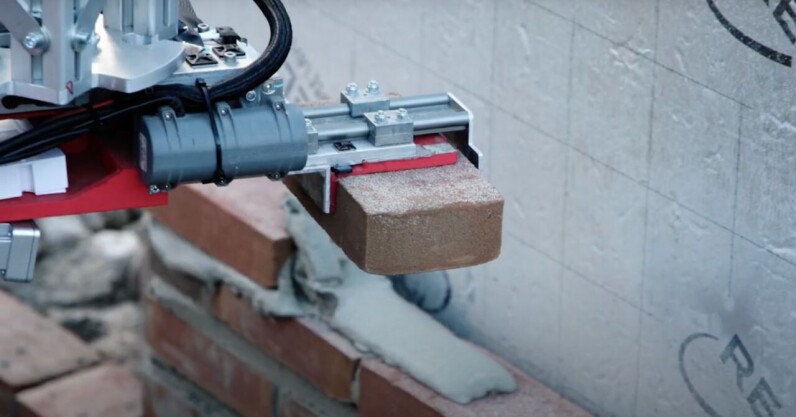
THENEXTWEB.COM
Can construction robots solve Europe’s housing crisis?
Europe’s housing crisis is deepening. High building costs, tight regulations, and labour shortages have choked the supply of affordable homes. As cities swell with new arrivals and construction workers retire en masse, the gap between supply and demand is only widening.
Endless solutions have been proposed. Mass housing projects, revamping the planning system, modular buildings, pre-fabricated materials, rent controls, and restrictions on corporate acquisitions of homes have all been explored with mixed success. But the shortage of affordable housing has only grown.
Dutch startup Monumental has pitched another fix: automation. The company is developing a suite of autonomous, electric robots that work on construction sites around the clock.
Salar al Khafaji, the startup’s CEO and co-founder, believes the tech can overcome the labour, cost, and regulatory hurdles crippling the industry.
The 💜 of EU techThe latest rumblings from the EU tech scene, a story from our wise ol' founder Boris, and some questionable AI art. It's free, every week, in your inbox. Sign up now!“It’s obvious that we need some forms of automation and robotics to solve these problems,” he tells TNW. “There’s almost no other way around it.”
At TNW Conference on June 19-20 in Amsterdam, al Khafaji will share his tips on building a thriving robotics business. Ahead of his talk, he outlined his vision of the future of construction.
Why construction has stagnated
Before launching Monumental in 2021, al Khafaji cofounded a visualisation startup called Silk. When Silk was acquired by US analytics giant Palantir in 2016, he began pondering his next venture. His plan was to focus on a major global challenge.
“I wanted to solve a serious problem in society,” he says. “And I became obsessed with construction and infrastructure.”
Al Khafaji was stunned to see so little technological progress in the industry. The built world in which we live, work, and play had become severely restricted as a result. His focus turned to a central problem: a productivity collapse in construction.
Labour shortages, strict regulations, and high costs, he feared, were worsening the housing crisis. New developments had become eye-wateringly expensive and painfully slow to construct. They also often result in unpopular buildings.
The past offers unflattering comparisons. The Empire State Building, for instance, was completed in 1931 after just 410 days. Eighty-four years later, 432 Park Avenue took 1,500 days — and became infamous for leaks, malfunctions, and a divisive design.
The problem extends beyond landmark buildings. Construction of standard homes has also lost pace. The average time taken to build a single-family house went from 4.8 months in 1971 — the earliest year with data available — to seven months in 2019. Even after scaling this to account for the growth in average house size, the process is still slower today.
Longer projects also bring higher costs, with labour often forming the bulk.
“It’s very, very labour-intensive because we’ve barely automated anything there,” al Khafaji says.
Monumental is his attempt to overhaul the status quo.
Credit: MonumentalAl Khafaji (right) and Monumental co-founder and CTO Sebastiaan Visser. Credit: Monumental
Tackling the housing crisis
Al Khafaji founded Monumental in 2021 alongside his long-term business partner, Sebastiaan Visser, who serves as the company’s CTO.
Their big idea was automating on-site construction with robotics and software. They began by building a prototype robotic crane, which evolved into autonomous ground vehicles that carry building materials around a construction site.
The first finished system off the production line focused on one crucial construction craft: bricklaying. It was a logical starting point.
Bricklaying is a skilled but physically demanding and sometimes dangerous job with a rapidly dwindling workforce. In 2022, researchers found that 19 European countries had a shortage of bricklayers, which made it the occupation with the biggest labour scarcity. As a result, construction projects suffer from delays and increased costs.
