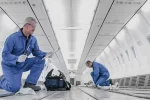
Materialise EN 9100 Certification for Metal 3D Printing in Aerospace
3dprintingindustry.com
Materialise, a Belgium-based additive manufacturing company, has secured EN 9100 certification for its metal 3D printing operations. The designation, which builds on ISO 9001, confirms that the company meets rigorous quality management standards specific to the aerospace industry, including traceability, process control, and regulatory compliance. The certification enables Materialise to expand its role in aviation and space supply chains by offering certified metal components produced through additive processes.Before this development, Materialise had already achieved EN 9100 certification for its polymer 3D printing activities, producing more than 500,000 functional parts currently in service on aircraft. These include components for original equipment manufacturers (OEMs), tier suppliers, and maintenance, repair, and overhaul (MRO) operations. The addition of certified metal capabilities allows the company to address new part categories with structural or durability requirements and respond more flexibly to industry demands.Beyond EN 9100, Materialise holds a Production Organization Approval (POA) from the European Union Aviation Safety Agency (EASA), permitting it to manufacture flight-ready components with Form 1 accreditation. It is also one of a limited number of additive manufacturing providers certified to Airbus AIPI standards, having recently received the highest possible grade on the Airbus Quality Maturity assessment. These credentials position the company to support a range of aviation stakeholders in identifying and qualifying parts suitable for polymer or metal 3D printing.Erik de Zeeuw, Market Manager for Aerospace at Materialise, said: Low-criticality parts that need to be light, strong, and durable, such as seat bezels, housings, interior trims, or ducts, are particularly strong candidates. They often need to be repaired or replaced, but in small quantities. These are requirements that align perfectly with key benefits of metal 3D printing, including the ability to have digital on-demand stock for faster, more reliable sourcing, and cost-efficient production of small series parts.Materialise expands its aerospace portfolio with EN 9100 certification for metal 3D printing. Image via Materialise.The additive process eliminates tooling and associated setup costs, making small-batch production economically viable compared to conventional manufacturing. There is no requirement for minimum order quantities, which reduces the risk of holding excess inventory. This is a significant factor in aerospace, where parts are often needed in limited runs.Paying only for parts used, and with a lower TCO, is clearly beneficial, de Zeeuw said. As is avoiding any potential supply chain disruptions that could delay part availability, which in turn can end up grounding flights for long periods of time. Whats more, it becomes less cost-prohibitive to review and adapt parts for continuous improvement.Certification benchmarks across AM sectorsAerospace-focused additive manufacturing companies have increasingly sought quality management certifications to meet sector-specific requirements. A3D Manufacturing, a US-based manufacturing-as-a-service provider, recently earned AS9100 certification from the International Aerospace Quality Group (IAQC). This approval confirms that A3Ds 3D printed components and processes meet the high precision, environmental tolerance, and safety standards demanded by aerospace applications. The AS9100 standard is often a prerequisite for doing business with large aerospace manufacturers. Similar certifications have been granted to other additive firms including Additive Flight Solutions and Keselowski Advanced Manufacturing, which qualified both their additive and CNC operations for aerospace and defense production in under six months.In construction 3D printing, quality and safety standards have also become more formalized. ISO/ASTM 52939:2023, published in December 2023, sets out qualification principles for structural and infrastructure elements in additive construction. Developed jointly by ISOs Additive Manufacturing Technical Committee and ASTMs F42 committee, the standard outlines requirements for process control, quality-relevant characteristics, and risk mitigation. It mandates that certified engineers oversee specific production steps to ensure structural integrity. Although the new guidelines do not apply to metals or address environmental and safety issues, they provide a framework for certifying non-metallic 3D printed elements used in residential and commercial infrastructure.ASTM International Logo. Image via ASTM International.Ready to discover who won the 20243D Printing Industry Awards?Subscribe to the 3D Printing Industry newsletter to stay updated with the latest news and insights.Featured image shows Materialise expands its aerospace portfolio with EN 9100 certification for metal 3D printing. Image via Materialise.Anyer Tenorio LaraAnyer Tenorio Lara is an emerging tech journalist passionate about uncovering the latest advances in technology and innovation. With a sharp eye for detail and a talent for storytelling, Anyer has quickly made a name for himself in the tech community. Anyer's articles aim to make complex subjects accessible and engaging for a broad audience. In addition to his writing, Anyer enjoys participating in industry events and discussions, eager to learn and share knowledge in the dynamic world of technology.
0 Comments
·0 Shares
·25 Views