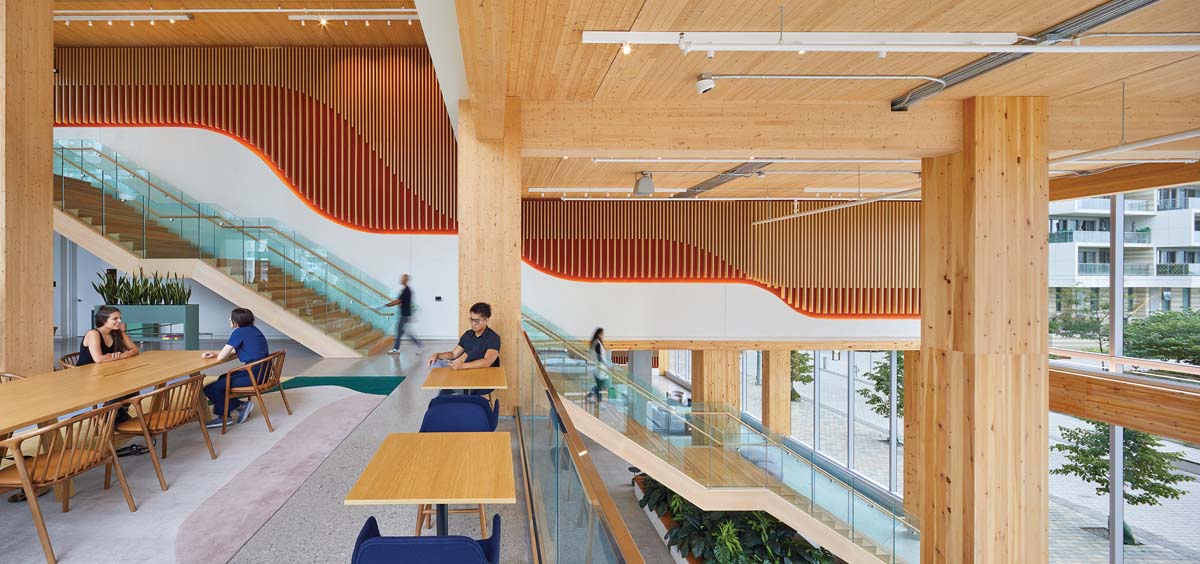
WWW.CANADIANARCHITECT.COM
Timber Redux
The two buildings of T3 Sterling Road are a contemporary take on the former industrial fabric of their neighbourhood, west of downtown Toronto. Photo by James BrittainPROJECTS T3 Sterling Road and T3 Bayside Phase 1ARCHITECTST3 STERLING ROAD DLR Group Architecture inc. (Design Architect and Architect-of-Record) and WZMH (Local Affiliate Architect)ARCHITECTST3 BAYSIDE WZMH Architects (Executive Architect) and 3XN (Design Architect)TEXT Lloyd AlterIn 1970, Barton Myers and Jack Diamond bought the Eclipse Whitewear Building on King Street in Toronto and converted it into offices. They left the brick walls and massive wood structure exposed, and kept visible all the conduits, ducts, sprinkler pipes and other mechanical paraphernalia, layering in industrial lighting. When you entered the space, you got the shock of the old: the existing warehouse adapted for modern use. Soon, warehouse conversions were happening around North America, including in San Francisco and in Minneapolis, where a renovation of the half-million-square-foot Butler Building became the continents most prominent example.Creative industries loved these spaces, which quickly filled with architects, advertising firms, and tech startups. Jane Jacobs understood this, writing in The Death and Life of Great American Cities, Old ideas can sometimes use new buildings. New ideas must use old buildings.Ground floor amenities include a generous co-working space. Photo by James BrittainBut old buildings were not without their problems. The floors were usually mill decking, where lumber such as 2x10s were nailed to each other to carry the heavy industrial loads. Noise passed right through them, as did dirt: staff would often find dust and debris on their desks.In 2016, real estate developer Hines built the continents first large new mass timber building, which they called T3 (for Timber, Transit, Technology). They aimed to capture the look and feel of a warehouse, without the drawbacks. It was sort of a new-old building. Hines noted in their marketing materials at the time:We love old brick & timber warehouses. We love the feel of them, the originality, and the entrepreneurship that lives inside their bones. They are cool places to collaborate, create, and innovate. Unfortunately, these buildings lack good natural light, are drafty, noisy, and have outdated HVAC systems. So we asked ourselves, why cant we solve these problems by selecting an authentic location, surrounded by heritage buildings, and construct a brand new, vintage building? All the charm of an old brick & timber building, with none of the downsides.Ground floor amenities include a generous co-working space. Photo by James BrittainThe Minneapolis T3, designed by Canadian mass timber pioneer Michael Green and American firm DLR Group, was built with glue-laminated columns and beams. Its floor slabs were made of Nail-Laminated Timber (NLT) supplied by StructureCraft of British Columbia, and nailed together in Winnipeg, Manitoba. Modern NLT was developed in Germany in the 1970s by engineer Julius Natterer. NLT was used because it was in the building codes and could be made anywhere, by anyone with a nailgun; Cross-Laminated Timber (CLT) was not yet approved or manufactured in North America. Unlike conventional construction, with mass timber, the supplier often acts as the timber structural engineer and builder, delivering the complete package. StructureCraft says, Our Engineer-Build model brings responsibility for all the steps of engineering and construction under one roof, to a company that has significant experience taking on this responsibility. Engineer-Build synthesizes and smooths out the building process.T3 Minneapolis was a success, and Hines took the concept to other cities, with a total of 27 buildings completed, under construction, and in design. The most recent finished T3s are in Toronto, where Hines has opened two projects: T3 Sterling Road and T3 Bayside.A new landscaped park is framed by T3 Sterling Road to the south, and the Museum of Contemporary Art (MoCA) to the east. Photo by James BrittainHines pitches its T3 projects as timber buildings with a conscience, claiming T3s exceptional amenities prioritize health and well-being, and the natural wood interior and bright, inspiring spaces help people feeland dotheir best. Research backs this up. An Australian study, Workplaces: Wellness + Wood = Productivity found that Employees surrounded with natural wooden surfaces