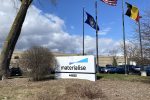
3DPRINTINGINDUSTRY.COM
[INTERVIEW] Brigitte de Vet-Veithen on The Future of 3D Printing at Materialise
Before RAPID + TCT 2025 kicked off, Materialise celebrated its 35th anniversary at its North American headquarters in Plymouth, Michigan. During the event, which included a guided tour of the Belgian software developer’s medical 3D printing facility, I sat down with CEO Brigitte de Vet-Veithen.
We discussed the importance of building a strong presence in the U.S. amid uncertain trade policies, certification challenges in additive manufacturing, 3D printing for mass production, and her outlook for the future of 3D printing.
The Materialise CEO highlighted where 3D printing is being leveraged to produce millions of parts and touched on her company’s increasing focus on defense applications. Significantly, de Vet-Veithen called additive manufacturing a “slow revolution.” She explained how the company’s “North Star” approach influences its “longer-term perspective.”
Read more 3D printing news and executive insights from RAPID + TCT 2025
For de Vet-Veithen, collaboration is key. “Our competition is not each other in AM,” she said. “Our competition is traditional manufacturing.” These values were reflected by Materialise’s RAPID + TCT announcements, which included two new build processors developed in partnership with One Click Metal and Raplas. For the latter, Materialise’s technology has accelerated 3D printing speeds by up to 40%. In other news, Materialise introduced a new update to its Magics software that integrates nTop’s implicit geometries to reduce build preparation times from days to seconds.
While doom-laden discourse prophesying the death of additive manufacturing persists from some quarters, de Vet-Veithen is more optimistic. She believes “we’re still at the start of AM adoption,” emphasizing the significant opportunity in the medical, aerospace, and defense sectors. Materialise delivers 280,000 3D medical devices annually and has fabricated over 500,000 aerospace components.
However, de Vet-Veithen cautioned against overhyping 3D printing. Appointed CEO of Materialise in January 2024, she believes the industry has yet to reach a pivotal inflection point. While signs of progress are encouraging, she emphasized the need for patience, demonstrable results, and a focus on application-driven solutions.
Materialise CEO Brigitte de Vet-Veithen. Photo via Materialise.
Materialise’s strategic presence in the United States
As I spoke with de Vet-Veithen on April 7, 2025, the economic impacts of the Trump administration’s sweeping tariffs, announced the week prior, were already unfolding. On the day of our meeting, the Dow Jones Industrial Average dropped 349 points and the S&P 500 slipped 0.23%, as tensions in the U.S.-led trade war escalated.
Despite these concerning headlines, Materialise’s CEO remained pragmatic. Although the full impact remains unclear, she noted that shifting trade dynamics could drive domestic 3D printer adoption. “It will definitely impact us, and hopefully in a good way,” added de Vet-Veithen.
The HEC Liège alumna acknowledged the risk that aggressive tariff policies pose to Materialise’s supply chains. However, she emphasised the strategic advantage of maintaining a U.S.-based manufacturing facility. “It’s hugely important for us to have a presence here because the US is a hugely important market in the additive industry,” she said.
The CEO singled out the medical sector as a critical segment within America’s borders. Materialise manufactures around 280,000 3D printed implants and medical instruments annually, including 160,000 for the U.S. market. In 2023, the Leuven-based company expanded its Michigan base with a new metal 3D printing hub. This state-of-the-art facility features multiple laser powder bed fusion (LPBF) systems dedicated to patient-specific devices like titanium cranio-maxillofacial (CMF) implants used in facial reconstruction surgery.
Before opening the facility in 2023, Materialise had manufactured CMF devices at its AM facility in Belgium. Now, the company can respond more quickly to the needs of surgeons in hospitals across the U.S., reducing lead times for patients requiring personalized implants.“Everything we do is patient-specific,” added de Vet-Veithen. Materialise’s Plymouth site handles the full workflow, from converting medical images into design files to 3D printing, post-processing, and quality assurance in a 10,147 Square foot clean room.
Materialise also runs a polymer (resin and SLS) 3D printing operation at its U.S. headquarters, prioritizing anatomical models, surgical guides, and personalized implants. Elsewhere in the building, the Belgian company conducts R&D, software development, automotive tooling, and 3D printed insole commercialization.
Materialise’s U.S. Headquarters in Plymouth, Michigan. Photo by 3D Printing Industry.
Overcoming 3D printing certification challenges
Although 3D printing holds major potential for demanding applications, stringent certification requirements remain a significant barrier to adoption. This is also a critical challenge for other regulated industries like aerospace, space, defense, and automotive.
However, de Vet-Veithen suggested that the last decade has seen real progress, at least in healthcare. “We’ve made huge progress in figuring out how to deal with the regulations and how to get the right certification in place,” she stated.
De Vet-Veithen stressed that Materialise does not write regulations directly. However, the company has worked openly with authorities like the U.S. Food and Drug Administration (FDA) to create awareness around additive manufacturing technologies. “We have always been very open to working with the FDA, to help them understand what additive manufacturing is,” she said. The goal for de Vet-Veithen is to increase certainty around clear regulatory frameworks to help foster future adoption, accelerate innovation, and boost investor confidence.
