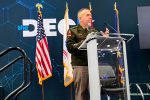
3DPRINTINGINDUSTRY.COM
RAPID + TCT 2025 3D Printing for Defense: New Insights from the U.S. Army, BlueForge Alliance, Boeing, and More
Aerospace and defense now rank among the largest and most valuable sectors adopting additive manufacturing.
Ongoing international supply chain disruptions, rising geopolitical tensions, and global conflicts threaten access to critical equipment and components vital for national security. In response, defense agencies are turning to 3D printing to cut lead times, localize production, repair equipment, and restock depleted inventories.
This growing focus on 3D printing for defense was evident at RAPID + TCT 2025, which co-located with the eighth edition of SME’s AeroDef Manufacturing 2025 expo. A large section of the show floor at Detroit’s Huntington Place was dedicated to key exhibitors within the military technology ecosystem. This included heat exchanger manufacturer Conflux Technology, aerospace 3D printing firm Hyphen Innovations, and US defense manufacturing accelerator LIFT.
Read more RAPID + TCT 2025 news and executive insights
AeroDef also featured a stacked conference track. Expert-led presentations and panels provided insights into the value, opportunities, and challenges facing the defense industrial base.
Major General Michael Lalor of the U.S. Army highlighted 3D printing’s role in sustaining 70% of the infantry’s combat inventory. He also emphasized its importance for building an “arsenal of democracy” in Detroit.
RHH Advisory’s Tali Rosman identified 3D printing’s potential to increase the pace of American manufacturing. This is particularly significant given that China’s shipbuilding capacity is currently 350 times greater than that of the United States. A BlueForge Alliance-led panel discussed how to accelerate production in the U.S. Navy’s industrial base, highlighting the value and challenges surrounding 3D printing adoption.
Elsewhere, Dr. Bill Anderson highlighted the cybersecurity threats that malicious foreign actors pose to the digital ecosystem of additive manufacturing. Boeing’s Daniel Braley was also on the agenda. He highlighted vulnerabilities in the supply chain for critical minerals and materials, citing the “threat of the U.S. going to full-scale war in one to two years.” As geopolitical tensions rise and global supply chains constrict, all speakers broadly agreed that 3D printing will become a critical strategic pillar in safeguarding the West’s defense industrial base.
The AeroDef Manufacturing 2025 expo show floor. Photo by 3D Printing Industry.
Major General Michael Lalor: Advanced manufacturing at U.S. Army TACOM
Major General Michael B. Lalor, Commanding General of U.S. Army Tank-automotive and Armaments Command (TACOM), opened the AeroDef conference with a welcome address. Headquartered at Detroit Arsenal, the Command manages 70% of the U.S. Army’s ground combat inventory. “If a soldier drives it, shoots it, or wears it, we sustain it,” Lalor explained.
TACOM oversees a $30 billion annual budget and manages over 3,500 weapon systems. According to the former M1A1 Tank Platoon Leader, these include everything from Abrams and Bradley tanks to eight-wheeled Stryker armored fighting vehicles and artillery systems. TACOM maintains a global presence. At any given time, about 350 personnel across 70 “flyaway teams” operate overseas, supporting supply chain operations for units in the field.
Collaboration with industry partners is vital for TACOM’s operations. He noted that technological evolution and supply chain complexities demand new levels of collaboration that transcend “international and traditional boundaries.” Lalor added that TACOM is leading the U.S. Army in advanced manufacturing. 3D printing is being leveraged to fabricate customized parts on demand, reducing reliance on lengthy lead times. TACOM’s Major General highlighted that the Command has seen “amazing results” through this adoption.
Over the past year, TACOM has developed its Battle Damage Repair and Fabrication Program (BDRF). The initiative leverages additive manufacturing to produce temporary replacement parts for damaged military vehicles. This reduces downtime and increases operational readiness, allowing critical warfighting equipment to be returned to the battlefield in less time.