on average reported higher personal productivity, mood, concentration, clarity, confidence and optimismand were more likely to find their workplaces relaxing, calming, natural-feeling, inviting and energising. These ideas are captured in the concept of biophilia, a term coined in the mid-80s by Harvard professor Edward O. Wilson to refer to humans fondness for nature, including plants, wood, and natural light.The leasable spaces feature Dowel-Laminated Timber (DLT) floor assemblies, along with glulam columns and beams. Photo by James BrittainHines also points to the environmental benefits, noting that building with wood avoids the emissions that come from making steel or concrete, which together total about 15 percent of global carbon emissions. When a tree is taken and used in a building that will last for centuries, the developer writes, that piece of wood is storing that carbon dioxide in the material for the life of the building.For T3 Sterling Road, Hines brought DLR Group and StructureCraft together again, including lead designer Steve Cavanaugh, who worked with Green on T3 Minneapolis. StructureCrafts roles once more encompassed acting as the timber structural engineer, coordinating timber sourcing, and providing supply and installation. The team also included WZMH Architects as the local architect of record.Torontos Sterling Road district has become a hotbed of warehouse conversions and brewpubs, anchored by the Museum of Contemporary Art; the New York Times has described it as newly hip, its appeal broadening beyond the small cadre of tuned-in artists and bohemian types who for years have had it to themselves. The site certainly nails the Transit of the T3 moniker, with a short walk to the Bloor subway and the UP Express train, which connects to downtown and the airport. The environmental importance of location and available transit is often underestimated: Alex Wilson of BuildingGreen calculated that the energy used by tenants commuting to a building was 2.3 times the energy consumed operating the building.Mullioned windows and upper level diagonal braces emulate the appearance of industrial buildings. Photo by James BrittainPhase 1 of the Sterling Road project includes two buildings totalling 300,000 square feet, constructed of glulam columns and beams, and with Dowel-Laminated Timber (DLT) floors. DLT was developed in the 1990s by a German company which called it Dbelholz, German for dowelled wood. Holes are drilled in softwood lumber with a moisture content of about 15 percent, and hardwood dowels, dried to about 8 percent, are driven in. As the dowels absorb moisture from the surrounding wood, they expand, locking the assembly together. StructureCraft has built sophisticated DLT machinery in its Abbotsford plant, which can spit out massive 12-foot-wide by 60-foot-long panels.Sterling Road is a bit rough around the edges, and the design for T3 Sterling aims to be edgy as well, with exposed diagonal bracing and steel bars added on the exterior to emulate the appearance of industrial windows. The program is geared towards young urbanites; while the upper floors are conventional leased office space, the ground floor has a large co-working space, a well-equipped gym, and bicycle storage.Different types of mass timber have distinct looks and feel, and DLT can be finished in different ways. T3 Sterlings DLT is made of 3-wide boards with a kerf on the corner, giving it a seriously industrial look, like you used to get in warehouses when wood was thicker. While most modern office buildings have a 30-foot-by-30-foot grid, mass timber is not cost-effective at that span, so the grids in the T3 are 20-by-30. DLR lead architect Steve Cavanaugh explained that many layouts were tested against the grid, and it was found to maintain planning flexibility.Although they both share the T3 label and are made of mass timber, T3 Bayside is a very different building from T3 Sterling Road. Its located in the rapidly developing area just east of the downtown core, and is surrounded by new residential towers.In branding this building, Hines adjusted the second T in T3 to substitute Talent for Transit, because its a fairly substantial 24-minute walk to Union Station. (A light rapid transit line, approved by the City in 2019, is currently in the design phase.) WZMH is back as the architect of record, with Danish firm 3XN as lead designer.At T3 Bayside, a band of glazing steps up to accommodate the possibility of interconnected spaces between office floors. Photo by Tom ArbanWhere T3 Sterling