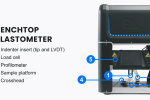
3DPRINTINGINDUSTRY.COM
ASTRO America Deploys Plastometrex Technology to Accelerate Mechanical Testing in Additive Friction Stir Deposition
ASTRO America, a nonprofit research institute focused on manufacturing policy and technology in aerospace and defense, has integrated Plastometrex’s PLX-Benchtop system into its additive friction stir deposition (AFSD) workflows. The goal is to accelerate mechanical characterization of materials during parameter development. Plastometrex, a UK-based company founded by scientists from the University of Cambridge, develops mechanical testing systems that extract stress-strain data using non-destructive indentation techniques. Since adoption began, ASTRO has run several hundred tests with the PLX-Benchtop to assess aluminum alloys processed via MELD’s solid-state 3D printing technology.
Profilometry-based Indentation Plastometry (PIP) technology, central to Plastometrex’s platform, offers a cost-effective alternative to traditional tensile testing by providing accurate stress-strain curves within minutes. “The ability to conduct fast, non-destructive mechanical testing with PIP has significantly improved our approach to material optimization,” explained Noah Barnhill, Vice President, Army Operations at ASTRO America. “We can now evaluate mechanical properties in real time, making data-driven decisions about process parameters without the delays and material constraints of conventional testing methods.” Employing PIP-based testing allows ASTRO to identify the influence of various print parameters in ways that would be cost-prohibitive using conventional methods. Notably, the PLX-Benchtop enables assessment of part homogeneity directly on finished parts, bypassing the extraction challenges of destructive sample testing.
Plastometrex and ASTRO America partnership for rapid additive manufacturing testing. Image via Plastometrex/ASTRO America.
Mechanical testing typically presents a bottleneck in additive manufacturing research. Plastometrex’s platform changes this dynamic by allowing direct, localized analysis of 3D printed components. As Dr. Mike Coto, Chief Commercial Officer at Plastometrex, described, “ASTRO’s use of the PLX-Benchtop demonstrates how rapid, cost-effective mechanical testing can unlock deeper insights into process optimization, material performance, and component reliability – without the cost and time barriers of traditional tensile testing.” PIP enables the mapping of stress-strain curves through three distinct steps: creation of a controlled indent in the test sample, detailed 3D measurement of the indent’s residual profile, and inverse finite element analysis to extract plasticity parameters from the measured shape. An individual test is completed in less than five minutes, returning detailed data on yield strength, work-hardening, ultimate tensile strength, and uniform elongation.
Testing begins with a spherical indenter, typically between 0.5 and 1 millimeter in radius, pressed into the alloy surface to create an indent of 100–200 microns depth. PIP’s use of larger indents compared to micro- or nano-indentation means test results reflect the response of the material’s bulk rather than a single grain. After indentation, either a stylus profilometer or interferometer measures the full 3D profile of the residual indent. Data from this scan is then compared against computational models, with iterative updates until the best match is found. This approach yields a full stress-strain curve with a fraction of the time, cost, and material waste associated with traditional testing protocols.
Plastometrex’s PLX-Benchtop platform. Image via Plastometrex.
ASTRO America’s Role in Standardization and Investment for Additive Manufacturing
Earlier in April, ASTM International, a leading organization for technical standards, began a three-year collaboration with ASTRO America focused on establishing comprehensive qualification frameworks for AFSD. This project, titled “Advancement of Process, Materials, Applications, and Test and Evaluation for Large-Scale Additive Manufacturing,” is structured in five technical phases and targets improvements in equipment control, facility setup, feedstock parameters, and process operations. ASTM’s Additive Manufacturing Center of Excellence (AM CoE) plays a key role, overseeing stakeholder workshops and implementing a dedicated Quality Management System for process characterization and metrology.
Parallel to technical standardization, ASTRO America has helped secure new capital resources aimed at accelerating additive manufacturing adoption among small and medium-sized manufacturers. The organization’s AM Forward initiative recently achieved federal approval for its private equity vehicle, the Stifel North Atlantic AM-Forward Fund, under the U.S. Small Business Administration’s Critical Technology initiative. This fund is designed to address persistent barriers such as capital access, machine qualification, and workforce training, with backing from major industrial partners including Lockheed Martin, GE Aerospace, and ASTM International. AM Forward’s mandate is to increase the presence of metal 3D printing throughout U.S. supply chains by offering tailored financial structures and strategic mentorship to companies contributing to national defense and advanced manufacturing.
ASTM Center of Excellence Logo. Image via ASTM.
Ready to discover who won the 2024 3D Printing Industry Awards?
Subscribe to the 3D Printing Industry newsletter to stay updated with the latest news and insights.
Featured image showcase Plastometrex’s PLX-Benchtop platform. Image via Plastometrex.
Anyer Tenorio Lara
Anyer Tenorio Lara is an emerging tech journalist passionate about uncovering the latest advances in technology and innovation. With a sharp eye for detail and a talent for storytelling, Anyer has quickly made a name for himself in the tech community. Anyer's articles aim to make complex subjects accessible and engaging for a broad audience. In addition to his writing, Anyer enjoys participating in industry events and discussions, eager to learn and share knowledge in the dynamic world of technology.
0 Commentarii
0 Distribuiri
38 Views