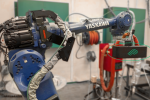
3DPRINTINGINDUSTRY.COM
Phase3D rolls out new in-situ QA tool for cold spray AM, also suited for LPBF
Chicago-based 3D printing quality assurance software developer Phase3D has introduced a new inspection system designed to improve quality assurance (QA) in cold spray additive manufacturing (CSAM).
Supported by $1.25 million in funding from the Air Force Research Laboratory (AFRL), the system, called Fringe Inspection: Cold Spray, uses structured light to capture surface data in real time during the spray process. It was tested at the University of Dayton Research Institute (UDRI) and later validated in an operational environment at Ellsworth Air Force Base.
CSAM has long presented challenges in maintaining consistent quality due to the nature of the material deposition process. Phase3D’s system addresses these challenges by providing real-time data that allow for immediate identification of surface-level defects such as cracking, cratering, and pitting.
The system also evaluates the flatness and overall shape of the deposited surface, offering technicians the opportunity to adjust process parameters dynamically, thereby reducing material waste and improving efficiency.
“The successful completion of this project underscores the importance of real-time inspection in additive manufacturing, ”said Niall O’Dowd, Founder and CEO of Phase3D. “The deployment at Ellsworth AFB proves that structured light inspection is a game-changer for cold spray applications. This technology not only ensures higher-quality repairs but also delivers significant cost and time savings for the Air Force.”
Fringe Inspection : Cold Spray attaches to the robotic control arm and scans cold spray deposits during the printing process. Photo via Phase3D.
Validated through real-world testing
The Fringe Inspection : Cold Spray hardware is mounted to a robotic arm, where it collects millions of measurement points related to layer thickness, roughness, and shape. Phase3D developed and deployed both the hardware and its accompanying software suite, Fringe Operator, which is used to interpret inspection data and document part-specific quality metrics.
Working with Air Force engineers, the team established data-driven benchmarks for acceptable and unacceptable deposition quality, drawing on cold spray samples created with helium and nitrogen as carrier gases. These examples informed the creation of a go/no-go threshold system to evaluate parts during the manufacturing process.
To validate this approach, Phase3D conducted a blind test using the quality thresholds it had developed. Components were evaluated using real-time data collected during the build process, and defects such as uneven spray patterns and surface discontinuities were identified and categorized.
The successful classification of test specimens further confirmed the utility of the system for in-situ inspection in cold spray environments. This project was conducted under the STTR Phase II Proposal F2-16465 – In-Situ Monitoring for Blown Powder Additive Manufacturing contract.
A separate case study involving a laser powder bed fusion (LPBF) component 3D printed on an EOS M270 machine further demonstrated the practical benefits of Fringe Inspection technology.
An undisclosed aerospace manufacturer faced part failures caused by inconsistent porosity and internal geometries, traced to powder buildup on the recoater blade that intermittently dropped onto the build surface, an issue technicians suspected but couldn’t confirm using standard imaging tools.
After installing Fringe Inspection on the machine, the issue became immediately visible through high-resolution heightmaps. The system detected powder drops of up to 200 µm, four times the normal layer thickness, falling onto the melt pool.
The discovery led to a simple fix: adding a fixed blade at the recoater’s home position to prevent powder buildup. After implementation, powder-related build failures stopped entirely, reducing annual losses of $63,000 by over 90%, not including indirect engineering and troubleshooting costs.
Following these successful implementations, Phase3D plans to expand the application of its structured light inspection systems beyond cold spray. The company is currently engaging with the U.S. Department of Defense (DoD) and private-sector partners to explore additional use cases and support broader adoption of real-time quality monitoring in additive manufacturing.
The case study is based on reported findings and represents a real set of events. No confidential figures were used, and all data has been recreated to protect customer privacy.
Quality Chart output from Fringe Inspection identifying when the process is out of control during the process. Visualized in Fringe Qualification. Image via Phase3D.
Quality assurance in 3D printing
In-situ quality assurance is essential for industries like aerospace and space, where standards are high, prompting many AM companies to develop their own novel solutions.
For example, Siemens Energy and risk management firm DNV partnered to develop a new industrial quality assurance platform by integrating Siemens’ AM Cockpit with DNV’s Independent Quality Monitor (IQM). The platform enables real-time monitoring, digital validation, and comparison of 3D printed parts against approved models.
It provides automated certification and aims to support zero-defect manufacturing, particularly in powder bed fusion processes. Developed under the EU-funded InterQ project, the combined system is designed to strengthen confidence in AM for critical sectors like energy, with Siemens highlighting its role in enabling gas turbines to operate on low-carbon fuels such as hydrogen.
During the Formnext 2022, MakerVerse and ZEISS introduced enhanced quality assurance tools on the MakerVerse platform through the integration of ZEISS’s specialized metrology solutions. These additions included Tactile CMM, Optical 3D Scanning, Industrial CT and X-Ray capabilities, along with surface roughness measurement. MakerVerse CEO Dr. Markus Seibold emphasized that this alliance “is the perfect solution for our customers needing industrial-grade quality inspections and reports for their AM parts.”
What 3D printing trends should you watch out for in 2025?
How is the future of 3D printing shaping up?
To stay up to date with the latest 3D printing news, don’t forget to subscribe to the 3D Printing Industry newsletter or follow us on Twitter, or like our page on Facebook.
While you’re here, why not subscribe to our Youtube channel? Featuring discussion, debriefs, video shorts, and webinar replays.
Featured image shows Fringe Inspection : Cold Spray attaches to the robotic control arm and scans cold spray deposits during the printing process. Photo via Phase3D.
Ada Shaikhnag
With a background in journalism, Ada has a keen interest in frontier technology and its application in the wider world. Ada reports on aspects of 3D printing ranging from aerospace and automotive to medical and dental.
0 التعليقات
0 المشاركات
62 مشاهدة