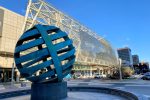
3DPRINTINGINDUSTRY.COM
RAPID + TCT 2025 Roundup: New Technology and Executive Insights from the Show Floor
Last week, over 500 exhibiting companies and over 15,000 attendees converged on Detroit’s Huntington Place for RAPID + TCT 2025. Despite uncertainty around shifting tariff policies and volatile stock markets, a sense of cautious optimism was evident on the show floor.
Many agreed that the industry has entered a new stage of maturity, where hype is fading and practical applications and user value are taking center stage. The focus of the show also shifted away from flashy product launches, and while RAPID + TCT 2025 featured several new systems (detailed below), they played a smaller role than in previous years.
Read more news from RAPID + TCT 2025
Steve Prahalis, Chief Operating Officer at the event organizer SME, identified that previous shows saw many “big and beautiful booths” designed to satisfy shareholders and one-up competitors. He believes this mentality has ceased, with companies more focused on demonstrating how they address customer challenges.
RAPID + TCT sign at Huntington Place. Photo by 3D Printing Industry.
The overall sentiment at the show reflected a conscious shift from revolution to evolution, with less appetite for disruption and technological innovations. During the executive perspectives panel on day one, EOS President Glynn Fletcher argued that the industry should shift from “cool” to “cost-effective” because “cool is not a business model.” He expressed the need for the 3D printing industry to “fit into the bigger picture of manufacturing” and move from an “adversarial industry” to a “complementary industry.”
Other panelists emphasized the importance of collaboration. Brigitte de Vet-Veithen, CEO of Materialise, believes that “collaboration can really drive growth.” SME’s Prahalis shares this vision. He told me, “The hype cycle’s over, we need to be realistic. We need to collaborate.”
This was echoed by Stratasys’ CEO Yoav Zeif, who warned against internal competition between additive manufacturing companies. Instead, he argued that “the competition is the status quo.” For Zeif, delivering value, meeting part requirements, and lowering the total cost of ownership are critical to increasing 3D printer adoption. “We need to focus on adoption, not hype,” he added. “If we focus and collaborate, we will win.”
The executive perspectives panel on day one of RAPID + TCT 2025. Photo by 3D Printing Industry.
RAPID + TCT 2025: Insights from the event organizers
SME is a nonprofit organization with a mission to promote advancements and increase the adoption of additive manufacturing. 2025 marks 35 years since SME hosted its first “RAPID” conference in 1990, focused on rapid prototyping and stereolithography. Over three decades later, the annual event has grown into North America’s leading additive manufacturing trade show.
This year’s event saw RAPID + TCT co-locate with SME’s AeroDef Manufacturing, SAE International’s World Congress Experience (WCX) mobility show, and America Makes’ Technical Review & Exchange (TRX). Angie Szerlong, SME’s Group Director for Additive Manufacturing, called this collaborative approach “a very big highlight” for this year’s expo. She called the event “a mega place for all manufacturing groups to come together and experience all different parts of the supply chain.”
Prahalis echoed this sentiment. He revealed that the co-location helped elevate 2025 to the “largest RAPID we’ve had.” This year’s 15,000 attendees grew from around 9,000 last year. It included over 10,000 attending primarily for RAPID + TCT, 1,000 for AeroDef, 4,000 for WcX, and around 500 for the TRX program.
Co-location also reflects a growing effort to integrate 3D printing with broader manufacturing, increase usability, and deliver value for customers. Prahalis referenced the strong consensus among industry executives to “break into manufacturing” and “not just sing the praises” of 3D printing. He noted that additive manufacturing events have previously been predominantly attended by “AM enthusiasts” who have already bought into the technology, stunting scalability.
SME hopes to increase additive manufacturing’s presence at other industry events, for example, IMTS and FABTECH Expo. Increasing visibility will “get the general manufacturing audience to understand the impact of AM,” added Prahalis. As part of this mission, SME is working to integrate 3D printing into its Manufacturing Technology Series of expos and conferences. Prahalis also shared his vision for co-locating with other independent manufacturing shows in future iterations of RAPID + TCT. He compared this approach to the “Costco model,” allowing visitors from all verticals to get the most value from their trip to the exhibition center.