Over 40,000 vehicle parts have been assessed for additive manufacturability in collaboration with the U.S. Army DEVCOM Ground Vehicle Systems Center and TACOM Integrated Logistics Support Center. From this, TACOM’s Rock Island Arsenal – Joint Manufacturing and Technology Center in Illinois has 3D printed more than 600 3D CAD models.
According to Lalor, these efforts are vital to relieving the substantial pressure on America’s few remaining foundries. The U.S. Army’s only operational foundry at Rock Island has seen its workload quadruple over the past 18 months amid a dearth of domestic castings and forgings capabilities.
Lalor revealed that Rock Hill Arsenal’s additive manufacturing technologies will be ASTM 9100 compliant by June 2025, when it will ramp up production of aerospace and aviation-certified parts. “There are gaps to close, and that arsenal is part of the solution,” he added.
Major General Michael Lalor speaking at AeroDef Manufacturing 2025. Photo by 3D Printing Industry.
The value of 3D printing for defense
In a separate presentation, Tali Rosman, a Business and M&A advisor at RHH Advisory and former Elem Additive CEO, shared her perspective on the defense opportunity for 3D printing.
Rosman emphasized the U.S. Department of Defense’s (DOD) growing adoption of additive manufacturing, suggesting that the Pentagon is “arguably the largest user” of additive manufacturing based on dollars spent. However, this adoption comes amid a challenging point for the Pentagon. According to Rosman, “China is outpacing the U.S. in terms of manufacturing.” Notably, she highlighted that China’s shipbuilding capacity is 350 times that of the United States.
Amid this threat, the DOD is adopting additive manufacturing “in earnest” to secure the U.S. defense supply chain. While it can take years to build conventional manufacturing plants, some 3D printing technologies can start fabricating parts in weeks. In today’s “volatile and uncertain world,” that speed makes the technology especially appealing.
Rosman highlighted expeditionary manufacturing as one key application for 3D printing. She emphasized that conflict in Ukraine has “paved the way” for its remote deployment. Ukrainian soldiers are leveraging metal additive manufacturing, including cold spray 3D printers from SPEE3D, to increase equipment uptime and localize critical supply chains.
The U.S. Navy has also installed 3D printers on warships to conduct repairs and fabricate replacement parts at the point of need. Last year, SPEE3D’s XSPEE3D and Snowbird Technologies’ SAMM Tech hybrid DED manufacturing system were deployed during the Rim of the Pacific (RIMPAC) exercise in Hawaii. During the trial, Navy personnel sought to reduce the delivery time of critical parts from days to hours.
Additionally, Rosman highlighted increased DOD funding to restock its depleted missile arsenals using 3D printing. She pointed to Albuquerque-based aerospace firm X-Bow Launch Systems, which recently received an additional $9.85 million from the DOD to advance research into 3D printed solid rocket motors (SRMs). This new capital sees the company’s current DOD contract value rise to $28.67 million, while its total U.S. defense funding has exceeded $97 million.
Similarly, the Pentagon has backed Ursa Major to 3D print missile SRMs. Last December, the Colorado-based firm completed successful flight testing for the U.S. Army. Daniel Jablonsky, Ursa Major’s CEO, claimed that the company’s Lynx 3D printing technology unlocked “unprecedented timelines,” with nearly 300 SRM static test fires completed in 2024.
Looking ahead, Rosman anticipates that 3D printing will play an increasing role for many of America’s allies. European countries are expected to ramp up defense funding, following the Trump administration’s call for increased security spending among NATO members. For instance, Germany’s defense spending could grow to 3% of GDP by 2027, potentially exceeding 3.5% after that, according to Goldman Sachs research.
Rosman believes a “disproportionate” amount of Europe’s funding will be “flowing into the additive manufacturing sector” in the coming years. Indeed, the UK recently outlined plans to accelerate 3D printing for defense. The Ministry of Defense (MOD) aims to increase investment to incentivise adoption, adapt policies to remove barriers, and increasingly integrate additive manufacturing into the defense supply chain.
