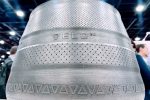
3DPRINTINGINDUSTRY.COM
Velo3D’s New Direction: Arun Jeldi on His First 90 Days as CEO and Future Roadmap
At RAPID + TCT 2025, I spoke with Dr. Arun Jeldi to discuss his first four months at the helm of Velo3D. He outlined a revised strategic direction as the new-look company plots a path to profitability.
In January 2023, Velo3D launched a strategic review after a stretch of financial and regulatory setbacks. One year later, amid a NYSE noncompliance notice and declining revenue, the Californian company ceded 95% of its shares to Arrayed Additive. The transaction prompted a leadership change, with Jeldi, Arrayed’s chief executive, replacing Brad Kreger as Velo3D’s CEO. In the re-shuffle, Kreger was made Chief Operating Officer.
Standing in the Velo3D booth at Detroit’s Huntington Place exhibition center, Jeldi outlined his journey from healthcare to entrepreneur and 3D printing executive. An NTR University of Health Sciences graduate, Jeldi has built a substantial portfolio within the manufacturing sector. Besides Velo3D and Arrayed Additive, he leads magnesium manufacturing firm Lite Magnesium Products and magnesium extraction specialist Crown Magnesium Inc.
Since becoming Velo3D CEO, Jeldi has charted a new course for the Fremont-based metal 3D printer OEM. The company’s new Rapid Production Services (RPS) offering shifts the business beyond machine sales, aiming to provide scalable metal additive manufacturing capabilities.
Jeldi explained his goal to achieve financial stability and ensure the firm is “moving in the right direction” by addressing customer demand. According to the new CEO, his first 90 days at Velo3D have exceeded all expectations, with “a lot more demand than we expected.” He also shared insights into the value of 3D printing for defense, aerospace, and space applications and revealed plans to build a new factory in the American Midwest.
Read more RAPID + TCT 2025 news and executive insights
A part 3D printed using Velo3D’s Sapphire technology on display at RAPID + TCT 2025. Photo by 3D Printing Industry.
Velo3D’s financial challenges
Jeldi’s priority in his first 90 days as CEO was to chart a “new direction” for Velo3D. Previously, the Californian firm prioritized manufacturing and selling 3D printers to generate revenue. This approach guided the development of its Sapphire range of metal laser powder bed fusion (LPBF) systems, including the Sapphire 1MZ and Sapphire XC 3D printers.
Velo3D’s products stand out thanks to their non-contact recoater technology. Most LPBF systems incorporate recoater blades that physically spread metal powder material across the build plate. This can create defects and inhibit design complexity. Velo3D’s recoated blades are suspended above the powder bed and use controlled air to spread material, reportedly unlocking more complex geometries and enhancing build quality.
Despite these advantages, Velo3D machine sales alone have struggled to sustain the company’s cash flow. The firm saw its revenue decline YoY in each quarter of 2024. FY 2024 revenue dropped 47.1% YoY from $77.4M to $41.0M. Additionally, dipping Velo3D stock prices caused the firm to receive two NYSE noncompliance notices in as many years. While Velo3D posted a -$82.3M operating loss in FY’24, this figure improved by 38.2% from -$133.3M the previous year. Adjusted EBITDA, net loss, and gross margin are also moving in the right direction.
Meanwhile, Nikon SLM Solutions, a key competitor in the market, has capitalized on growing demand. Last year, Lockheed Martin opened a 16,000-square-foot additive manufacturing facility featuring multiple SLM NXG 3D printers. Nikon’s quarterly earnings consistently cite rising interest in its large-format 3D printers, particularly from clients in the aerospace, space, and defense sectors. In FY 2024, Nikon’s Digital Manufacturing segment, which includes Nikon SLM, reported a 42.4% year-on-year revenue increase to ¥59.9 billion, driven by expanded 3D printer sales.
The Sapphire XC 1MZ. Photo via Velo3D.
A Strategic Pivot at Velo3D
Jeldi has shifted Velo3D’s strategic approach to remain competitive, removing its reliance on 3D printer sales. He noted that the company “had a different view on the market before,” but has now transitioned with a new focus on “real strategy and financial stability.”
At the heart of this strategy is Velo3D’s newly launched RPS offering. Introduced last month, RPS gives customers access to Velo3D’s production cells, allowing them to scale manufacturing without significant capital investment. The service targets rising demand in the U.S. for flexible, scalable, and localized production, particularly from aerospace, defense, and energy customers. Jeldi also revealed that his company is actively working with 3D printing material and metal feedstock suppliers to improve vertical integration and “create an ecosystem for our customers to be successful.”