SAE’s WCX show sign. Photo by 3D Printing Industry.
New 3D printers unveiled at RAPID + TCT 2025
While RAPID + TCT 2025 was not as launch-heavy as previous iterations, several booths hosted new 3D printer announcements.
Massachusetts Institute of Technology (MIT) spinout Rapid Liquid Print (RLP) attracted plenty of attention by unveiling its new Levity Machine. Set to begin shipping next year, the new system features the company’s patented “gravity-free” 3D printing technology.
RLP’s technology was first showcased at Design Miami 2017. It allows soft, pliable silicone parts to be “drawn” within a gel suspension. The injected material is held in place as it is cured at room temperature, removing the need for support structures. According to RLP’s CEO and Co-founder, Schendy Kernizan, this process increases sustainability because users “only 3D print the material that they need.”
Rapid Liquid Priont’s gravity-free 3D printing. Photo by 3D Printing Industry.
The new Levity Machine can quickly fabricate large-scale parts with flexible, elastic properties. Originally designed for 3D printing furniture, Kernizan said RLP now focuses on medical applications such as orthotics and prosthetics. The Boston-based company has also expanded into large-scale gasket and sealing components for the aerospace, automotive, and marine industries.
Standing in the bustling RLP booth, Kernizan expressed his excitement at the “excellent” feedback his team received during RAPID + TCT 2025. “It’s showing that we’re solving the things that have been requested in terms of speed limitations and part quality,” he added. “Our goal is to give people the opportunity to bring this technology into their factory floor, and to go from prototyping to full production with the same machine.”
Rapid Liquid Print Levity Machine. Photo by 3D Printing Industry.
Stratasys once again stood out with one of the biggest booths at RAPID + TCT. According to the company’s Chief Business Unit Officer and President, Rich Garrity, exhibiting at North America’s primary additive manufacturing expo continues to pay off. “It’s been a great show so far,” he told me. “We had, I think, 40% more leads on day one than a year ago.”
During the show, the company presented its new Neo 800+ large-format SLA 3D printer, first announced during the AMUG 2025 conference in the week before the Detroit event. The updated system features Stratasys’ ScanControl+ scanning technology, reportedly accelerating 3D printing speeds by up to 50%. Vacuum System Protection, Z-Stage Collision Detection, and live environmental monitoring features are also included to enhance part quality and increase uptime.
At the Stratasys booth, visitors could also get hands-on with parts 3D printed using the company’s new PolyJet ToughONE photopolymer resin. This high-strength material delivers the mechanical performance for functional prototypes and end-use parts. ToughONE offers the highest impact resistance and shock absorption of any PolyJet material. As such, it closely mimics the properties of durable plastics like HDPE, PP, PBT, PC-ABS, PC, Nylon 12, and Nylon 6.
The Stratasys Neo 800+ at RAPID + TCT 2025. Photo by 3D Printing Industry.
The consumer resin 3D printer market also witnessed a new addition in Detroit. Shenzhen-based Elegoo revealed the Jupiter 2, a new LCD 3D printer featuring a 14-inch, 16K resolution screen and upscaled 302.40 x 161.98 x 300.00 mm build volume. Designed to directly address feedback from Elegoo’s customer base, the Jupiter 2 incorporates a modular design and LCD screen that can be swapped in 10 seconds. A 2kg detachable resin handling system has also been added to automate material feeding and recycling.
Elegoo Jupiter 2. Photo by 3D Printing Industry.
Coco Lee, Elegoo’s Brand Director, explained that while the Jupiter 2 will continue to serve the company’s core base of entry-level consumers, it has also been optimized for prosumers. Its increased build volume expands Elegoo’s reach to those wanting to fabricate large parts, achieve higher-quantity production runs, and access improved surface resolution. The desktop 3D printer’s price is yet to be revealed, with shipments set to begin in Q3 2025.
