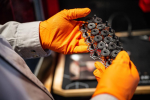
3DPRINTINGINDUSTRY.COM
How Vestas and Würth Are Industrialising Additive Manufacturing: AMUG Conference 2025
A conversation between Würth Additive Group and Vestas at the 2025 AMUG Conference discusses additive manufacturing as a scalable tool for managing supply chain risk, reducing downtime, and aligning with digital and sustainability strategies.
AJ Strandquist, CEO of Würth Additive Group, and Jeremy Haight, Principal Engineer & Lead Specialist – Additive Manufacturing & Advanced Concepts, at wind turbine leader Vestas, unpacked how tightly controlled digital workflows, qualified platforms, and strategic deployment are unlocking real-world value from 3D printing.
Jeremy Haight, Vestas and AJ Strandquist, Würth Additive Group [L-R]. Photo by Michael Petch.
TLDR? Key Insights
Pressed for time? Here are the core insights from the experience of Würth Additive Group and Vestas with additive manufacturing.
Think in terms of systems
Standards and qualification are lagging but crucial
Additive manufacturing’s strength is in the supply chainDigital control and lockdown of processes are essential
The industry suffers from a lack of interoperability
Backward compatibility is hard, forward integration is better
Quality failures require root cause analysis, not blame
Additive Manufacturing’s Supply Chain Moment: Würth and Vestas Eye Scale with Digital Inventory, Quality Controls
Würth Additive Group and Vestas are building the infrastructure for additive manufacturing to move beyond niche applications and into global-scale, supply chain-critical roles.
Strandquist framed the opportunity—and the challenge—with a touch of dry humor. “All the party animals are in this room talking about liabilities and quality concerns,” opening the session in Chicago. The two leaders are overseeing the deployment of additive manufacturing as a foundational capability within highly structured industrial ecosystems.
Strandquist’s mandate is to integrate additive manufacturing into Würth’s global logistics and distribution networks, embedding digital part fulfillment into traditional supply chains. The goal, he explained, is to ensure that customers can order 3D printed parts with the same ease and procedural traceability as legacy components. “For us, wherever that demand comes from… they’re going to place an order into a system,” he said. “From that system, we are going to integrate so a buyer sees the part on the screen just like anybody else does… [with] complete traceability.”
The underlying vision is a seamless supply experience—whether parts are made traditionally, pulled from stock, or 3D printed locally on demand. This includes modalities as diverse as vending machines and e-commerce.
The Würth AM leader draws a distinction between cost-driven components and critical engineered parts, noting that “quality is not consistent”—and shouldn’t be. “I specialize in parts that are very low cost… like automotive clips,” he said, contrasting this with Vestas’s use cases, which include R&D prototypes and operational components in high-risk environments. These differences demand scalable quality regimes, such as Production Part Approval Process (PPAP), with levels ranging from “use any machine and any vendor” flexibility to traceability down to raw material origins. Haight highlighted the need to balance internal and external production while ensuring the sanctity of quality documentation and design control.
Both executives stressed that additive manufacturing often steps in as a second-source or emergency solution. As Strandquist put it: “3D printing always does best in [special] situations. The price point doesn’t matter when something’s missing.”
This flexibility introduces new considerations around intellectual property and digital security. Ensuring that only approved files are used, and that they are not modified or leaked, is critical.
Vestas and Würth Advance AM Supply Chains with Rigorous Controls and Distributed Infrastructure
The transition of additive manufacturing to an industrial-scale technology demands enterprise-grade systems, traceability, and precise vendor control—alongside the physical decentralization that defines the technology’s core advantage.
“Across industry, especially in heavy industry, additive is seen either as novelty—or something exclusive to aerospace and medical. Digital manufacturing removes that mental barrier,” said Haight. For some time, the term “digital manufacturing,” or DVM was used at Vestas to remove this artificial barrier to adoption.
Haight oversees a program that spans composite tooling, metal components, and concrete printing, all integrated into a global enterprise stack. The architecture ties in AM part production with Vestas’s existing ERP, PLM, and asset management systems. “Right off the printer, they get the part and the ISO 17025-qualified inspection report with it. That’s all tied into our enterprise asset management system—fluid and automated,” he explained.
The Vestas roadmap, already partially implemented, includes mobile units embedded in EVs that 3D print parts en route to remote wind farms.
Würth Additive Group is aligning its infrastructure accordingly. The CEO noted the importance of preserving manufacturing fidelity without introducing complexity at the customer interface. Repeatability often hinges on process discipline, especially in mid-volume applications. One contributor described a production run of “under 100,000 per year,” developed over seven years with a QA/QC pipeline embedded directly into the partner company’s systems. The bottlenecks, unsurprisingly, have been in material consistency and knowledge loss as teams changed. Strandquist underscored this as a known risk. “That was a living process, not a frozen one. I always say: freeze it, then you can thaw it and freeze it again. But you never want to be out of that frozen state very long if you have a production part.”
To combat fragmentation and maintain data discipline, Vestas operates on a strict ‘recipe’ model when outsourcing AM work. “We have a qualified machine, qualified materials with batch and lot traceability, and we simply provide [vendors] a recipe,” Haight said. “They can run it, do visual inspection, but that’s the limit of what they can do.” Sensitive IP is protected using classic techniques such as segmented production and robust NDAs—“sometimes you’re not going to get around it.”
Internally, Vestas has mapped out the additive landscape by technology and business function—composites, metals, base polymers, concrete—and tied them to process families, use cases, and ROI thresholds. The logic is surgical: match material and process capabilities directly to component types, from turbine blade precast molds to rotor-stator assemblies and directional fiber reinforcement.