Through the RPS workflow, Velo3D collaborates with clients to develop solutions tailored to their application needs, promising shorter design cycles and faster qualification. Metrology software, 3D printing process control tools, and data-driven analysis are integrated to enhance part reliability, output predictability, and certification at Velo3D’s production hubs.
In a Velo3D press release, an unnamed “leading aerospace engine manufacturer” stated, “RPS achieved more in four months than we were able to accomplish in the previous four years.” The firm reportedly used Velo3D’s new service to produce 11 large-format proof-of-concept parts using three materials, moving two into its production pipeline. It also claims to have made “substantial progress” in qualifying IN718 material.
The Velo3D booth at RAPID + TCT 2025. Photo by 3D Printing Industry.
3D printing for aerospace, space, and defense
Demand for Velo3D’s revamped operations has surged, according to Jeldi. The company had expected a “10% or 20% increase in orders” by the third or fourth quarter. However, within the first 90 days of 20253, orders had doubled. “It’s clear that there’s a lot more demand than we expected,” Jeldi said.
According to Velo3D’s new CEO, this unexpected uptick in orders has been driven by growing demand in 3D printing for defense, space, and aerospace applications. These sectors increasingly require rapid prototyping capabilities and a high-mix of complex geometries in small volumes. “Space is booming. Ammunition is booming,” explained Jeldi. This growth comes amid a challenging international geopolitical environment, with America’s security and aerospace organizations seeking more secure and localized supply chains.
For instance, under a week after our conversation, Velo3D signed a five-year, $15 million master services agreement (MSA) with U.S. commercial space company Momentus, Inc. The deal will see Jeldi’s company provide consulting and part fabrication services through its RPS offering, accelerating the production of space systems components.
Momentus plans to use these 3D printed components in its satellites, Orbital Service Vehicles, and other space systems. According to the San Jose-based firm, Velo’s LPBF technology will unlock more optimized designs, lower production costs, enhance part reliability, accelerate prototyping, and open new revenue streams
Velo3D’s new leader believes the key advantage of additive manufacturing for defense lies in its ability to accelerate the transition between concept, design, prototype, and production. He explained that traditional manufacturing is “backlogged” and hampered by slow processes and skill gaps.
While AM boosts production efficiency, Jeldi recognizes that Velo’s 3D printing capabilities are unsuitable for high-volume, million-part production runs. Instead, the company excels at delivering small numbers of high-quality, AM-optimized metal parts. This is a key reason behind Velo3D’s focus on defense and aerospace over other verticals, such as automotive. “We’re not driving in automotive in any way because we want to be in this space,” Jeldi explained.
An aerospace component 3D printed by Velo3D. Photo by 3D Printing Industry.
The future of 3D printing at Velo3D
For Jeldi, the future of 3D printing at Velo3D is bright. Amid strong demand for the company’s new RSP service, Jeldi revealed plans to build a new 3D printer production facility in the American Midwest.
This expansion will see Velo3D grow its production capabilities across the United States, shifting manufacturing closer to customers and labor pools better suited for scaled operations. While Velo3D has not yet selected a final location, Jeldi aims to have the new facility in full production by 2027 or 2028. Additionally, the company is set to retain a presence in California. R&D operations will remain in the Golden State due to a “lack of skill set in the Midwest.”
Velo3D’s new CEO isn’t just planning for the next three years, he’s looking 25 years ahead. Jeldi’s long-term roadmap includes developing a next-generation Velo3D printer. He explained that the company’s R&D efforts focus on creating a fully automated machine that any OEM can operate with minimal experience.
At the same time, Velo3D plans to improve cost stability and scale up production to meet growing RSP demand. In the Midwest, the company aims to expand further with multiple new facilities and to build a network of contract manufacturers, creating a secure 3D printing ecosystem.
Jeldi was clear that additive manufacturing cannot solve all manufacturing challenges within the aerospace, space, and defense sectors. Instead, the future will see Velo3D increasingly leverage AM in a “hybrid model” that combines traditional manufacturing methods. The recently appointed CEO revealed that customer feedback is guiding this roadmap. Velo3D is talking directly with its customer base to deliver value, and has noted growing demand for faster production capabilities. Jeldi is confident that better aligning operations with the clients’ future vision “will make us successful.”
Read all the 3D printing news from RAPID + TCT 2025
Who won the 2024 3D Printing Industry Awards?
Subscribe to the 3D Printing Industry newsletter to keep up with the latest 3D printing news.You can also follow us on LinkedIn, and subscribe to the 3D Printing Industry Youtube channel to access more exclusive content.Featured image shows a part 3D printed using Velo3D’s Sapphire technology on display at RAPID + TCT 2025. Photo by 3D Printing Industry.
0 Commentarii
0 Distribuiri
70 Views