Snowbird Technologies’ 3D printer at RAPID + TCT 2025. Photo by 3D Printing Industry.
Additive manufacturing bolsters the US Navy’s industrial base
The role of additive manufacturing in the U.S. submarine industrial base (SIB) is also growing. Leading this effort is BlueForge Alliance (BFA), a nonprofit defense integrator. Headquartered in Bryan, Texas, BFA coordinates manufacturing, recruitment, and technology integration to support the U.S. Navy’s manufacturing supply chain.
During a panel discussion, Tim Shinbara, BFA’s Chief Strategy Officer, sat down with James Hockey, Director of metal 3D printing service provider Incodema3D, and Greg Mallon, Chief Strategy Officer of engineering and manufacturing firm GSE Dynamics. Incodema3D and GSE Dynamics are among the roughly 16,000 companies working in America’s ship and submarine manufacturing sector.
Mallon identified workforce challenges as stunting the growth of America’s maritime industrial base. He noted that over the past 30 years, the U.S. has shifted from a goods-based economy to one driven by digital and service industries. The result? A shrunken manufacturing workforce, down from 3 million to just over a million workers. “That has left the defense industrial base very atrophied,” Mallon added.
Additive manufacturing firms, like Incodema3D, are no less affected. “Our biggest problem is still talent,” agreed Hockey. “We can’t hire people fast enough.” The 27-year 3D printing veteran explained that Incodema3D needs to be growing 25% every year “just to keep up with the scaling we’ve already done.” However, the company, which operates out of Freeville, New York, has only grown 30% since its founding in 2013.
BluForge Alliance is working to alleviate these shortfalls through buildsubmarines.com, a website that connects workers with employers in the submarine industrial base. According to Shinbara, the recruitment tool offers a low-cost and effective solution to workforce challenges. “It’s only eight cents for someone to apply, and we found it’s about $700 per person to be hired,” he explained.
Buildsubmarines.com sign in Detroit. Photo by 3D Printing Industry.
Adoption also remains a core challenge within maritime manufacturing. In particular, Hockey identified the need for customers to embrace design for additive manufacturing (DfAM) and understand where the value lies.
He highlighted a common issue with additive manufacturing: the assumption that it’s always the faster solution. Specifically, customers are increasingly requesting low-volume casting for legacy parts. Hockey explained that these applications offer little value unless the design includes novel geometries or features enabled by 3D printing.
For Mallon, the roadblocks to adoption go beyond the machinery, citing “a lack of enthusiasm to adopt that new technology.” He highlighted a “resistance to change” among experienced workers, often due to job security concerns or comfort with legacy systems. However, there is stronger enthusiasm for 3D printing among younger workers, who “embrace the technology much faster.”
Looking to the future of maritime manufacturing, Mallon believes hope lies in predictable defense programs and automation. “When you look at the Navy’s 30-year shipbuilding plan, each year it changes,” he said. “It’s hard to follow.” Mallon believes increased predictability would allow customers to follow through on programs and prioritize execution. Moreover, GSE Dynamics’ Chief Strategy Officer believes increased automation will improve efficiency and speed.
Hockey echoed this sentiment, highlighting his company’s internal push for tighter integration between additive manufacturing and CNC machining. Hockey predicted that streamlined workflows will ease staffing pressures while also elevating the overall skill level of the workforce.
Shinbara, surveying the broader context from Washington, D.C., concluded with a hopeful note. “The policy, posture, and funding are starting to align,” he said. “It’s probably one of the few times outside of World War Two” that the U.S. has seen this level of policy and financial momentum.
Tim Shinbara, Greg Mallon, and James Hockey (L-R). Photo by 3D Printing Industry.
