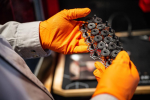
3DPRINTINGINDUSTRY.COM
Raise3D launches its new RMS220 SLS and DF2+ DLP 3D printer: Technical specifications and pricing
3D printer manufacturer Raise3D has marked its tenth anniversary by launching two new 3D printers at RAPID + TCT 2025 in Detroit, taking place from April 8-10.
The company introduced the RMS220, its first Selective Laser Sintering (SLS) 3D printer, and the DF2+, an enhanced Digital Light Processing (DLP) resin system that builds on its predecessor, the DF2. Both systems aim to meet the growing demand for reliable, end-to-end AM workflows that support a range of production needs.
Raise3D CEO Edward Feng said, “To meet these needs, Raise3D takes a full-process approach—from deep integration of software, hardware, and materials to a comprehensive ecosystem spanning FFF, DLP, and SLS technologies. We focus on balancing performance, cost, and efficiency to drive innovation and ease production challenges.”
Both systems have been validated for use in custom jigs, functional prototypes, and low-volume parts. The DF2+ is expected to begin shipping in the second quarter (Q2) 2025, with the RMS220 following in Q4 for the US and Europe.
During the RAPID + TCT event, Raise3D is offering live demonstrations, application overviews, and sample part displays at Booth 3025.
3D printed part made with DF2+. Photo via Würth Additive Group.
Key benefits of the RMS220 SLS 3D printer
According to the manufacturer, the RMS220 serves as Raise3D’s first production-oriented SLS system, developed to accommodate batch manufacturing requirements. It offers up to 5 kgs of daily 3D printed output using PA12, supported by a 220 × 220 × 350 mm build volume. For users needing fast turnaround, the printer delivers a speed of up to 2.2 L/hr at 20% fill density.
Raise3D has equipped the system with a modular build chamber and a powder-change process that takes roughly 45 minutes, making it easier to switch between materials with minimal downtime. A high-performance 1064nm laser allows the use of a broad range of materials, including PA12, PA11, and TPU, while maintaining a low total cost of ownership by streamlining efficiency across hardware, consumables, and workflow.
From a production standpoint, the RMS220 aims to deliver reliable results with precision. It supports a dimensional accuracy of ±0.2 mm and a minimum wall thickness of 0.5 mm when using PA11, which can be useful for detailed parts or functional prototypes.
A 75W laser and a four-zone, self-calibrating infrared heating system help maintain consistent material properties across batches. Designed with ease of use in mind, the system requires less training and upkeep, while its compact size reduces space demands in production environments.
Expanded resin compatibility and digital inventory integration for DF2+
Raise3D’s latest DF2+ DLP 3D printer includes a high-power, longer-lasting light engine and a 20% print speed increment. The system is compatible with a wider range of high-performance resins and includes a post-processing workflow with radio-frequency identification (RFID) traceability to support a streamlined production loop.
Material flexibility remains a central focus. Through its Open Material Program (OMP), Raise3D is working with partners such as Henkel and Forward AM to validate a growing list of resins. By Q2 2025, over 30 options are expected to be available, including ESD-safe, fire-retardant, high-temperature, medical-grade, flexible, clear, and high-impact materials. This expansion is intended to support applications across a wide range of industries.
Additionally, Raise3D has partnered with Würth Additive Group, demonstrating a fully integrated system in Würth’s Digital Inventory Services (DIS) platform. Having showcased at AMUG 2025, the setup is described as the first 3D printer integration with encrypted digital part distribution and secure, on-demand manufacturing capabilities. This combination is aimed at enabling more scalable use of AM within industrial supply chains.
Technical specifications and pricing of RMS220 SLS and DF2+ DLP 3D printer
For more details about the 3D printers, contact or visit the Raise3D website.
RMS220 SLS 3D printerTechnologySelective Laser Sintering (SLS)Build Volume220 × 220 × 350 mm (8.7 × 8.7 × 13.8 inch)Laser Type75 W fiber laser, wavelength 1064 nmPrinting Speed2.2L/h (packing density 20% by weight)Max Powder Temp.220°CHopper Size31.5 L, 40 L if extended with material boxMaximum Output5 kg/ Day**Using PA12 material and standard parameter settings, packaging density is 20% of weightLayer Height0.05 – 0.40 mmSupported MaterialsRaise3D PA12 Powder/ Raise3D PA11 Powder/ Raise3D TPU90A White Powder/ Raise3D TPU90A Powder/ Raise3D PA12 GB PowderSlicerideaMakerInput File FormatsSTL/ OBJ/ 3MF/ OLTP/ STEP/ STP/ IGES/ IGS
DF2+ DLP 3D printerTechnologyDigital Light Printing (DLP)Build Size (W × D × H)200 × 112 × 300 mm (7.87 × 4.41 × 11.8 inch)Max Printing Speed100 mm/h (Using Draft Resin and 200 μm layer height on DF2+. Actual print time obtained by printing a set of test parts at room temperature: 24-26°C, humidity: less than 50%)General Printing Speed50-60 mm/h (Average of all Raise3D materials printed at 100 μm layer height. Print speed will vary depending on resin type, layer height and part geometry, etc.)XY Resolution2560 × 1440Layer Height50-200 micronLight Source DensityTwice the light source density of DF2Raise3D ResinsRaise3D Standard White Resin, Raise3D High Detail Apricot Resin, Raise3D Tough 2K Grey Resin, Raise3D Rigid 3K Grey Resin, Raise3D High Clear Resin, Raise3D Draft Grey ResinComing Soon: Raise3D Standard Black, Raise3D ESD, Raise3D High Temperature ResinOpen Material Program (OMP)LOCTITE 3D IND405, LOCTITE 3D PRO476, LOCTITE 3D 3843, LOCTITE 3D PRO410, LOCTITE 3D PRO417, Ultracur3D RG 3280, Ultracur3D RG 1100 B, Ultracur3D EL 60, Ultracur3D EL 4000Coming Soon: LOCTITE 3D IND147, LOCTITE 3D 3843 White
What 3D printing trends should you watch out for in 2025?
How is the future of 3D printing shaping up?
To stay up to date with the latest 3D printing news, don’t forget to subscribe to the 3D Printing Industry newsletter or follow us on Twitter, or like our page on Facebook.
While you’re here, why not subscribe to our Youtube channel? Featuring discussion, debriefs, video shorts, and webinar replays.
Featured image shows 3D printed part made with DF2+. Photo via Würth Additive Group.
Ada Shaikhnag
With a background in journalism, Ada has a keen interest in frontier technology and its application in the wider world. Ada reports on aspects of 3D printing ranging from aerospace and automotive to medical and dental.
0 التعليقات
0 المشاركات
65 مشاهدة