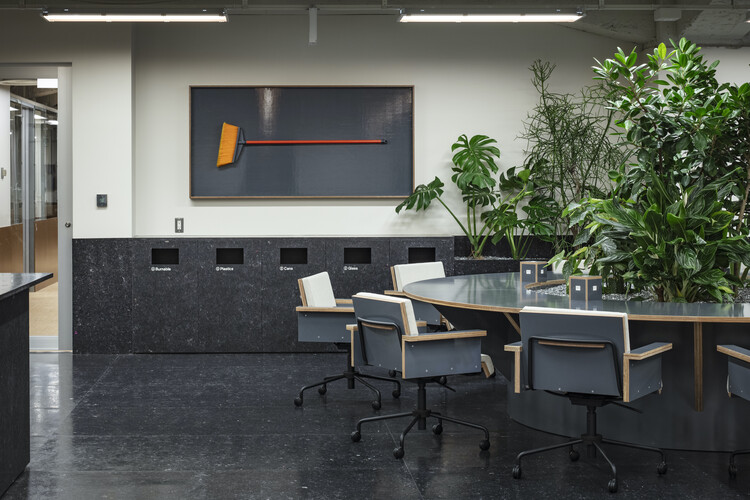
WWW.ARCHDAILY.COM
0 Club Coworking Space / DDAA
0 Club Coworking Space / DDAASave this picture!© Kenta Hasegawa
Architects:
DDAA
Area
Area of this architecture project
Area:
1742 m²
Year
Completion year of this architecture project
Year:
2024
Photographs
Photographs:Kenta HasegawaMore SpecsLess Specs
Save this picture!
Text description provided by the architects. Many people might not be familiar with the technology area called Climate Tech. This term refers to a technology often discussed that focuses on reducing CO2 emissions or dealing with the effects of global warming. Many startups in Japan and overseas are addressing the issue of decarbonization in the business world while also pursuing profitable business ventures. DDAA designed the interior of the 0 Club, a coworking space for startups, VCs, and academics specializing in Climate Tech and related businesses. The term "Climate Tech" covers a wide range of approaches to the goal of carbon neutrality, including the development of alternative and clean energy sources to replace petroleum, measures to address construction materials such as concrete and steel that emit large amounts of CO2 and toxic substances during the production process, the development of upcycled and recycled materials with low environmental impact, and measures to reduce food loss. The 0 Club was created as a place for companies in this field to come together.Save this picture!Responding to humanity's ceaseless efforts and desires, our world is increasingly flooded with ever-more convenient products and services. The scale of the infrastructure supporting a well-organized and convenient lifestyle is rapidly increasing, and the balance of the global environment and the entire social system is becoming distorted. If we continue to pursue convenience without considering the consequences, developing countries will suffer first, and developed countries will be affected. However, because restoring the balance would involve some inconvenience in people's daily lives, those of us who have already become accustomed to the convenience of modern life cannot bring ourselves to make such a drastic change.Save this picture!Save this picture!If we consider only the environment, the best option would be to stop making things, but that would mean denying social progress and past achievements. If we stop aiming for a better state of affairs, we will become increasingly conservative, and all intellectual renewal will come to a halt. This ambivalent state, where two contradictory thoughts - "Do we really need more?" and "I want to make the world a better place" - coexist, is probably the premise of modern manufacturing.Save this picture!If that is the case, we may try to enjoy this contradiction, consider ways to use the restrictions and regulations as triggers for creativity, and embrace the inconvenience. For example, during the Prohibition era of the 1920s, a large number of cocktail recipes were invented to disguise alcoholic drinks as non-alcoholic drinks in illegal speakeasies. During the Edo period, when the commoners were prohibited from enjoying luxuries and only allowed to wear brown, grey, and greyish-brown, a variation of dyeing called "48 browns and 100 greys" was created, which produced multiple shades of these colors. In this way, rather than just seeing restrictions as they are, we should raise the resolution of our creativity and reinterpret them as tools to have fun.Save this picture!Games and sports have developed as platforms to enjoy such "prohibition rules." Soccer is a game that shares the straightforward restriction everyone understands: Do not use your hands. The simple rule prohibiting one of the most important aspects of being human - the hands - is easy to share across language barriers. Through trial and error, brilliant plays are born, people get excited, it drives the economy, stadiums are built, and urban infrastructure gets upgraded for the World Cup. The research and development of soccer uniforms and shoes to support more effective play and further the development of soccer are naturally related to chemistry and physics, and contribute to the development of medicine and ergonomics. Using soccer as an example, can we design a methodology for creating something while enjoying the constraints and inconveniences?Save this picture!Under the themes of "sustainability without compromise" and "create without creating as much as possible," this project uses materials with low environmental impact, natural materials, and things that are readily available, while stopping to investigate and reflect on each step and making the most of existing things as much as possible. This inevitably requires more time and careful thought, leading to increased costs. If we reinterpret "carefulness" as "craftsmanship," it is about improving quality rather than simply fulfilling functionality. It is similar to paying meticulous attention to the details of a kimono's weave or applying multiple layers of urushi lacquer. Thinking about ways to achieve sustainability may also lead to thinking about it as a modern craft design. All things, not just architecture and interior design, are made by combining materials and production methods. This time, we decided to consider both aspects using the phrase "low environmental impact" as a prefix.Save this picture!Save this picture!Broadly speaking, "environmentally friendly" materials have high recycling and upcycling rates and minimize CO2 emissions in the manufacturing process as much as possible. However, the more you learn about them, the more you realize this is not as simple as it seems. This is because problems exist not only in how materials are produced but also in how much they are used. The environmental impact of fundamental materials is significant when considering the overall impact, but the materials we see and use in our daily lives should not be ignored either.Save this picture!Two fundamental materials used in modern architecture are steel and concrete, and the cement and steel industries are known to produce a substantial amount of CO2 emissions. The more fundamental the material, the more efficient its production needs to be. The word "efficient" is tricky because it means centralization, so naturally, CO2 emissions are concentrated in a specific area. Given this, research into green steel and alternative concrete, which emit less CO2 during production, is underway, as are efforts to recycle CO2 