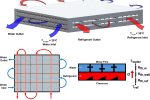
3DPRINTINGINDUSTRY.COM
Revolution in Cooling Tech: Research finds 3D Printed Condenser Outperforms Traditional Designs
Researchers at the University of Illinois Urbana-Champaign have developed a compact water-cooled condenser using additive manufacturing (AM), demonstrating a significant performance improvement over conventional heat exchanger designs. Published in the International Journal of Heat and Mass Transfer, the study introduces a 3D-printed aluminum condenser for R134a refrigerant with internal features tailored to maximize heat transfer efficiency. The device achieved volumetric power densities of up to 6.2 MW/m³, outperforming traditional shell-and-tube designs by 30–50% while maintaining comparable pumping power.
3D printing enables advanced internal geometries
The condenser was fabricated using laser powder bed fusion in AlSi10Mg alloy, enabling the creation of complex internal geometries unachievable with subtractive methods. These include chevron-shaped flow disruptors on the refrigerant side and cross-shaped wavy fins on the water side, designed to enhance turbulence and improve local heat transfer coefficients. Unlike conventional heat exchangers, which rely on stacked plates or finned tubes, this 3D printed architecture allows for precisely tuned internal structures that manage flow, pressure drop, and thermal resistance across multiple fluid paths.
Cut-away CAD view of heat exchanger design, showing inset images of the chevrons in the refrigerant-side channels (top) and 3D wavy fins in the water-side channels (bottom). Image via William P. King.
Multi-pass crossflow architecture for compact performance
The condenser features a multi-pass, multi-channel crossflow architecture, designed to optimize heat exchange between water and refrigerant within a compact footprint. In a crossflow configuration, the two fluids, cooling water and refrigerant, flow perpendicular to one another, enhancing thermal contact across the heat exchanger’s internal surfaces.
Design of the AM crossflow refrigerant condenser. Image via William P. King.
Multiple parallel flow paths within each fluid domain, increase surface area and improve flow distribution. Both the water and refrigerant are routed through the condenser in several sequential stages. In this design, the refrigerant flows through four passes, each with progressively narrower channels to compensate for increasing density as it condenses. Simultaneously, water flows through its own four-pass circuit in the opposite direction.
This architecture enables fine control over fluid velocity, pressure drop, and thermal gradients, ensuring efficient energy transfer between the two working fluids. Despite its internal complexity, the unit maintains a compact outer dimension of 260 × 235 × 39 mm.
Simulation-guided optimization and machine learning integration
To optimize water-side performance, the research team combined 2D finite element simulations with a machine learning model trained on 36,000 parameterized fin shapes. The model predicted fin efficiency and area enhancement factor as inputs to a physics-based segmented thermal model. Design candidates were filtered through parametric sweeps and refined using CFD simulations to verify local temperature, velocity, and pressure distributions.
Segmentation procedure of the condenser. Image via William P. King
Experimental verification in a custom vapor-compression loop
The prototype was experimentally tested in a custom-built vapor-compression loop. The condenser demonstrated heat transfer rates between 3 kW and 8 kW, at refrigerant saturation temperatures ranging from 35°C to 49°C. Water-side flow rates were tested between 5 and 40 liters per minute. The physics-based model and CFD results matched experimental data within 5% accuracy, validating the reliability of the simulation framework.
Compatibility with low-GWP refrigerants
Although initially tested with R134a, the study evaluated performance with other refrigerants such as R1234yf, R32, propane, and isobutane. These refrigerants have lower global warming potential (GWP) compared to R134a and were assessed using the same geometry and comparable volumetric flow rates. Simulations showed that R32 achieved up to twice the heat transfer rate of R134a at higher flow rates, while propane and R1234yf showed similar or slightly improved performance.
Outlook for additive thermal components
The research provides a validated design methodology for compact, high-efficiency two-phase heat exchangers using AM. The ability to fine-tune thermal resistance, flow paths, and geometry at the segment level, combined with verified CFD and experimental results, positions this approach as viable for real-world applications in HVAC, automotive, data centers, and aerospace systems.
The condenser design adds to a growing body of research and commercial development using 3D printing to reshape heat exchanger performance. A recent study by Lawrence Livermore National Laboratory (LLNL), highlighted in MIT Technology Review, explored using metal 3D printing to fabricate miniaturized heat exchangers for use in electronics and aerospace. These devices incorporated folded geometries to maximize surface area, though performance gains in early testing remained modest.
Meanwhile, companies like Conflux Technology, In October 2024, Conflux raised €11 million in Series B funding to expand its production of 3D printed heat exchangers using laser powder bed fusion. The company has also partnered with Rocket Factory Augsburg to integrate 3D-printed heat exchangers into orbital rockets, demonstrating the applicability of AM in producing components capable of withstanding extreme conditions. The company also launched a high-performance cartridge-style heat exchanger designed for fluid control systems in automotive and industrial environments, characterized by its compact form and optimized internal geometry.
Other efforts include GE Research, which developed a grape-shaped 3D-printed heat exchanger capable of operating at 900°C, surpassing the temperature limits of existing solutions by over 200°C. These developments demonstrate the flexibility and application-specific design benefits of additive manufacturing in thermal management systems.
The full research paper, Additively Manufactured Compact Water-Cooled Refrigerant Condenser, is available here via International Journal of Heat and Mass Transfer.
Subscribe to the 3D Printing Industry newsletter to keep up with the latest 3D printing news.
You can also follow us on LinkedIn and subscribe to the 3D Printing Industry Youtube channel to access more exclusive content.
Feature image shows Design of the AM crossflow refrigerant condenser. Image via MIT William P. King.
Rodolfo Hernandez
Rodolfo Hernández is a writer and technical specialist with a background in electronics engineering and a deep interest in additive manufacturing. Rodolfo is most interested in the science behind technologies and how they are integrated into society.
0 التعليقات
0 المشاركات
71 مشاهدة