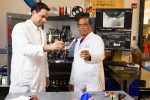
3DPRINTINGINDUSTRY.COM
NASA grants $5M to FAMU-FSU for in-space manufacturing research
Researchers at the Florida A&M University-Florida State University (FAMU-FSU) College of Engineering have received a $5 million NASA grant to develop composite materials and manufacturing systems for future space missions.Administered by FAMU, the project involves collaboration with faculty members from FSU, the Goddard Space Flight Center, and FAMU. Led by Professor Subramanian Ramakrishnan from the Department of Chemical and Biomedical Engineering, the team featuring Richard Liang, Emily Pritchard, Satyanarayan Dev, and Margaret Samuels, is working on single-step systems that integrate sensing materials and electrodes to improve manufacturing efficiency and device quality.Imagine while on a space mission having the ability to print sensors, radiation shields or even functional tissues as the mission progresses, said Professor Subramanian Ramakrishnan from the Department of Chemical and Biomedical Engineering. This capability could change the space exploration paradigm, making missions more sustainable and adaptable to unforeseen challenges.Jamel Ali, Ph.D., (L) and Subramanian Ramakrishnan, Ph.D., pose with the nScrypt 3D printer at the High-Performance Materials Institute (HPMI) of the Materials Research Building (MRB) at FAMU-FSU College of Engineering in Tallahassee, Florida. Photo via FSU.Novel inks and printing techniques for space missionsFor this research, the team is working with a range of materials, including 2D materials known as MXenes, along with metallic and semiconducting nanoparticles. These inks are designed to be 3D printed into various components, from sensors and antennas to radiation shielding and flexible electronic circuits. The goal is to make it possible for astronauts to manufacture what they need as they go, without relying entirely on supplies sent from Earth.Theyre also exploring how to make use of materials found on other planets. By turning lunar and Martian soil, or regolith, into inks for 3D printing, the researchers hope to create functional structures directly on Mars or the Moon, reducing dependence on Earth-based resources and making long-term missions more sustainable.Part of their work involves refining a technique called electrohydrodynamic (EHD) printing, which uses electric fields to precisely print nanoparticles. Combined with laser curing, the process is intended to speed up manufacturing, particularly for tasks aboard the International Space Station (ISS) where efficiency is critical.Beyond the NASA grant, Ramakrishnan is leading a separate project funded by a $700,000 grant from the National Science Foundation (NSF). This project focuses on expanding 3D printing capabilities through the acquisition of an nScrypt 6-axis 3D printing system at FAMU. The system is designed to produce complex structures on curved surfaces, which has potential applications in aerospace and medical devices.We are experimenting with innovative ink formulations and techniques, Ramakrishnan said. The equipment is helping us produce new and exciting next-generation sensors for NASA.A focus on medical applicationsAnother aspect of the research involves studying how human cells grow and interact in microgravity environments.Co-Director and Assistant Professor Jamel Ali from the Department of Chemical and Biomedical Engineering is leading efforts to examine the behavior of 3D printed tissues in space, with the goal of enhancing therapeutic cell expansion and regenerative medicine. For this purpose, Alis research group is working with researchers at the Mayo Clinic in Jacksonville, who are working with NASAs Kennedy Space Center on related projects.Alis team is also developing semiconducting nanomaterials through EHD printing that are specifically tailored to meet NASAs requirements. Their work includes establishing guidelines to address the challenges associated with 3D printing on curved surfaces.According to the researchers, the outcomes of these projects could extend beyond space exploration. Technologies developed through these initiatives, including sensors, tissues, and other materials, could have broader applications in biomedicine, materials science, and other fields that require advanced manufacturing techniques.In-space manufacturing with 3D printingOngoing developments in manufacturing technology are steadily bringing in-space manufacturing closer to practical application. This year, the European Space Agencys (ESA) Metal3D project sent the first metal 3D printed part produced in space to Earth for testing.Metal 3D printed part from space. Photo via ESA.Manufactured aboard the ISS using Metal 3D Printer developed byAirbus Defence & SpaceandAddUp, the part was created in mid-2024 and has now arrived at ESAs European Space Research and Technology Centre (ESTEC) in the Netherlands for analysis. Researchers will compare it with Earth-printed samples to evaluate how microgravity affects the printing process, providing data essential for developing reliable in-space manufacturing for future missions.Back in 2023, in-space manufacturing deep-tech startup Orbital Composites received a $1.7 million U.S. Space Force SpaceWERX Orbital Prime SBIR contract, funded by the Air Force Research Laboratory (AFRL), to advance In-space Servicing, Assembly, and Manufacturing (ISAM) antennas.Working with Axiom Space, Northrop Grumman, and Southwest Research Institute (SwRI), Orbital aims to enhance Satellite-Based Cellular Broadband (SBCB) and Space-Based Solar Power (SBSP) through in-space manufacturing. The project seeks to reduce costs and expand commercial opportunities by building antennas directly in space.What3D printing trendsshould you watch out for in 2025?How is thefuture of 3D printingshaping up?To stay up to date with the latest 3D printing news, dont forget to subscribe to the 3D Printing Industry newsletter or follow us on Twitter, or like our page on Facebook.While youre here, why not subscribe to our Youtube channel? Featuring discussion, debriefs, video shorts, and webinar replays.Featured image shows Jamel Ali, Ph.D., (L) and Subramanian Ramakrishnan, Ph.D., pose with the nScrypt 3D printer at the High-Performance Materials Institute (HPMI) of the Materials Research Building (MRB) at FAMU-FSU College of Engineering in Tallahassee, Florida. Photo via FSU.
0 Comments
0 Shares
24 Views