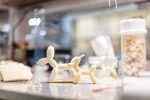
3DPRINTINGINDUSTRY.COM
Unique 3D Printed Foam Gets a Boost with Catalyst-Free Bonding
Researchers from the University of Texas at Dallas (UT Dallas) have introduced a fresh approach to 3D printing polymer foams that can achieve a broader range of mechanical properties and expansion capabilities.Having used catalyst-free dynamic covalent chemistry (DCC), their method embeds dynamic phosphodiester bonds within polymers containing foaming agent microspheres. These bonds can exchange during thermal foaming, allowing the materials to expand more effectively without sacrificing structural integrity.Published in RSC Applied Polymers, this research was co-led by chemistry doctoral students Ariel Tolfree, and Rebecca Johnson under the supervision of Dr. Ron Smaldone, Associate Professor of chemistry and biochemistry in the School of Natural Sciences and Mathematics and who is also the corresponding author of the study.This is probably the longest project Ive ever done, said Johnson, who plans to complete her PhD in chemistry in May. From start to finish, it was a little over two years. A lot of it was trying to get the polymer formulation correct to be compatible with the 3D printer.Tiny dog-shaped pieces of sturdy, lightweight 3D printed foam. Photo via UT Dallas.Overcoming structural limitations with dynamic bondingPolymer foams are valued for their lightweight structure, insulation, and mechanical properties, but balancing pore size, density, and strength remains challenging. Conventional methods using gas injection often face trade-offs. Moreover, higher crosslinking density enhances toughness but limits expansion, while larger pores reduce density and mechanical strength.The researchers addressed this issue using DCC, which allows bonds to rearrange under specific conditions. Unlike conventional polymers with fixed bonds, these adaptable networks enhance performance and recyclability. Therefore, they focused on phosphodiester bonds for their chemical stability and ability to exchange at temperatures as low as 50C without harmful or costly catalysts.Foaming microspheres were embedded within a polymer matrix containing varying concentrations of dynamic and non-dynamic crosslinkers. When these printed parts were heated at 165C for 15 minutes, the foaming process began. As the thermoplastic shell of the microspheres softened, the liquid hydrocarbon inside vaporized and expanded. Cooling then hardened the shells, forming a closed-cell foam.Were certainly not the only ones trying to do this, Smaldone said. The novelty is using dynamic chemistry to print really great foam material. The next question to address will be, how do we tune the properties and use this new kind of knowledge to fit a variety of different needs?Comparative testing and recyclability resultsIn testing, researchers compared non-dynamic tetraethylene glycol diacrylate (TEGDA) crosslinkers with dynamic Bis[2-(methacryloyloxy)ethyl] Phosphate (DPE) crosslinkers and found that dynamic crosslinkers consistently achieved greater expansion. The foaming process involved direct phosphodiester exchanges, rearrangements forming triester and monoester products, and interactions with ester groups, mechanisms that enhanced network reorganization and expansion.To ensure the bond exchanges were working as intended, researchers used Fourier transform infrared spectroscopy (FTIR), which confirmed dynamic bond exchange through transesterification and condensation mechanisms. Differential scanning calorimetry (DSC) showed higher crosslinker content raised glass transition temperatures, indicating improved network uniformity.When put to the test, unfoamed dynamic polymers demonstrated higher compressive strengths, ranging from 180 to 216 MPa, compared to the 130 to 150 MPa recorded for non-dynamic polymers. After foaming, the dynamic polymers demonstrated better energy dissipation and compressive strength than non-dynamic foams with similar expansion.Theres more. The team also tested the foams recyclability by compressing unfoamed cylinders to 70% of their height and allowing them to recover before foaming. Dynamic phosphodiester polymers retained their mechanical properties better than non-dynamic TEGDA foams, indicating effective damage repair through bond rearrangement and condensation reactions.Ultimately, the study suggests that dynamic phosphodiester bonds provide a promising route to achieving higher foam expansion, improved mechanical strength, and energy dissipation without the need for catalysts. Its a method that could extend the lifespan of 3D printed foams and open up broader applications for these materials.3D printing with foamAway from UT Dallas, contributions in foam 3D printing also came from Nano Dimension-acquired Desktop Metal, which launched FreeFoam, a 3D printable photopolymer resin developed by its subsidiary Adaptive3D.Introduced at Foam Expo North America in June 2022, FreeFoam enables customizable foam parts to expand up to seven times their original size when heated between 160 170C. Available on the ETEC Xtreme 8K DLP 3D printer, it allows for reduced waste, enhanced design flexibility, and improved shipping efficiency across sectors like automotive, furniture, footwear, and healthcare.Elsewhere, UC San Diegos Department of NanoEngineering researchers developed an expandable foaming resin compatible with SLA 3D printers. Designed for heat-induced expansion post-UV-curing, the resin enabled the creation of parts up to 4000% larger than the printers build volume.The study aimed to overcome geometric limitations in manufacturing, with potential applications in aerospace, architecture, energy, and biomedicine. Testing involved heating 3D printed HEMA resin models at 200C for up to ten minutes, achieving significant expansion and suggesting uses in lightweight components like aerofoils and buoyancy aids.What3D printing trendsshould you watch out for in 2025?How is thefuture of 3D printingshaping up?To stay up to date with the latest 3D printing news, dont forget to subscribe to the 3D Printing Industry newsletter or follow us on Twitter, or like our page on Facebook.While youre here, why not subscribe to our Youtube channel? Featuring discussion, debriefs, video shorts, and webinar replays.Featured image shows tiny dog-shaped pieces of sturdy, lightweight 3D printed foam. Photo via UT Dallas.
0 Comentários
0 Compartilhamentos
27 Visualizações