With the profession struggling to attract young talent, the shortage of workers is only set to grow. In the UK, the number of bricklayers recently hit a 25-year low, and a third of them are forecast to retire within the next decade.
Monumental’s systems aim to fill the gap — and, ultimately, strengthen the supply of affordable housing.
The startup’s electric bricklayer robots work autonomously alongside humans. Using sensors, computer vision, and small cranes, the machines precisely lay bricks and mortar in walls.
The system also integrates with existing construction processes — a crucial requirement in an industry that isn’t always open to new technologies.
The robot builders
Al Khafaji compares the robots to distributed computers. Composed of multiple, interconnected modular components, they function like network devices.
To prepare the machines for construction jobs, the startup’s software models both the site and the robots themselves. A machine vision stack then allows them to localise in the building zone. While they work, AI coordinates their tasks.
“We really think of it as an operating system for construction sites,” al Khafaji says. “We’re trying to make construction more software-defined.”
In 2023, the robots completed their first large-scale, 15-metre wall. Since then, the machines have built facades for houses, canal retaining walls, and other structures that stand across the Netherlands today.
Investors have been impressed by the progress. Last year, Monumental raised $25mn in seed funding to bring the concept closer to reality. But the company still has to win over the construction industry.
Labour’s role in the housing crisis
Across construction sites, many labourers’ tasks have changed relatively little over recent decades. Bricklayers, for example, continue working in much the same way. Shipyard workers, by contrast, have had their jobs transformed — if not replaced — by containerisation and automated pickers.
Al Khafaji was shocked by construction’s lack of innovation. “It doesn’t feel like enough time, money, or talent is flowing there… It’s the industry with the most stagnation,” he says. “Construction basically works the same way as a century ago.”
It’s a curious inertia given the size of the industry. Construction employs over 100 million people and accounts for about 13% of global GDP. Yet the sector still can’t come close to matching demand. Take the Netherlands. In 2020, the Dutch government set a goal of building 1 million new homes – two-thirds of them affordable — within a decade. Since then, the country has consistently fallen short of the target.
Automation and digital tools could bring enormous benefits on building projects. But construction firms have historically been reluctant to adopt them.
The industry is typically cautious of new technologies for fundamentally logical reasons. Businesses often operate on boom-and-bust cycles, prioritising financial reserves over long-term investments in new, unproven ideas. Costs are enormous, project cycles are extremely long, and project margins low, fostering conservative and risk-averse strategies.
“No one wants to take a bet,” al Khafaji says. “Imagine if you were to build your own house for your family… Are you gonna take a bet on a new material that no one has tried before or a process that no one has done before?”
Monumental hopes to ease the industry’s concerns.
The robot march towards building sites
The company offers services in ways that are familiar to construction projects. Quotes are offered in common market terms, such as per square metre or brick. Standard materials are used, supply chains are conventional, and clients aren’t asked to do CapEx investments.
Instead, they can simply tell Monumental which bricks and mortar they desire and the company will construct the project. At any point, they can also swap the technology out for human masons.
“We’re not selling them robots,” al Khafaji says. “We’re not selling them software licenses… We’re selling them a wall.”
But bricks on walls are just the start of Monumental’s plans. The company plans to apply robotics to numerous building tasks.
“A brick is just a building block,” al Khafaji says. “You could imagine the brick being different things — concrete blocks, window frames, door frames, roofing elements. All these things, you grab them, hold them, and put them in a different place.”
Monumental estimates that these functions account for a third of the tasks on a construction site. As the technology evolves, autonomous machines could take on even more building jobs.
Al Khafaji has grand visions for the future.
“That’s an almost science fiction version of this, where everything is automated,” he says. “You could imagine electric robots coming in for just a couple days and silently building beautiful structures in a very short amount of time — with limited pollution and more safety.”
It’s a long way from laying bricks, but the foundations are already being set — one robot at a time.
Salar al Khafaji will be among the standout speakers at TNW Conference, which takes place on June 19-20 in Amsterdam. Tickets are now on sale — use the code TNWXMEDIA2025 at the checkout to get 30% off the price tag.
Story by
Thomas Macaulay
Managing editor
Thomas is the managing editor of TNW. He leads our coverage of European tech and oversees our talented team of writers. Away from work, he e
(show all)
Thomas is the managing editor of TNW. He leads our coverage of European tech and oversees our talented team of writers. Away from work, he enjoys playing chess (badly) and the guitar (even worse).
Get the TNW newsletter
Get the most important tech news in your inbox each week.
Also tagged with
0 Commentaires
0 Parts
26 Vue