adoption of additive manufacturing across regulated marine engineering domains.New pressure vessel validation and construction standards in AMFronius International, an Austrian welding specialist, recently collaborated with Linde Engineering, MIGAL.CO, and TV SD Industrie Service to qualify additively manufactured pressure vessel components under a draft standard developed by the German Institute for Standardization (DIN). The project produced a component featuring a 3D printed aluminum pipe branch welded onto a conventionally manufactured base pipe. The team employed Fronius Cold Metal Transfer (CMT) process and implemented real-time sensor adjustments and parameter monitoring to minimize geometric deviations. Multiple layers of validation were applied, including destructive and non-destructive testing, metallographic analysis, and pressure assessments. The final components met the requirements of the European Pressure Equipment Directive 2014/68/EU, confirming the feasibility of AM for regulated pressure-bearing equipment.In 2023 on a separate development, the ISO published ISO/ASTM 52939:2023, a standard defining quality assurance protocols for 3D printing in the construction sector. Developed through coordination between ISOs Technical Committee 261 and ASTM Internationals Committee F42, the standard outlines requirements for structural and infrastructure elements produced via additive manufacturing. It applies across materials and technologies, excluding metals, and mandates that all relevant steps in the additive construction process be overseen by locally certified engineers. While the standard does not address environmental or safety aspects of the facility, nor design or material characterization, it establishes a baseline for process control and approval that reflects the growing need for standardized qualification principles in emerging AM applications.Additive manufacturing build-up of the pipe branch with weld layers. Image via Fronius.Ready to discover who won the 20243D Printing Industry Awards?Subscribe to the 3D Printing Industry newsletter to stay updated with the latest news and insights.Featured image shows Laser-based additive manufacturing process in IACS qualification guidelines for 3D printed marine components. Photo via IACS.
0 Comments
0 Shares