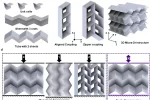
3DPRINTINGINDUSTRY.COM
University of Houston Develops 3D Printed Ceramic Origami Structures for Biomedical and Aerospace Applications
A research team at the University of Houston has developed a new method for fabricating flexible, damage-resistant ceramic structures by integrating origami-inspired geometries with a biocompatible elastomeric coating. The approach leverages 3D printing to produce complex Miura-ori ceramic architectures, which are then coated with polydimethylsiloxane (PDMS), a hyperelastic silicone polymer. The result is a class of brittle materials that exhibit significant improvements in energy absorption and failure tolerance.
The project was led by Maksud Rahman, assistant professor in the Department of Mechanical and Aerospace Engineering, with key contributions from postdoctoral fellow Md Shajedul Hoque Thakur. Their findings were published in the journal Advanced Composites and Hybrid Materials, providing a comprehensive account of the experimental procedures, material modeling, and mechanical testing of the ceramic origami structures.
University of Houston’s engineering team designed and fabricated Miura-ori ceramic structures using slurry-based stereolithography, a 3D printing process that utilizes a silica-filled resin and ultraviolet light to build complex, high-resolution forms. The intricate origami patterns were chosen for their unique mechanical advantages, including multistability, tunable stiffness, and auxetic behavior. After printing, the components underwent a series of cleaning and drying steps, followed by multi-stage thermal sintering at temperatures up to 1271 °C. This process removed the polymer binder and fused the silica particles, resulting in a dense, load-bearing ceramic with a final density of nearly 50 percent.
To ensure dimensional accuracy after sintering shrinkage, the research team adjusted the digital design files—generated using MATLAB and SolidWorks—prior to printing. Scanning electron microscopy (SEM) confirmed successful densification and grain boundary development within the finished ceramic lattice.
The assembly of the origami structure and the directions for performing compression tests. Image via Springer Nature Link.
The origami ceramics were coated with a thin layer of polydimethylsiloxane (PDMS), a widely used biocompatible silicone elastomer to impart flexibility. The team used a vacuum-assisted dip-coating procedure, curing the PDMS in two steps to achieve a uniform thickness of 75 to 100 microns. SEM cross-sections showed that the elastomer coating covered all surfaces and creases of the structure, while remaining superficial and not infiltrating the ceramic core. Volume analysis estimated that 91 percent of the composite consisted of ceramic, closely mirroring the structure of natural nacre, which uses brittle/soft layering to enhance toughness.
Mechanical Testing Across Three Axes
Compression tests were performed on both coated and uncoated origami samples in three orthogonal directions, using an Instron ElectroPuls E3000 system. Load-deflection measurements revealed that uncoated ceramics failed catastrophically at low strains, particularly along their weakest axis. In contrast, PDMS-coated samples absorbed significantly more energy before failure. The weakest loading direction showed the largest relative improvement in toughness—an effect attributed to the compartmentalized failure enabled by the elastomeric layer, which prevented cracks from propagating through the entire structure at once.
SEM imaging further illustrated that the coating stopped or slowed crack growth, resulting in a stepwise, localized failure mode rather than the sudden collapse typical of ceramics. Optical images taken at various stages of compression confirmed that coated origami maintained structural integrity at strains that destroyed uncoated samples.
Finite element analysis was performed using ABAQUS/Explicit, with material models tailored to both the ceramic (concrete damaged plasticity) and the hyperelastic PDMS coating (Arruda–Boyce model). Element deletion routines were employed to accurately simulate fracture and separation. Simulation results closely matched experimental findings, revealing lower stress concentrations and delayed damage accumulation in coated samples. Mesh convergence was verified, with final models containing nearly 300,000 elements to ensure numerical stability.
Fabrication of the 3D-printed ceramic Miura-ori structure, followed by the application of a hyperelastic coating. Image via Springer Nature Link.
Analysis of von Mises stress and maximum principal strain showed that the PDMS layer redistributed loads away from vulnerable edges and vertices. The presence of the coating reduced both tensile and compressive damage variables, with the largest reduction seen in the direction most susceptible to crack initiation.
Cyclic Loading Shows Durability Under Repeated Strain
Researchers further evaluated the coated ceramics under cyclic loading in the X-direction, up to a compressive strain of 1.5 percent. Uncoated structures failed at or below this threshold, but PDMS-coated samples endured multiple loading cycles with only minor reductions in peak force—evidence of crack bridging and controlled damage. Simulation of cyclic loading confirmed this trend and provided additional insight into the evolution of damage over time.
The team’s approach demonstrates that combining complex origami geometries with 3D printed ceramics and hyperelastic coatings can yield macroscale structures with application-specific mechanical properties. By tuning both geometry and material composition, University of Houston engineers have created a pathway toward lightweight, tough, and biocompatible materials suitable for prosthetics, implants, impact-resistant aerospace parts, and robotic systems.
Future work will focus on further optimizing Miura-ori unit cell parameters using algorithmic design and simulation to maximize performance under specific loading conditions. The team anticipates that advanced optimization techniques—such as Bayesian methods or genetic algorithms—will enable the rapid identification of optimal design configurations for new engineering challenges.
Results of the experimental quasi-static compression test on the architected ceramic structure. Image via Springer Nature Link.
Ready to discover who won the 2024 3D Printing Industry Awards?
Subscribe to the 3D Printing Industry newsletter to stay updated with the latest news and insights.
Featured image showcase the assembly of the origami structure and the directions for performing compression tests. Image via Springer Nature Link.
Anyer Tenorio Lara
Anyer Tenorio Lara is an emerging tech journalist passionate about uncovering the latest advances in technology and innovation. With a sharp eye for detail and a talent for storytelling, Anyer has quickly made a name for himself in the tech community. Anyer's articles aim to make complex subjects accessible and engaging for a broad audience. In addition to his writing, Anyer enjoys participating in industry events and discussions, eager to learn and share knowledge in the dynamic world of technology.
0 Commenti
0 condivisioni
20 Views