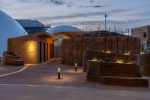
3DPRINTINGINDUSTRY.COM
WASP Powers 3D Printed Earthen Build at Expo Osaka
Aki Hamada Architects, a Japanese architecture studio, has developed a 3D printed rest facility using locally sourced soil for Expo 2025 in Osaka. Built with a Crane WASP Stand Alone system, the structure is part of a broader initiative that includes 20 rest stations designed by emerging Japanese architects selected through a national call. The facility integrates rest areas, toilets, a satellite studio, and a pop-up stage within a canyon-like architectural installation.
WASP, an Italian firm specializing in 3D printing technologies for architecture, provided the large-format construction printer used to fabricate key components of the facility. These included prefabricated exterior panels, planter-benches, modular earthen blocks, and cylindrical washbasins. All elements were produced using a soil-based mix composed of clay, straw, seaweed glue, pigments, and a magnesium oxide hardener. The formula was chosen for printability, mechanical performance, and its connection to Japan’s traditional earthen wall construction methods. Printed elements were cured for three days in a humid environment before air drying to achieve structural strength.
The 3D printed rest facility at Expo 2025 in Osaka. Photo via WASP.
“Through this project, we aim to present a glimpse of a future society in which humans, nature, and machines coexist—realized through architecture built with natural materials like earth and advanced robotics,” said Aki Hamada. As part of the design process, the team 3D scanned stone shapes from various regions across Japan, generating composite geometries. These forms were optimized through physical testing to ensure structural stability with soil alone and adjusted to respect overhang tolerances required for 3D printing. Panels were printed at a facility in Toyama, transported to the Expo site, and installed onto timber frames using pre-embedded wooden inserts.
The construction system, with a 6.2-meter diameter and 1.7-meter height build volume, was also deployed onsite to produce planter-benches that serve as rest spaces and tables. The resulting geometries included curved enclosures and clustered island forms, allowing visitors to rest in multiple configurations. Smaller stacked planters were constructed from 45 individually printed earthen blocks, some of which were filled with magnesium-based hardener and reinforced with bamboo rods in place of rebar. Washbasins were printed at the factory with recessed fronts for knee clearance and rear access panels for plumbing integration, then placed beneath pre-installed sinks and countertops.
Close-up of the earthen walls fabricated using a locally sourced soil mix. Photo via WASP.
Expo 2025 in Osaka is framed as a platform for future-oriented technologies and experimental architecture. Aki Hamada Architects used this opportunity to propose an alternative to industrial construction—where complexity arises from time, not cost, and materials are gathered directly from the local environment. All elements of the structure are biodegradable, reflecting a design intention for the installation to decompose naturally or be removed without contributing to long-term waste.
Recent developments in 3D printed architecture across Asia and the Middle East
Japan has recently accelerated its adoption of 3D printing in public infrastructure projects. In early 2025, West Japan Railway Company (JR West), in partnership with JR West Innovations and Serendix, announced plans to construct a new train station building at Hatsushima Station using a 3D printer. Designed as a compact, culturally integrated structure, the 6.3-meter-wide reinforced concrete station is expected to be assembled in just six hours between overnight train operations. This pilot aims to assess whether 3D printing can replace conventional steel and concrete methods in rural railway renewal, reducing construction time and labor costs while accommodating location-specific aesthetics.
In Dubai, large-scale architectural 3D printing also reached a milestone. Proto21, a UAE-based additive manufacturing firm, partnered with MYATA Platinum to build what has been officially recognized as the world’s largest 3D printed structure by volume. Finalized in February 2025, the project involved over 150 printers running continuously across three additive manufacturing technologies—FDM, SLA, and LfAM—to create more than 21,000 custom parts. Inspired by canyon formations, the project’s intricately modeled geometry demonstrated the capacity of 3D printing to bypass traditional manufacturing constraints, particularly in producing non-repetitive architectural components at scale.
Inside MYATA Platinum Dubai. Photo via: Proto21
Ready to discover who won the 20243D Printing Industry Awards?
Subscribe to the 3D Printing Industry newsletter to stay updated with the latest news and insights.
Featured image shows the 3D printed rest facility at Expo 2025 in Osaka. Photo via WASP.
Anyer Tenorio Lara
Anyer Tenorio Lara is an emerging tech journalist passionate about uncovering the latest advances in technology and innovation. With a sharp eye for detail and a talent for storytelling, Anyer has quickly made a name for himself in the tech community. Anyer's articles aim to make complex subjects accessible and engaging for a broad audience. In addition to his writing, Anyer enjoys participating in industry events and discussions, eager to learn and share knowledge in the dynamic world of technology.
0 Comentários
0 Compartilhamentos
28 Visualizações