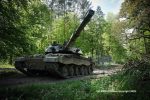
3DPRINTINGINDUSTRY.COM
Babcock to support 3D printing of military parts for Ukraine under the latest MoD contract
The UK Ministry of Defence (MoD) has awarded British defense company Babcock a proof-of-concept contract to help Ukrainian personnel 3D print military equipment.
As the lead contractor, Babcock will work with defense technology firm QinetiQ to create digital drawings, including computer-aided design (CAD) files of key military components. These files would enable Ukrainian forces to manufacture replacement parts locally, using 3D printing.
Tom Newman, CEO of Babcock’s Land Sector, said, “We aim to give Ukraine the capability to recreate the military parts that they need, where and when it really matters. This innovation builds on our engineering expertise and technology capability, giving us further opportunities to optimise 3D printing.”Separately, Babcock is helping maintain and repair vehicles such as Challenger 2 tanks, managing spare parts and supply chains, and training the Ukraine military to carry out repairs independently.
The Challenger 2 tank. Photo via UK MoD.
Global military support for Ukraine
A core element of the project involves reverse engineering older or legacy components that are difficult to source or no longer manufactured. By analysing their structure and function, the team aims to digitally recreate them for fabrication in the field. This approach could help Ukrainian forces maintain equipment in combat zones where conventional supply chains are disrupted or delayed.
The broader significance of the effort lies in its potential to showcase how digital manufacturing can be used to support military logistics during active conflict. A validated digital catalogue of essential components would allow faster repairs and reduce downtime for high-use or frequently damaged systems.
Babcock noted that the project builds on its broader expertise in engineering and field support, while QinetiQ brings specialist capabilities in materials assurance and technical validation. Alan Hart, Managing Director of Science, Technology and Weapons for QinetiQ explained that this latest contract demonstrates QinetiQ’s “commitment to support to the frontline, whether our own or those of our allies.”
This initiative adds to the UK’s ongoing military assistance to Ukraine. Away from the British, militaries from other nations reportedly contributed to Ukraine’s war efforts against Russia.
In 2023, SPEE3D delivered seven WarpSPEE3D 3D printers to Ukraine as part of the US Department of Defense’s (DoD) Ukraine Security Assistance program. To support their effective use, the company ran a 15-day training course for Ukrainian military personnel, focusing on how to operate cold spray additive manufacturing (CSAM) systems in the field.
According to Calum Stewart, SPEE3D’s Director of Defense Programs, the technology allows soldiers to keep more equipment operational for longer durations. Similar to the XSPEE3D, the WarpSPEE3D system is designed for deployment in remote or hard-to-access areas, enabling the on-demand production of metal parts. Stewart noted that the machines are transportable and can be set up and ready for use in under an hour.
Essentium is another 3D printing company providing support to Ukraine. In partnership with KVG, the company introduced its High-Speed Extrusion (HSE) 3D printers at multiple sites across the country. Like SPEE3D, Essentium ensured local teams received hands-on training to keep production running smoothly and consistently.
Essentium’s High-Speed Extrusion (HSE) 3D printer. Photo via Essentium.
3D printing military equipment
3D printing is increasingly being used to produce military equipment on demand, speeding up repairs, reducing supply chain reliance, and enhancing frontline readiness.
Earlier this year, Creech Air Force Base’s 432nd Wing installed two Bambu Lab 3D printers to support US Air Force (USAF) maintenance training for MQ-9 Reaper drones, addressing part shortages that previously disrupted operations. As part of a new manufacturing setup, over 800 personnel can now produce replacement components on-site, helping reduce downtime and logistical strain.
Fabricated parts include those for airframe propulsion and power generation systems, with broader applications such as diagnosing aircraft damage and printing spares at the point of need. In some cases, parts that once cost thousands can now be produced in-house for a fraction of the price.
In 2020, the Indian Navy partnered with Indian 3D printing bureau think3D to address spare part shortages caused by aging, imported equipment. Focusing on components like centrifugal pump impellers, think3D reverse engineered and 3D printed replacements using HP’s Multi Jet Fusion (MJF) technology.
The new impellers were lighter, 40% cheaper, and produced in just two days compared to three months via traditional methods. After successful shipboard testing, think3D began developing a digital repository for on-demand production and is working on a customized 3D printer capable of operating offshore with pre-loaded CAD designs to enable rapid in-situ manufacturing.
What 3D printing trends should you watch out for in 2025?
How is the future of 3D printing shaping up?
To stay up to date with the latest 3D printing news, don’t forget to subscribe to the 3D Printing Industry newsletter or follow us on Twitter, or like our page on Facebook.
While you’re here, why not subscribe to our Youtube channel? Featuring discussion, debriefs, video shorts, and webinar replays.
Featured image shows the Challenger 2 tank. Photo via UK MoD.
0 Comentários
0 Compartilhamentos
60 Visualizações