Inside the Elegoo Jupiter 2. Photo by 3D Printing Industry.
Another Chinese company that introduced new hardware was Shanghai-headquartered Raise3D. The company has entered the SLS 3D printing market with its RMS220 3D printer. Featuring a 220 x 220 x 350 mm build volume, 75-watt fiber optic laser, and up to 30,000 mm/second scanning speed, the system offers a maximum throughput of 2.2 liters per hour. Two swappable build chambers are included to maximize productivity and support batch production applications.
Ruben Nigaglioni, Raise3D’s Sales Director, explained that the RMS220 hopes to increase adoption by offering a “cost-effective way to get into industrial SLS 3D printing.” He added that combining a low price with advanced features helps the RMS220 differentiate within the industrial 3D printer market. Pre-orders are expected to open in Q3 2025, with the first systems being shipped the following quarter. Customers can purchase the 3D printer alongside Raise3D’s cleaning unit for de-powdering, and a sand-blasting unit for post-processing.
Raise3D’s RMS220 3D printer (right) and de-powdering station. Photo by 3D Printing Industry.
RAPID + TCT 2025 also witnessed new developments in metal 3D printing. Notably, Florida-based ADDiTEC introduced the Fusion S range, marking its entry into the metal laser powder bed fusion (LPBF) market. The company’s compact Fusion S 3D printer and Fusion Cabin unpacking station utilize a fully enclosed cartridge system. This allows users to safely transport 3D printed parts between machines without directly contacting the powder, removing the need for PPE and preventing material contamination. Featuring a 200 W laser and 50 µm welding spot, the Fusion S can fabricate parts with 10-50 µm layer thicknesses at up to 5 m/s.
ADDiTEC Fusion S Series. Photo by 3D Printing Industry.
Together, both units are priced at around $150,000, making them a cost-effective option in the LPBF space. ADDiTEC CEO Brian Matthews said the compact system is optimized for dental, medical, jewelry, and small aerospace parts. Its low cost and streamlined workflow also make it attractive to universities and research institutions. Although it debuted in Detroit, Matthews reported that the Fusion S has already received “a huge number of quotations” from interested customers. The British-born CEO plans to build a global distribution network for the Fusion S by year’s end.
ADDiTEC Fusion S swappable build cartridges. Photo by 3D Printing Industry.
German metal 3D printer manufacturer Ponticon showcased several parts fabricated using pE3D, its ultra-high-speed, laser DED system. This system features a unique tripod kinematic architecture. A stationary nozzle combines with a fast-moving build platform and precision-firing laser to 3D print at up to 200 meters per minute. The high-power laser melts the metal powder or wire feedstock, creating molten metal which is deposited onto the build platform layer by layer.
According to Dr. Simone Maffia, Head of Application Development, Ponticon’s technology is 200 times faster than most DED competitors, which can only produce parts up to two meters per minute. He also highlighted the pE3D’s ability to fabricate high-precision metal parts with walls as thin as 0.4 mm. This makes it well suited for aerospace, defense, and commodity applications. Every Ponticon system is customized for the customer and their specific application needs.
Ponticon 3D printed metal part. Photo by 3D Printing Industry.
Enhancing AI process monitoring in additive manufacturing
3D printing software at RAPID + TCT 2025 witnessed a strong focus on process monitoring optimized by artificial intelligence (AI) and machine learning.
One such exhibitor was Interspectral. Based out of Norrköping, Sweden, the company offers AM Explorer. This process monitoring and quality assurance software is optimized for metal additive manufacturing. According to CEO Isabelle Hachette, the company has made customized installations of its AI-powered defect detection software with metal 3D printer OEMs. She added that these “deep integrations” cover 60-70% of the metal LPBF 3D printer market, including EOS, Colibrium Additive, AddUp, Velo3D, and Nikon SLM Solutions’ NXG XII 600 range.