emissions.Save this picture!Save this picture!Save this picture!Then, what about already existing recycled materials? While manufacturers are putting a lot of effort into developing materials with low environmental impact, recycling inevitably involves breaking down and remaking the material, resulting in color irregularities and making it difficult to create a homogeneous material. In addition, because it involves an extra step of collection, the cost is often relatively high. The same applies to environmentally friendly natural materials such as bamboo and cork, which have many unknown factors and are often costly and challenging to handle. It makes us realize how humans have evolved by developing convenient things requiring little effort. To begin with, determining a product's environmental impact requires much effort to visualize CO2 emissions, which means balancing effort and effectiveness is crucial.Save this picture!A building's composition can be roughly divided into architecture, interior, and furniture. Buildings are made to last longer and continue to exist for a long time. The concept of "vintage" applies to furniture, meaning one can still obtain pieces made in the 1930s. However, the interior is often renewed every 10 to 20 years, rather than every 100 years, because it has to keep up with tenant turnover and the renewal of electrical, air conditioning, and low-voltage equipment. Given this, we concluded that it would be better to keep the interior work to a minimum this time and concentrate on the furniture and fixtures to compose the space. We will use as much of the existing interior as possible and "create without creating as much as possible." In addition, transportation to procure materials can also impact the environment. So, we decided to proactively use materials sourced locally, such as the cardboard boxes that arrive at our office, the photocopy paper used in this project, and the formwork that our client used in the seismic retrofitting work on the same building.Save this picture!The production rules that were ultimately adopted for this project are summarized as follows:The existing interior should be reused as much as possible without new construction. For areas where construction is unavoidable, only low-impact, environmentally friendly materials are used. In addition, when making things, it is essential to simplify the production process as much as possible, use fewer materials, and consider ways to make it easier to recycle or upcycle in the future. Items that can be substituted with furniture should be made as furniture as much as possible, so they can be continuously used in the future. We should reduce the transport of goods and reuse waste materials from construction as much as possible.Save this picture!Floor – The OA floor system is an office floor system under which wiring can be routed. This system is used in most office buildings. This project reused the existing OA floor as much as possible. The common areas were finished with a recycled material called Rifmo, and the private areas were finished with particleboard, up to the height not subject to the restriction on interior material use, eliminating the need to use non-combustible materials.Save this picture!Wall – The walls were the most challenging part of the interior construction, while ensuring the non-combustibility of the interior. This was because we could not find environment-friendly materials that could replace conventional LGS (light gauge steel substrates) and glass (from a startup perspective, this may be a business opportunity.) For this reason, we used conventional LGS. Due to the restriction on interior material use, we chose particleboard for the common areas and Rifumo for the private areas, and finished the walls up to waist height. Particleboard is made by crushing waste wood and is used as a substrate. It is the only type among fiberboard materials (including OSB and MDF) that uses crushed waste wood. The glass on the upper half of the wall is attached directly to the LGS using screws, minimizing the amount of framing material used. No sealant is used, eliminating the need for sorting when upcycling. The glass details are designed for easy removal. All the plasterboard is made from upcycled circular plasterboard.Save this picture!Ceiling/lighting/air-conditioning – The ceilings in the common areas were dismantled to increase the ceiling height. In contrast, the ceilings in the private areas were reused without dismantling, reducing the work required to install the ceiling fixtures when constructing the private rooms. Things that can be reused, such as air conditioning and lighting, were adjusted and repositioned without additional work. The color temperature of the existing lighting was adjusted by simply attaching film and acrylic using paper clips known as "double clips." This reduced the cost of the B construction and made removing the film easier in the future, facilitating maintenance and warranty work.Save this picture!Save this picture!Furniture layout – Given that this office is for a community specializing in a specific field, the layout is designed to allow people to walk around the entire facility. Private rooms are arranged in a radial pattern around the central lounge, and nap rooms, phone booths, etc., are dispersed between the private rooms so that they are automatically exposed to information from surrounding areas. The lounge can be divided into separate areas by curtains and used for various events. This room has a flexible layout, with several layout patterns in mind, such as a conference for about 100 people or group work. We aimed to create a space where the furniture and design could be used as a starting point for conversation, with traces of thought given to the environmental impact in all fixtures.Save this picture!
Project gallerySee allShow less
Project locationAddress:Chiyoda-ku, Tokyo, JapanLocation to be used only as a reference. It could indicate city/country but not exact address.About this officeDDAAOffice•••
Published on May 01, 2025Cite: "0 Club Coworking Space / DDAA" 01 May 2025. ArchDaily. Accessed . <https://www.archdaily.com/1029688/0-club-coworking-space-ddaa&gt ISSN 0719-8884Save世界上最受欢迎的建筑网站现已推出你的母语版本!想浏览ArchDaily中国吗?是否
You've started following your first account!Did you know?You'll now receive updates based on what you follow! Personalize your stream and start following your favorite authors, offices and users.Go to my stream
0 Comments
0 Shares
21 Views