Road is industrial and edgy, T3 Bayside is all business. Its defining architectural feature is a stepped, recessed band of glazing ringing the faades, which permits a succession of double-height spaces. The original concept included grand stairs running through these double-height spaces from ground to top floor, but this was before the pandemic, when it was anticipated that the building might be occupied by a single tenant who would appreciate the interconnection of their spaces. However, the market has changed significantly, and the building is starting to be leased to smaller tenants. The double-height spaces are now called opportunities, and are currently filled with removable slabs. Common areas on the first, second, and third floors do remain connected, resulting in a small set of dramatic spaces, linked by enticing stairs. On the buildings west side, the stepped glazing corresponds with the staggered, stacked spaces of the buildings atrium, a communal lounge, and a shared meeting room. Photo by Tom ArbanAs at T3 Sterling, the columns and beams of T3 Bayside are made of glue-laminated timber, but this locations slabs are Cross-Laminated Timber (CLT). The laminations in CLT are made up of 2x4s, laid up flat to form a layer; the next set is laid at 90 degrees to the layer below, and so on. The whole sandwich is glued together in giant presses. CLT was invented in the States and patented in 1923, but modern CLT was developed by Professor Gerhard Schickhofer at Graz University in the 1990s. Austria had a large lumber industry, but being landlocked, exports were expensive. Turning lumber into CLT added significant value.CLT is more dimensionally stable than DLT, and can act as a two-way slab, supported on columns without beams. However, Hines specifies a column-and-beam design so they can get competitive pricing between the different mass timber technologies. To avoid the noise transfer that was endemic in older warehouse conversions, the CLT floor is topped with a sound mat and 2.6 inches of concrete.CLT is usually more expensive than DLT, but the wood, structural design and assembly for T3 Bayside is supplied by Nordic Structures. Nordic is a subsidiary of Chantiers Chibougamau, a vertically integrated lumber company controlling close to six million acres of black spruce Quebec forest; the company processes 15 percent of the renewable resources in the provinces woodlands. Geographically, Quebec is a lot closer than British Columbia, so it is likely that the reduced transport expense helps to balance out costs.At T3 Bayside, Cross-Laminated Timber (CLT) floor assemblies are paired with glulam columns and beams. Dropped ceilings are absent from both T3s, opening panoramic views to the city and lake. Photo by Tom ArbanIn the base building, there are no dropped ceilings to block the view of the mass timber beams and slabs, and no raised floorall mechanical and electrical services are exposed. What is normally hidden and often installed haphazardly has to be precise and straight. Every conduit and duct is laid out in advance in the BIM model; notches are cut into the tops of beams for them to pass through. With rare exceptions, the electrical conduits in both Toronto T3s are a work of art, resembling a circuit board rather than a typical electrical installation. The ventilation ductwork is also lovely to look at; in Bayside, there is a narrow structural bay without beams running around the core so that the main supply ducts can run east-west, while the smaller ducts run north-south between beams. It is all brilliantly coordinated. No lighting is installed in the base building; that is added after the tenant layouts are determined.T3 Bayside Connection DetailHines notes that T3 Bayside will store 3,886 metric tons of carbon dioxide. However, this isnt counted or credited by LEED. According to the Life Cycle Assessment (LCA) report, biogenic carbon is excluded since it is assumed that at the end of life, the wood will be disposed and the embodied carbon will be re-emitted back into the atmosphere.The treatment of biogenic carbon in LCA calculations is a major topic of discussionand controversyin both the industry and academia. Some in the industry dont believe any credit should be given for carbon being stored in the wood, given that roots are left to rot in the ground, slash is left behind, scrap is burned to kiln-dry the wood, and wood panels are transported from factory to site in fossil-fuel-powered vehicles. Others, like Paul Brannen, author of the book Timber!, claim that