AM Explorer uses live 3D printing data and AI analysis to monitor the build process and detect defects in real-time. Its integrated AI models are trained to spot anomalies and trigger alerts and corrective actions. Users can view defects layer by layer through live visualization, enabling quick identification and response. This is especially valuable for high-volume runs using costly metal powder. “We can filter out the bad components from the good ones in a build job,” said Hachette. The software can then send an alert to pause the build and suggest adjustments to the process, like re-coating or changing the laser power.
According to Hachette, the company’s modular, vendor-specific AI architecture is unique among 3D printing software. “There is no one else that has this modular AI architecture,” she explained. “We can calibrate and use different AI models for specific systems, so we can really customize.”
Interspectral CEO Isabelle Hachette at RAPID + TCT 2025. Photo by 3D Printing Industry.
Another emergent company in the AI process monitoring software space is Euler. The Icelandic startup offers AI-powered defect detection for LPBF and SLS 3D printing. Its tool uses 3D printing camera data and AI algorithms to unlock automated analysis without the need for expensive monitoring equipment. It can detect part defects, predict 3D printing failures, and highlight common issues like uneven powder distribution, unfinished layers, and burns.
At RAPID + TCT 2025, Euler launched its process monitoring tool for EOS 3D printers. The plug-and-play software installs in under five minutes and requires no calibration, according to the company. Finnish metal 3D printing service provider Delva will use Euler’s tool to boost the efficiency of serial manufacturing with its EOS systems.
The show also saw Phase3D introduce a new version of Fringe, its metal 3D printing in-situ inspection platform, for cold spray additive manufacturing. Called Fringe Inspection: Cold Spray, the new tool was supported by $1.25 million from the Air Force Research Laboratory (AFRL).
Phase3D’s latest offering leverages structured light to capture surface data and measure each build layer, identifying defects such as cracking, cratering, and pitting. The software also evaluates the flatness and shape of deposited metal, allowing engineers and technicians to adjust parameters more effectively. Fringe Inspection: Cold Spray has already been tested by the University of Dayton Research Institute (UDRI) and evaluated in an operational environment at Ellsworth Air Force Base.
Fringe Inspection : Cold Spray attaches to the robotic control arm and scans cold spray deposits during the 3D printing process. Photo via Phase3D.
Away from 3D printing software, Hexagon’s upcoming Leica Absolute Tracker ATS 800 3D scanner seeks to enhance quality inspection and digitization in large-scale manufacturing. The new device stands out thanks to its impressive scanning reach, with the ATS 800 capable of capturing data at distances up to 40 meters. It combines direct scanning and reflector tracking technology to reduce the need for up-close scanning operations, which are impractical and unsafe for large-scale parts.
Joel Martin, Hexagon’s Director of Product Sales Management, explained that these capabilities are well suited to “anything that is big” in industries like aerospace, defense, shipbuilding, nuclear and wind energy production, and agriculture.
Martin emphasized that the ATS 800 stands out for its precise edge measurement capabilities. Most conventional scanners only capture the last point before dropping off an edge. However, Hexagon’s ATS 800 measures within the laser beam itself, not just at the surface contact point. This allows users to measure deep internal features that were previously unreachable. “Nothing else exists the way this thing does,” Martin said.
As the sun set on the final day in the Motor City, three themes stood out: collaboration, customer value, and applications. Zeif called it a “decisive moment” for 3D printing. Industry leaders agreed, arguing it’s time to move past the hype and integrate with broader manufacturing to reach market maturity.
The sun setting over Detroit. Photo by 3D Printing Industry.
Who won the 2024 3D Printing Industry Awards?
Subscribe to the 3D Printing Industry newsletter to keep up with the latest 3D printing news.You can also follow us on LinkedIn, and subscribe to the 3D Printing Industry Youtube channel to access more exclusive content.Featured image shows Huntington Place, Detroit. Photo by 3D Printing Industry.
0 Comentários
0 Compartilhamentos
73 Visualizações