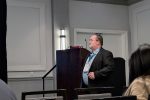
3DPRINTINGINDUSTRY.COM
Inside m4p’s Powder Playbook: Tight Tolerances and Contamination Control
As metal additive manufacturing scales from prototyping to serial production, powder quality demands are intensifying. At m4p Material Solutions, that means going far beyond standard compliance. From tightening tolerances on sphericity and alloy composition to developing in-house methods for detecting microscopic contamination, the company is positioning itself at the frontier of reliable, production-grade materials supply.
m4p Targets AM Maturity With Agile Materials Portfolio and Processing Warnings
Speaking at the 2025 AMUG Conference, Burghardt Klöden, Global Sales Director at m4p Material Solutions, is blunt about what the additive manufacturing sector still lacks: maturity. “We believe the AM ecosystem still needs some growth,” he said. “We help people get started and ideally, grow together.”
The company, founded ten years ago, has scaled rapidly, surpassing triple-digit customer counts and tripling revenue since its inception. Its core value proposition is responsiveness (90% of deliveries are made within one to three days) and technical flexibility, supporting all powder-based AM technologies initially with small minimum order quantities, then large quantities as usage increases.
The materials portfolio is divided into three categories: standard materials (just over one-third), development products (about 40%), and customized materials tailored to client specifications (around one-quarter). The development products are typically co-created with R&D or industrial partners and include several proprietary or licensed alloys.
Resisting Limits: A High-Temp Aluminum Alloy
One of m4p’s recent highlights is a high-temperature aluminum alloy known as ResistAl, originally developed externally and licensed into their portfolio. “At the time, it was really unique,” Klöden said. The material targets applications such as aerospace and motorsports, offering impressive strength retention at elevated temperatures without requiring post-build heat treatment.
ResistAl is a multi-phase alloy with notable high-temperature microstructural stability. Klöden explained that the yield strength remains virtually unchanged even after 200 hours of artificial aging at 250°C. “No major change in microstructure, even after artificial heat treatment. This makes this alloy pretty special,” he said.
However, this performance comes at a cost, “This material is very challenging to process.” To achieve the advertised mechanical properties, samples must be printed on specialized machines equipped with heated build plates reaching 350°C.
Despite this, m4p’s customers are pushing boundaries. A French R&D partner recently managed to print ResistAl on a standard AM machine, a breakthrough Klöden characterized as both impressive and unlikely without deep process expertise. The customer was able to 3D print a complex component with lattice structures and no signs of delamination, a task m4p had previously failed using the same setup. “If you do it right, there is a good chance you are rewarded with outstanding properties,” he noted.
Iron-Based Versatility and Unexpected Consumer Use
The company’s iron-based alloy portfolio includes several grades tailored for specific industrial segments, from oil and gas to high-displacement automotive components. One material Klöden highlighted, based on a 6+ iron alloy, combines the hardness of martensitic structures with the corrosion resistance of austenitic types. The properties can be tuned via heat treatment, offering high tensile strength and modifiable elongation.
A particularly unconventional case study involved a consumer product: tailor-made knives. A customer used the 6+ alloy to produce durable, customized blades with engraved handles, leveraging AM’s design freedom and material hardness to differentiate their offering. Though far from m4p’s core industrial clientele, the example underscored the flexibility of their materials platform.
As m4p’s customers shift from prototyping to serial production, their expectations shift accordingly. Klöden emphasized that powder consistency, particularly flowability and spreading behavior, becomes increasingly critical. “In prototyping, you can make up for some failed parts,” he said. “In serial production, this gets much more critical.”
Larger build volumes introduce higher risks of part failure during the build or post-processing stages. m4p has responded by ensuring their powders meet tight specifications on parameters such as particle size distribution and morphology. While the former is commonly reported on certificates of analysis, the latter (linked to powder sphericity and flow characteristics) is not, though it directly affects build quality.