“We want something that’s going to merge with your ecosystem, not fight it,” Haight emphasized.
Jeremy Haight shows how Vestas maps the landscape. Photo by Michael Petch.
Locking Down the Digital Factory: Vestas and Würth Tackle IP Control, Operator Simplicity, and Legacy Parts in AM Supply Chains
Additive manufacturing’s promise of distributed, on-demand production hinges not just on technology readiness but on governance, security, and organizational alignment. That means managing everything from untrained field operators to multi-million-part inventories with automation, policy enforcement, and strategic vendor selection.
“The people in the field don’t need to be experts,” said Haight. “We use RBAC—role-based access control. These are pre-fixed recipes stored in our PLM. They can’t be modified. It’s locked down by design.”
This is not only a matter of usability, but also of trust and compliance. Strandquist noted that errors and deviations are rarely technological. “If you can’t trust your people to follow a standard operating procedure, you can’t trust them with anything else,” he said. “There’s no fixing deviancy. The best you can do is design systems so it’s hard to cheat.”
Vestas, operating across dozens of countries, avoids such risk by choosing closed ecosystem platforms and suppliers. Their initial AM rollout centered on closed-loop systems with tight administrative controls. “We own the mandate for additive,” said Haight. “We want to discourage non-compliant printers or materials entering our factories.”
In some cases, such as concrete tower components, Vestas ships the entire printing process while sourcing raw materials locally. This avoids cross-border complexity while aligning with longer-term ambitions around circularity. “We’re working on reclaiming materials and recomposing them into new AM workflows,” said Haight. “Digital twin meets recyclability.”
That model also opens a unique geopolitical advantage. “There are no tariffs on emails yet,” Strandquist quipped. “You can transform material in-country, avoid customs issues entirely, and still deliver a spec-inspected part. That’s a huge advantage when things get stuck at the border.”
Still, the most enduring challenge lies in managing the legacy footprint. “We’ve got close to 32 million SKUs in our PLM and DMS,” Haight said. “So that’s a job for software.” Vestas uses automated part screening platforms to identify additive-suitable candidates, and in some cases, works directly with operators under right-to-repair laws. Their field qualification metric is straightforward: one year of continuous fault-free operation.
For new parts, however, additive has more traction—particularly in long-lifecycle support. “Looking backward for AM is inherently hard,” said Strandquist. “The strength is in designing for additive from the beginning. Once your production tooling wears out, the 3D printed version is already certified because it was in the original test batch.”
This forward-looking view also supports dynamic sourcing strategies. Both Haight and Strandquist described additive as a bridge and fallback in the face of tooling delays or vendor outages. “It opens up alternative supply options,” Haight said. “You never want to be single-source.”
Standards, Supply Chains, and Stakeholder Trust: AM Leaders Urge Structural Maturity in Digital Manufacturing
The industry’s next evolution depends less on technology than it does on institutional trust, interoperable standards, and system-wide process controls.
Despite the focus on automation and documentation, failures still require forensic analysis. “If a part breaks after 10,000 units, that’s not an AM issue. That’s a design issue,” said Strandquist. “But if one breaks on its own, you start looking at the black box.”
Resistance from inside organisations remains a hurdle, especially among engineers accustomed to legacy systems. “A lot of them have been jaded by automation that only delivered 30% of what was promised,” Haight said. The response has been to demonstrate performance directly: “Put the part in their hand. Prove it.”
Environmental metrics—another critical performance area—remain difficult to quantify with confidence. While Vestas aligns its AM programme with decarbonisation goals and Industry 4.0 principles, the carbon math is elusive. “It’s an incredibly complex model,” said Haight. “We try, but it’s mostly qualitative.” Strandquist agreed: “I haven’t seen a tool I would bet my reputation on. There’s too much nuance for a punch-in algorithm.”
Still, the industrial logic is hard to dispute. AM cuts downtime risk and inventory costs. Yet the broader industry remains fragmented by design. Standardised machine communications and cross-platform compatibility are still missing. “It’s like early railroads,” Strandquist said. “Every state had a different gauge. They didn’t think nationally.” He warned that locking users into proprietary systems was self-defeating: “You don’t buy computers that can’t talk to each other. AM should be the same.”
There are signs of movement. Both leaders acknowledged the progress of groups like ASTM F42, which is working on standardised data packaging and pedigree handling. “To unlock AM’s full value, new technologies must enter with robust vetting and a clear business case. “We look at technology readiness level and match it to a real customer need,” said Strandquist. “That proof of concept is where we learn the most.”
“If we’re strategic and objectively seeking business results, we’ll find a path,” Haight said. “But you need the mandate, the metrics—and the buy-in.”
The path forward demands standardisation, openness, and the recognition that AM is not a magic bullet—it’s a business tool. “It’s a shortcut for your supply chain,” Strandquist noted, “but only if you treat it like part of the system, not something separate from it.”
Read more from the 2025 AMUG Conference.
Ready to discover who won the 2024 3D Printing Industry Awards?
Subscribe to the 3D Printing Industry newsletter to stay updated with the latest news and insights.
Featured image shows a 3D printed part made with DF2+. Photo via Würth Additive Group.
Michael Petch
Michael Petch is the editor-in-chief at 3DPI and the author of several books on 3D printing. He is a regular keynote speaker at technology conferences where he has delivered presentations such as 3D printing with graphene and ceramics and the use of technology to enhance food security. Michael is most interested in the science behind emerging technology and the accompanying economic and social implications.
0 التعليقات
0 المشاركات
63 مشاهدة