so much carbon is sequestered in the wood that developers should be able to sell carbon credits for every tonne stored, to help reduce the cost premium and to encourage more wood construction.Some also worry that building out of wood will lead to deforestation and the loss of old-growth timber. Hines counters by saying: The trees we use at Hines come from responsibly harvested forests/certified sustainable forests. The forests in the U.S. and Canada, for example, reproduce the timber required for T3 buildings every 20 minutes.Adding to their claims, Hines measures and mentions avoided emissions, the carbon emissions that dont happen because of the decision to go with wood. They note in a FAQ that Compared with steel or concrete, T3 Sterling Roads timber construction avoids emitting approximately 1,411 metric tons of carbon dioxide into our atmosphere. I question the idea of avoided emissions, thinking that its like being on a diet and crediting the calories of the chocolate cake I didnt eat.But any negativity disappears when you walk into either T3 Sterling Road or T3 Bayside. The spaces look good. They smell good. Fondle the columns, and they feel good. The biophilic effect is instantaneous. One may argue about the exact count of kilograms of carbon emissions stored or avoided, but as wood expert Dave Atkins noted about building materials, it all comes down to one principle: If you dont grow it, you mine it.The T3 buildings give tenants the culture, the aesthetics, the warmth, and the biophilic effects of an old warehouse building, with modern technology and services, and without the noise and dust. The carbon savings, however they are measured, are a wonderful bonus.Lloyd Alter, formerly an architect and real estate developer, is the author of The Story of Upfront Carbon (New Society Publishers). He currently writes a popular Substack newsletter, Carbon Upfront!T3 Sterling RoadCLIENT Hines | ARCHITECT TEAM DLR GroupStephen J. Cavanaugh, Kevin Curran, Kelly Goffiney, Charlie McDaniel, Bobby Larson, Kailey Smith, Neely Sutter. WZMHTed DuArte (MRAIC), Robert Sampson (MRAIC) | STRUCTURAL Magnussen Klemencic Associates | MECHANICAL/ELECTRICAL TMP | LANDSCAPE Janet Rosenberg Studio | INTERIORS Partners by Design | CONTRACTOR Ellis Don | AREA 28,234 m2 | BUDGET Withheld | COMPLETION Spring 2024ENERGY USE INTENSITY (PROJECTED) 45.6 kWh/m2/year T3 Bayside Phase 1CLIENT Hines | ARCHITECT TEAM 3XNCompetition Phase: Jens Holm, Audun Opdal, Kim Herforth Nelson, Elizabeth Nichols, Sai Ma, Monty de Luna, Sean Lyon, Matthias Altwicker; Design Phase: Jens Holm, Matthias Altwicker, Elizabeth Nichols, Laura Wagner, Sai Ma, Catherine Joseph, Jacquelyn Hecker, Ida Flche, Thomas Herve, Aleksandre Andghuladze, Farzana Hossain, Benji Magin, Christian Harald Hommelhoff Brink, Lydon Whittle, Sang Yeun Lee, Ann Christina Ravn, Thomas Lund, Eliana Nigro, Dora Lin Jiabao, Majbritt Lerche Madsen, Morten Norman Lund; Execution Phase: Matthias Altwicker, Catherine Joseph, Elizabeth Nichols, Jens Holm. WZMHRobert Sampson (MRAIC), Nicola Casciato (MRAIC), Len Abelman (MRAIC), Paul Brown, Ted DuArte (MRAIC), Nazanin Salimi, Derek Smart, Liu Liu, Ashley McKay, Samer Richani, Akhilesh Ahuja, Terek Aly, Loc Nguyen, Tracey Gaull| STRUCTURAL DESIGN Magnusson Klemencic Associates | MASS TIMBER PRODUCTION Nordic Structures | MECHANICAL The Mitchell Partnership Inc. | ELECTRICAL Mulvey & Banani | LANDSCAPE Janet Rosenberg & Studio | INTERIORS Partners by Design | CONTRACTOR Eastern Construction Company Ltd. | CODE Vortex Fire | CIVIL WSP | GEOTECHNICAL EXP | CONTROLS AND SECURITY HMA Consulting | ACOUSTICS Cerami & Associates Inc., HGC Engineering (Site Plan only) | SUSTAINABILITY Purpose Building Inc. | ENERGY MODELLING EQ Building Performance | ENVELOPE Entuitive Consulting Engineers | COMMISSIONING RWDI Consulting Engineers & Scientists | TRANSPORTATION BA Consulting Group Ltd. | WIND Gradient Wind Engineering | VERTICAL TRANSPORTATION Soberman Engineering Inc. | SIGNAGE Kramer Design Assoc. Ltd. | BUILDING MAINTENANCE EQUIPMENT RDP Engineering Inc. | AREA 23,341 m2 | BUDGET Withheld | COMPLETION Fall 2023 ENERGY USE INTENSITY (PROJECTED) 141.3 ekWh/m2/year | WATER USE INTENSITY (PROJECTED) 0.3 m3/m2/year (water use reduction of 45% compared to the LEED baseline, including greywater reuse in toilets from water collected on the roof and stored in a cistern)As appeared in the November 2024 issue of Canadian Architect magazineThe post Timber Redux appeared first on Canadian Architect.
0 Σχόλια
0 Μοιράστηκε
32 Views