Advanced Powder Testing for Metal Additive Manufacturing
Ensuring consistent material performance in additive manufacturing requires more than meeting specifications. Fittingly, m4p has moved beyond a compliance mindset toward proactive control of variability across batches. “Don’t max out what you’re given by the spec,” he said. “This leads to instability in processing.”
Using Ti-6Al-4V as an example, Klöden detailed how m4p applies tighter internal controls than industry standards demand, particularly for particle morphology and chemical composition. Sphericity is measured using image analysis that evaluates the ratio between a particle’s major and minor axes. “A ratio of 0.9 is already quite close to ideal,” he noted, “and we monitor how much of our powder stays above that threshold.”
This level of control also applies to elemental composition. Klöden displayed data from multiple years of titanium alloy production, showing how the company maintains a consistent aluminum concentration near the lower end of the acceptable range. “It’s not easy, but it’s well managed,” he said.
A Structured Approach to Quality
While many powder suppliers address morphology and particle size distribution (PSD), contamination remains poorly standardized. M4p’s Priyanshu Bajaj explained, “There’s no existing ISO or ASTM standard that defines a repeatable method to quantify contamination in metal powders.”
To fill this gap, m4p has developed its own methodology, built around scanning electron microscopy (SEM) paired with energy-dispersive X-ray spectroscopy (EDS). This enables both visual detection and elemental classification of unwanted particles.
“The moment you add anything that’s dissimilar and undesired, for example, plastic fragments or foreign metals, that’s contamination,” said Bajaj. “Even if it’s small, even if it’s rare, it can cause problems.”
Because such contamination is often invisible to standard chemical assays or PSD reports, m4p adapted pharmaceutical-grade sampling techniques to ensure statistical relevance. Powders are sampled and prepared for SEM inspection using an automated platform and image analysis software. EDS is then used on identified outliers to determine their composition.
One customer returned a batch after experiencing unexpected part failures. The SEM-EDS process revealed the presence of sub-5-micron cobalt-based particles, well below the detection limits of conventional analysis, but sufficient to affect downstream performance. “You wouldn’t catch this with standard methods,” the team said. “But it’s enough to cause real trouble in production.”
m4p’s statistical approach to contamination testing. Photo by Michael Petch.
What Happens When Contamination Is Detected?
Asked about next steps after identifying contamination, the company clarified that while rejecting a batch is sometimes necessary, other options exist. “It depends on the nature of the contamination,” they said. “We assess whether cleaning or powder reclamation is viable. If not, we discard the batch.”
The team stressed that this level of scrutiny is part of standard procedure for all outgoing shipments. With contamination rates below 2 percent by particle count, most of them smaller than five microns, m4p positions itself as a supplier prepared for the stringent reliability needs of serial production environments.
The company’s message to customers is clear: robust quality control requires more than trusting what’s on the certificate of analysis. It requires ongoing inspection, tight tolerances, and an active risk management strategy: before the powder ever touches the machine.
The takeaway from m4p’s approach is that consistent powder performance cannot be left to certificates of analysis alone. Real stability comes from controlling what lies between the lines of a spec sheet: subtle variations in particle shape, contamination undetectable by routine tests, and long-term drift in composition. With an eye on data, automation, and pharmaceutical rigor, m4p is making the case that materials excellence is an operational discipline. This is critical to AM’s shift into mature manufacturing.
What 3D printing trends should you watch out for in 2025?
How is the future of 3D printing shaping up?
Subscribe to the 3D Printing Industry newsletter to keep up with the latest 3D printing news.You can also follow us on LinkedIn and subscribe to the 3D Printing Industry Youtube channel to access more exclusive content.
Featured image shows Burghardt Klöden, Global Sales Director at m4p Material Solutions. Photo by Michael Petch.
Michael Petch
Michael Petch is the editor-in-chief at 3DPI and the author of several books on 3D printing. He is a regular keynote speaker at technology conferences where he has delivered presentations such as 3D printing with graphene and ceramics and the use of technology to enhance food security. Michael is most interested in the science behind emerging technology and the accompanying economic and social implications.
0 Comments
0 Shares
43 Views