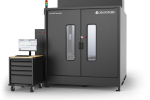
3DPRINTINGINDUSTRY.COM
3D Systems debuts new application-specific 3D printing solutions at RAPID + TCT 2025
3D Systems, the U.S.-based 3D printing pioneer headquartered in Rock Hill, South Carolina, has unveiled a trio of application-specific solutions at RAPID + TCT 2025 aimed at transforming manufacturing efficiency. The announcement includes the new Figure 4 135 platform for high-mix, low-volume production, a process-optimizing module for EXT Titan Pellet printers, and QuickCast Diamond, a build style for precision investment casting patterns using the PSLA 270 SLA system.
Flexible precision production with Figure 4 135
The Figure 4 135 system is engineered to address the growing demand for HMLV workflows in industries such as motorsports, furniture, electronics, and healthcare. Traditional injection molding is cost-effective only at scale and requires dedicated tooling for each part variant. By contrast, the Figure 4 135 enables rapid part production without tooling, supporting hundreds of part variations at high throughput and significantly lower cost.
The platform is paired with Figure 4 Tough 75C FR Black, a flame-retardant material rated UL94 V0 at thin wall sections (0.4 mm) with long-term thermal resistance of up to 150°C (electrical) and 130°C (mechanical). According to 3D Systems, this combination allows users to manufacture precise, production-grade parts such as electrical connectors, medical enclosures, and custom furniture hardware with repeatable quality and minimal post-processing.
By leveraging projector-based stereolithography and a high process capability index (CpK > 1.33), the Figure 4 135 is positioned to supplement or even replace injection mold tooling in demanding applications where accuracy, speed, and traceability are required.
3D Systems Figure 4 135. Image via 3D Systems.
Improving pellet extrusion efficiency with real-time control
For large-format and industrial-scale polymer applications, 3D Systems has introduced a new patent-pending module for its EXT Titan Pellet 1070 and 1270 printers. The add-on includes two main features; Part Solidity Optimization, which actively adjusts the extrusion flow rate to reduce voids and inconsistencies, improving internal part density and cutting machining time by up to 50%; and Print Bed Mapping, which Scans and maps the build surface in under 60 seconds, creating a numeric height map to guide leveling. This can reduce leveling time by 60% compared to prior methods.
The module is designed for additive manufacturing environments where EXT Titan printers are used to create jigs, fixtures, tooling, and production parts. It will ship standard on new EXT Titan Pellet systems with the optional milling spindle toolhead, and will be field-installable on existing machines starting Q3 2025.
Accelerating investment casting with QuickCast Diamond
QuickCast, first introduced by 3D Systems in the 1990s, helped establish 3D printing as a valuable tool in investment casting workflows. Now, the company has enhanced this capability with QuickCast Diamond, a new build style for its PSLA 270 printer that combines SLA precision with the high throughput and material flexibility of its Figure 4 systems.
Used to produce master patterns for metal casting in sectors like aerospace and energy, QuickCast Diamond enables the rapid design of sacrificial structures with excellent surface finish and no geometric limitations. When processed through 3D Systems’ 3D Sprint software, the PSLA 270 can quickly deliver mid-sized casting trees at a fraction of the time and cost of traditional tooling.
This feature aims to further reduce time-to-part and cost-per-part for manufacturers producing turbine blades, automotive impellers, and similar geometrically complex parts.
Dr. Jeffrey Graves, president & CEO, 3D Systems, emphasized the strategic nature of the releases, stating:
“Our historic R&D surge in 2024 yielded dozens of polymer and metal products, all driven by a rising demand to address an increasing number of applications using additive manufacturing. These new product introductions underscore our unwavering commitment to delivering application-specific solutions that address our customers’ rapidly evolving needs.”
3D Systems SLA metal part and 3D printed castnig pattern. Image via 3D Systems.
Adoption of high-mix, low-volume manufacturing
The additive manufacturing industry is increasingly pivoting toward HMLV production as companies seek more agile ways to respond to market variability, part customization, and supply chain challenges. Recent interviews with industry leaders, including HLH Rapid, highlight how manufacturers are adopting AM to bridge the gap between prototyping and scaled production without sacrificing speed or quality. Executive surveys published by 3D Printing Industry also confirm that flexibility, speed to market, and application-specific solutions are top priorities heading into 2025. Against this backdrop, 3D Systems’ latest solutions reflect an ongoing shift toward AM platforms that can deliver precision, repeatability, and cost efficiency across diversified product portfolios.What 3D printing trends should you watch out for in 2025?
How is the future of 3D printing shaping up?
Subscribe to the 3D Printing Industry newsletter to keep up with the latest 3D printing news.
You can also follow us onLinkedIn and subscribe to the 3D Printing Industry Youtube channel to access more exclusive content.
Featured image shows 3D Systems EXT 1070 Titan Pellet 3D printer. Image via 3D Systems.
Rodolfo Hernandez
Rodolfo Hernández is a writer and technical specialist with a background in electronics engineering and a deep interest in additive manufacturing. Rodolfo is most interested in the science behind technologies and how they are integrated into society.
0 Σχόλια
0 Μοιράστηκε
46 Views