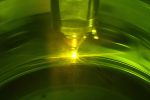
3DPRINTINGINDUSTRY.COM
New repair solution cuts Pratt & Whitney’s GTF engine service times by 60%
American aerospace manufacturer Pratt & Whitney (P&W) has introduced a newly developed AM repair process designed to speed up the servicing of GTF engine components.
The aerospace manufacturer expects the new method, which it says can cut process time by more than 60%, to be rolled out across its global maintenance, repair, and overhaul (MRO) network after industrialization efforts are complete. Over the next five years, the company estimates that incorporating additive repairs into its MRO operations could help recover around $100 million worth of parts.
“A more agile, additive repair process allows us to better serve our customers by improving turnaround time, while reducing tooling costs, complexity and set up,” said Kevin Kirkpatrick, Vice President of Aftermarket Operations at P&W. “At the same time, it reduces our dependency on current material supply constraints.”
Pratt & Whitney has developed a new solution that will enable repair to GTF structural case features using a 3D printing method known as Directed Energy Deposition (DED). Photo via Pratt & Whitney.
Repair process enhances engine overhaul
Created at the company’s North American Technology Accelerator in Jupiter, Florida, the repair process focuses on restoring structural case features of GTF engines.
Rather than relying on conventional techniques, the new approach uses DED to ensure deposits of material exactly where it is needed. P&W said the process eliminates several steps from the traditional method, with most of the time savings coming from fewer machine changeovers and a reduction in heat treat cycles.
Work on the solution was carried out in alliance with the Connecticut Center for Advanced Technology (CCAT) and the RTX Research Center. While the immediate focus is on structural repairs, the company plans to extend the application of the technology to refurbish components that wear down during normal engine use.
The repair development is part of a broader strategy by P&W to bring advanced technologies into its aftermarket services. Earlier this year, the company announced an expansion of its technology accelerator programs to target areas such as digital inspection, adaptive processing, and advanced coating and masking techniques for key engine parts, including blades, fans, and cases.
Together, the initiatives are expected to contribute at least $24 million in annual savings once fully deployed.
Alongside its North American accelerator, it complements a similar facility the company established in Singapore in 2022. That location focuses on robotics, advanced inspection techniques, connected manufacturing systems, and digital twin applications. Both sites aim to support upgrades in maintenance capabilities across the company’s global service network.
As of today, the aerospace manufacturer’s GTF MRO network includes 20 shops across four continents, supported by quick-turn sites and offered through the EngineWise portfolio to help operators extend asset life and manage long-term performance.
Advancing aerospace MRO
Over the years, other novel ways have been explored to improve the efficiency, precision, and sustainability of repairing and assessing aerospace components.
In March 2022, it was announced that GE Aerospace (at the time GE Aviation) became the first company to gain approval for using metal AM to repair commercial jet engine components, with its Loyang facility in Singapore leading the initiative.
GE Aviation has used 3D printing to produce aircraft parts, including in Boeing’s 777x jet engine (pictured). Photo via Boeing.
Having leveraged 3D printing, particularly GE’s Concept Laser M2 machines, the company halved repair turnaround times, increased daily repair capacity, and reduced floor space requirements by one-third. Initially applied to high-pressure compressor blade repairs, the automated process uses image analysis to customize each part. The approach also supports sustainability goals by reducing waste, energy consumption, and the need for part replacements.
On the software front, Nanyang Technological University Singapore (NTU Singapore) researchers developed a rapid, low-cost imaging method to assess the microstructure and material quality of 3D printed metal parts.
Using an optical camera, flashlight, and proprietary machine-learning software, the system analyzed surface crystal patterns within 15 minutes at a fraction of the cost of electron microscopy. The method aimed to benefit industries like aerospace by simplifying certification and quality assessment for mission-critical parts used in MRO.
What 3D printing trends should you watch out for in 2025?
How is the future of 3D printing shaping up?
To stay up to date with the latest 3D printing news, don’t forget to subscribe to the 3D Printing Industry newsletter or follow us on Twitter, or like our page on Facebook.
While you’re here, why not subscribe to our Youtube channel? Featuring discussion, debriefs, video shorts, and webinar replays.
Featured image shows Pratt & Whitney has developed a new solution that will enable repair to GTF structural case features using Directed Energy Deposition (DED). Photo via Pratt & Whitney.
Ada Shaikhnag
With a background in journalism, Ada has a keen interest in frontier technology and its application in the wider world. Ada reports on aspects of 3D printing ranging from aerospace and automotive to medical and dental.
0 Yorumlar
0 hisse senetleri
75 Views