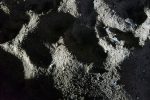
3DPRINTINGINDUSTRY.COM
$22 Million Exclusive Supply Agreement Between Velo3D and Amaero Boosts U.S. Manufacturing
Velo3D, a U.S.-based metal 3D printer manufacturer, has entered into a five-year exclusive supply agreement with Amaero, Australian-based metal AM specialist, projected to generate approximately $22 million in revenue. Under the terms, Amaero will serve as Velo3D’s exclusive supplier for Niobium C103 and other refractory alloy powders—including molybdenum, tantalum, tungsten, and zirconium—and will be the preferred supplier for titanium alloy powders.
Velo3D will also qualify Amaero’s spherical powders and develop exclusive print parameters for both C103 and refractory alloys across all Velo3D Sapphire printers, as well as for Amaero’s titanium alloy powder on new machine sales. The print parameters will be included with the 3D printing machine licensing, without any extra charge to customers.
Velo3D will use Amaero’s C103 and refractory alloy powders exclusively for all parts production, including its Rapid Production Solutions (RPS) initiative, and will dedicate a Sapphire machine to production with C103 powder. Velo3D will also dedicate a Sapphire XC machine to production with titanium alloys. Additionally, Velo3D will exclusively offer Amaero’s C103, refractory, and titanium alloy powders for sale to its 3D printing machine customers.
The Sapphire family of printers. Image via Velo3D.
Velo3D explained that this collaboration is a step toward supporting the re-shoring of advanced manufacturing to the United States. Dr. Arun Jeldi, Velo3D’s CEO, commented: “Velo3D is very excited to enter a long-term supply agreement with Amaero and to extend our proprietary print parameters to include C103 and refractory alloy powders. As space and defense applications evolve to require materials that perform in very high temperature and extreme condition environments, a proficient capability to 3D print parts from C103 and refractory alloys is an important and differentiating capability.”
Amaero’s Strategic Expansion and Commitment to U.S. Manufacturing
Hank J. Holland, Chairman and CEO of Amaero, emphasized that strengthening and expanding U.S.-based advanced manufacturing and supply chain capabilities is central to the company’s strategy. He noted that after decades of offshoring, recent policy efforts—particularly under the Trump Administration—have reprioritized industrial policy to support both national security and economic growth.
In response to critical vulnerabilities in the domestic supply chain, Amaero is making capital investments totaling approximately A$72 million through FY2026. This includes the commissioning of four state-of-the-art gas atomizers, expected to provide an annual powder production capacity exceeding 800 metric tonnes. The company has also allocated specialized production areas: one room and an EIGA Premium system for atomizing refractory alloys like niobium, molybdenum, tantalum, tungsten, and zirconium, and another planned for titanium alloy production, with the capability to scale up to five EIGA Premium atomizers.
Refractory Powders. Photo via Amaero.
“To achieve the potential of metal additive manufacturing, it’s important that we have a vibrant and financially strong domestic ecosystem that includes 3D printing OEM companies, high throughput and technically proficient part manufacturers and scalable, high quality, cost competitive spherical powders, “ said Holland. “We look forward to collaborating with Dr. Arun Jeldi and the Velo3D team to accelerate adoption of metal 3D printing and to improve the resiliency and scalability of domestic manufacturing.”
Strategic Supply Chain Partnerships
In March, PyroGenesis, a Canadian metal powder producer, officially confirmed Boeing as the aerospace OEM in its Ti64 metal powder qualification process, ending months of speculation. P. Peter Pascali, President and CEO of PyroGenesis, emphasized the significance of this achievement. “PyroGenesis is proud to be in the final queue for achieving supplier status with Boeing, one of the largest, most notable, and most advanced companies in the world. What’s exciting for PyroGenesis is that Boeing has shown itself to be a true innovator in the additive manufacturing arena, having spent more than three decades using 3D printed parts.”
In February, Ireland-based Croom Medical and US-based tantalum products supplier Global Advanced Metals (GAM) have developed a closed-loop supply chain approach to expand the use of tantalum in 3D printing. By tackling the material’s processing challenges and making its use more sustainable, the two companies are ensuring a steady, recyclable supply of tantalum powder for medical applications. Their process relies on Colibrium Additive’s M2 laser powder bed fusion (LPBF) technology to improve printing efficiency, making tantalum a more practical option for 3D printed implants.
What 3D printing trends should you watch out for in 2025?
How is the future of 3D printing shaping up?
To stay up to date with the latest 3D printing news, don’t forget to subscribe to the 3D Printing Industry newsletter or follow us on Twitter, or like our page on Facebook.
While you’re here, why not subscribe to our Youtube channel? Featuring discussion, debriefs, video shorts, and webinar replays.
Featured image shows Refractory Powders. Photo via Amaero.
Paloma Duran
Paloma Duran holds a BA in International Relations and an MA in Journalism. Specializing in writing, podcasting, and content and event creation, she works across politics, energy, mining, and technology. With a passion for global trends, Paloma is particularly interested in the impact of technology like 3D printing on shaping our future.
0 Comentários
0 Compartilhamentos
36 Visualizações