Cybersecurity threats and logistical challenges
Security threats and supply chain challenges also jeopardize adoption and growth. Dr. Bill Anderson, Principal Product Manager at Mattermost, underscored major cybersecurity concerns. He pointed to the risks tied to additive manufacturing’s expanding digital footprint.
Anderson opened his presentation with a stark warning: “The government is under attack from foreign adversaries.” He emphasized that government suppliers, contract manufacturers, and OEMs face significant risk.
The digital security expert observed that even manufacturers far from the front lines are under threat, warning, “You’re being attacked now, you probably just don’t know it.” The University of Waterloo alumnus explained that, in wartime, the West’s adversaries may look to shut down suppliers’ systems. This could have knock-on effects, impacting the military and government’s ability to operate.
According to Anderson, about 70% of cyberattacks on the defense industrial base are committed by nation states. He pointed to China as a major threat, particularly Volt Typhoon, reportedly a Chinese state-sponsored hacker group engaged in cyberespionage. In 2023, this advanced persistent threat (APT) breached commercial and Navy networks near Guam. While the U.S. successfully thwarted the intrusion, the attack could have severed communications across the Pacific. Such a capability would carry serious strategic consequences, particularly amid escalating tensions over Taiwan.
Security threats also impact the supply of critical materials. Braley, a Technical Fellow at Boeing, described the global supply chain as a “perfect storm.” He explained that intensifying threats from Russia, North Korea, China, and Iran have “severely affected” America’s ability to procure raw materials and manufactured parts.
Tightening U.S. and international regulations constrain the flow of materials essential to America’s defense manufacturing. According to Braley, “the real issue for the aerospace industry” lies in recent amendments to the National Defense Authorization Act (NDAA), which introduce new import restrictions.
Braley noted that most titanium powder used in metal 3D printing is sourced from China. Under the updated NDAA, the DOD could be barred from procuring Chinese titanium powder starting in June 2026. The legislation will also restrict imports of key steel and metal alloys, including nickel, iron, cobalt, zirconium, and their derivatives.
Braley is especially concerned about magnesium, which he says has “trace elements in almost everything.” Since “the vast majority of magnesium comes from China,” he warned that the restrictions will “drastically affect just about every product we make in the US.”
Dr. Bill Anderson at AeroDef Manufacturing 2025. Photo by 3D Printing Industry.
The future of 3D printing for defense
Despite these concerns, additive manufacturing is rapidly becoming a vital asset for defense applications. It offers value in strengthening supply chains, enhancing combat capabilities, reducing lead times, and replenishing depleted weapon stockpiles. The Pentagon has taken note, committing significant investment to scale domestic 3D printing capacity and cultivate a resilient network of additive manufacturing suppliers.
Rosman highlighted the growing market opportunity for 3D printing in defense, citing data from Additive Manufacturing Research (AM Research). In its 2024 report, the New York-based firm projected that DOD spending on 3D printing will exceed $1 billion in 2025, up from $800 million last year. U.S. investment is projected to rise steadily through the decade, reaching $2.6 billion by 2030.
These findings align with the views shared by speakers in Detroit. As geopolitical tensions and security concerns intensify, 3D printing is poised to play a larger role in strengthening global defense capabilities. While Europe is expected to ramp up adoption in the coming years, the United States is already investing heavily to secure a leading position in the additive manufacturing landscape. While challenges persist, increased collaboration between state and industry seems set to accelerate additive manufacturing adoption within America’s defense industrial base.
DOD 3D printing spending growth projections. Image via Additive Manufacturing Research.
Read all the 3D printing news from RAPID + TCT 2025.Who won the 2024 3D Printing Industry Awards?
Subscribe to the 3D Printing Industry newsletter to keep up with the latest 3D printing news.You can also follow us on LinkedIn, and subscribe to the 3D Printing Industry Youtube channel to access more exclusive content.Featured image shows Major General Michael Lalor speaking at AeroDef Manufacturing 2025. Photo by 3D Printing Industry.
0 التعليقات
0 المشاركات
36 مشاهدة