Materialise also actively collaborates with standards organizations alongside its regulatory efforts. De Vet-Veithen praised these groups, calling their work in additive manufacturing “amazing.” Organizations like the International Organization for Standardization (ISO) and ASTM International depend on industry experts and “members like us” to shape frameworks to encourage wider 3D printing adoption. “As an industry leader, we must take on that role and responsibility,” she said.
De Vet-Veithen believes the aerospace and defense industries are earlier in the certification journey than the medical sector. “There’s still more work to be done on that side, but we can learn a tremendous amount from what we’ve done in medical,” she explained. As with healthcare, Materialise is engaging closely with other sectors to help foster understanding around 3D printing and support the creation of new regulations.
Materialise has established a robust portfolio of flight-ready accreditations, including EASA Production Organisation Approval and EN 9100 certification for manufacturing flying parts. These credentials have enabled the company to deliver more than 500,000 3D-printed components to the aerospace sector. It currently produces around 4,000 distinct part types each year. Materialise supports the full aerospace and aviation value chain, serving OEMs, airlines, MROs, and suppliers. In early 2025, it expanded this presence by opening an Aerospace Competence Center at the Aerospace Innovation Hub in Delft, the Netherlands.
Following the release of its first-quarter 2025 results last week, de Vet-Veithen told investors the company is reassessing its role in the defense sector by extending “our offering into this segment.” The shift comes amid what she called a “breakdown of traditional global alliances,” as geopolitical tensions escalate. De Vet-Veithen said deeper involvement in defense 3D printing would further reinforce the company’s position in aerospace and unlock “new opportunities in the future.”
Transseptal puncture heart model 3D printed by Materialise. Photo by 3D Printing Industry.
3D printing for mass production
De Vet-Veithen believes the industry is at a “critical point.” She argued that “we really need to push the boundaries on getting serial manufacturing going.” Materialise’s CEO added that the company’s software can play a “tremendous role” in allowing companies to scale their operations into serial production. The value of Materialise software is not just in automation, but in building intelligence into the production chain. Capturing and leveraging data from across workflows to monitor builds and inform future projects is critical, de Vet-Veithen emphasized.
But what scale is possible with additive manufacturing? Had I asked this question a few years ago, de Vet-Veithen would have told me not to look at high-volume applications. However, she explained that this “reality is changing as we speak,” amid growing technological maturity, application development, and automation.
She pointed to China, where 3D printing is not just manufacturing thousands of parts. Instead, “we’re talking millions of parts,” especially for electronics applications. De Vet-Veithen also highlighted impressive volumes in the healthcare sector. She pointed to “millions of implants” produced with additive’s functional benefits, such as complex porous structures.
Even so, de Vet-Veithen cautioned that mass manufacturing is not the most suitable entry point for those adopting 3D printing. “Is it the best way for people to start? No, absolutely not,” she said. Instead, additive manufacturing is most valuable where it delivers clear design or functional advantages, rather than as a like-for-like substitute for conventional production methods. That said, she believes the industry is steadily uncovering “more and more applications where the functional benefits really are there.”
Neurovascular Procedural Plan model 3D printed by Materialise. Photo by 3D Printing Industry.
Materialise’s outlook on the future of 3D printing
Forecasting trends in AM is complex, de Vet-Veithen acknowledged, because leading and lagging indicators differ sharply by application area. In healthcare, for example, improved reimbursement pathways for patient-specific solutions could dramatically accelerate adoption. However, such mechanisms are irrelevant to other sectors like aerospace or defense.
Despite these nuances, she outlined a five-year vision for Materialise and the broader 3D printing industry. Central to this outlook is the increasing adoption of AM for serial manufacturing. “I absolutely believe that it’s going to happen,” she stated, pointing to the potential for workflow efficiencies and lower cost per-part amid increasing technological maturity.
Additionally, de Vet-Veithen expects the defense, aerospace, and healthcare sectors to be key drivers of 3D printer adoption in the coming years. She clarified that this does not yet represent an inflection point for AM. However, this reality will move closer as the decade nears its end, according to de Vet-Veithen.
She also explained that artificial intelligence (AI) and data-driven manufacturing will begin to transform workflow management. “We shouldn’t overhype AI, but there is potential,” she cautioned. “You can only do smart manufacturing leveraging AI if you have the data.” This is where Materialise’s CO-AM platform comes in. The company is “pushing the boundaries” with its software to help users collect data that can be used to build AI models.
De Vet-Veithen concluded that while additive manufacturing represents a transformative shift, its full impact will take time to materialise. “There’s hard work needed to make it happen, and there are a lot of steps that need to be taken.” She urged industry peers to adopt a long-term perspective rather than focus on short-term gains, arguing that only a collective, sustained effort will deliver the impact “we all dream of.”
Read all the 3D printing news from RAPID + TCT 2025
Who won the 2024 3D Printing Industry Awards?
Subscribe to the 3D Printing Industry newsletter to keep up with the latest 3D printing news.You can also follow us on LinkedIn, and subscribe to the 3D Printing Industry Youtube channel to access more exclusive content.Featured image shows Materialise’s U.S. Headquarters in Plymouth, Michigan. Photo by 3D Printing Industry.
0 Yorumlar
0 hisse senetleri
85 Views